Wet basement OSB in new build

Building a tract home in Syracuse NY. House has tyvek but no siding yet (a week to 10 days away). Upstairs is at the drywall mud stage. Basement is at the FG insulation stage. For about a week and a half the house was heated with a salamander propane heater which dumped a lot of humidity into the house. Plus the humidity from the mud. That heater is now replaced with a temporary furnace that is exhausted outside.
Anyway, the basement exterior wall cavities are 2x6s with an osb exterior. It has been very cold here (-9 on friday morning) and with the very humid interior air … of course I have condensation on the osb. It doesnt seem moldy but it’s wet.
I took it upon myself to pull all the FG out of the cavities this afternoon because I assume that it would be preferable to let it dry out a little bit before sheet rock goes up. The interior humidity is dropping and the exterior temps are going to be a more typical teens to 30s.
Here’s my question … am I over reacting? Should I have just left it alone and let it dry out over time? When would it be safe to re-install the FG? Maybe right before the SR goes up? Bear in mind that this is not a custom build and my builder will likely be pissed that I engaged in some self help. He’s likely to tell me that they do this all the time and that it will be fine. Any advice would be appreciated.
GBA Detail Library
A collection of one thousand construction details organized by climate and house part
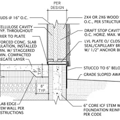
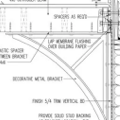
Replies
David,
Here at GBA, we hear from a homeowner like you every two or three months.
The reason that your OSB sheathing is wet is simple: the sheathing is cold, and the interior air is warm and humid. The cold OSB is a condensing surface.
The best solution is to install a sufficiently thick layer of rigid foam insulation on the exterior side of the wall sheathing. This keeps the OSB warm and dry all winter long. But in your case, it's probably too late for that.
In your case, you should probably open everything up (pull out the insulation) and wait a few months. In warmer weather, everything will dry out. Then you can insulate your stud bays and protect everything with an airtight layer of drywall. If you do a good job, your wall sheathing will stay "dry enough" -- not perfectly dry, but dry enough to avoid problems.
Your problem is common. Here are links to an article and some Q&A threads about cases almost exactly like yours:
Why Is This Sheathing Moldy?
Getting heavy condensation on the inside of the exterior boards
Basement insulation in Minnesota
Wet basement OSB sheathing
Wet basement OSB. Remedy?
The damp sheathing is more common in walls without taped drywall than in walls with taped drywall, and (obviously) more common in cold weather than warm weather. Homeowners who have an opportunity to inspect their sheathing before the drywall goes up have a rare opportunity to see with their own eyes what building scientists have been saying for years: OSB or plywood without exterior rigid foam is wetter on average than OSB or plywood with exterior rigid foam. For more information on this topic, see How to Design a Wall.
Thanks for your reply Martin.
I am familiar with the cause of the problem (warm humid air contacting a cold surface) and I am familiar with the best prevention (exterior insulation and or interior spray foam).
There is no polyethelene on the wall.
My problem is that this is a tract home, neither of those preventative measures are in the budget and even if they were my builder basically said that he doesn't want to do the exterior foam - because they have never done it before and it would probably interfere with their production line approach to building.
My question is "what should I do now?" My options are:
1- Put the FG back in the cavities after letting it dry for a day or two. In thise case teh sheetrock installation is probably 2 weeks away.
2 - Insist that the FG only go back in right before the SR goes up.
3- Try to find money in the budget now to flash and batt this area - understanding that the foam would have to adhere to a damp (maybe even wet) and cold osb surface..
Something else? I am going to have to deal with a pissed off and unconcerned builder this morning so I would like to have a plan for what to do going forward before I call him.
David,
There are two issues here: (1) the building science issue and (2) the social and contractual issue.
The building science issue is simple. Building a house in a cold climate without exterior rigid foam is an inferior approach compared to building a house with exterior rigid foam. Sometimes, when you cut corners, you experience problems.
The solution is to remove the fiberglass and wait (a) for warmer weather, and (b) for the sheathing to dry out. Once the sheathing is dry, you can insulate the bays. An approach that includes spray foam will, as you suggest, perform better than an approach that relies on fiberglass insulation alone.
The social and contractual issues are more complicated, and frankly, the decisions about how to proceed on this front are up to you. You'll need to have an honest conversation with your builder and determine how to proceed.
IMO I would just leave the FG pulled out until the last minute.
Tract builders can be tough to work with because many take the legally correct position that ultimately they own the code-minimum house until it has been completed and you simply agreed to buy it when they're done. Basically it's not all that different from ordering a car. As a buyer who has placed a substantial deposit it can be a maddening experience but the market accepts it.
Clearly the builder is on a timetable so it's doubtful that they'll wait until it gets warmer. The timetable is one of the ways in which they save you money.
What means " Basement is at the FG insulation stage. "???
Fiberglass insulation has some risks for below grade foundations, since it needs to deal with both ground moisture drives and interior humidity drives. An interior side vapor barrier would trap ground moisture in the fiberglass (and presumably, studs.) With very dry soil and sufficient above grade exposure to dry toward the exterior the risk can be pretty low, but in locations such as Syracuse prone to heavy lake effect snows and saturated ground the risk of creating indoor mold farms is pretty real.
A somewhat standard solution is to put sufficient foam for wintertime dew point control for above-grade walls (per IRC chapter 7 prescriptive) between the foundation and the studs & fiberglas for the amount of fiberglass being installed, and using only class-III vapor retarders on the interior. The vapor retardency of the foam mitigates ground moisture drives, the relatively vapor open interior allows it to dry toward the interior, and the R value of the foam avoid condensation or frost at the foam/fiber interface on the part where the concrete is above grade. That would also bring the basement insulation slightly ahead of code minimum performance.
Syracuse (Onondaga County) is the warm edge of US climate zone 6, so a 2x4/R13 insulated studwall against the foundation would need R7.5 foam between the studs/fiberglass and concrete. See TABLE 702.7.1 CLASS III VAPOR RETARDERS :
http://codes.iccsafe.org/app/book/content/2015-I-Codes/2015%20IRC%20HTML/Chapter%207.html
A couple inches of EPS, or 1.5' of foil faced polyiso is recommended.
If the studs are already up and you're going to punt, using 2-mil nylon (Certainteed MemBrain) instead of polyethylene on the interior side of the studs can mitigate some of the risk.
You're in a tough situation. For our house (zone 6), we ran a small inexpensive (< $200) dehumidifier to reduce humidity levels during winter construction. You'll of course have to monitor it and empty the tank each day. This won't solve your issues, but it will help keep your (most likely high) indoor humidity levels in check.
By "Basement is at the FG insulation stage" I mean that the above ground wood framed portion of the basement walls have FG in them. The poured concrete portion of those walls has R10 foam and will get FG in the 2x4 framed wall.
I looked into flashing the OSB between the studs with spray foam but between the cold and moisture, the foam would likely not cure or adhere well.
Now considering cutting sheet foam and installing 1-2 inches of that against the wet OSB and then reinstalling the FG. If I do that the OSB will only be able to dry to the outside, and likely not until spring.