We have risky assemblies. Is our humidity and vapor control strategy sufficient?

We are first-time homebuilders, building on a budget in NY state in a tense and overloaded time for construction. Finding competent and affordable design help proved to be a major challenge, so our framing company did most of our assembly design. They’re great framers, but I’m not sure they’re totally with it on managing moisture concerns, and we’ve landed on some assemblies that I’ve seen deemed risky on this forum. I’m laying the assemblies and our risk-mitigation thoughts here and welcome your feedback.
Context: House is on a slab, 2.5 stories, ~1000 sq ft footprint, in zone 5b or 6. We have Zip sheathing acting as a continuous exterior air barrier in the house. We asked for this, and the builders were willing to do the “tacked on rafter tail” thing for us. We expect to get this house well air sealed on the outside.
1. Exterior Walls: Zip R3 sheathing over 2×6 framing (24″ OC), with dense-pack cellulose in the cavities (R21 + 3). We didn’t ask for zip R3, but the builders made a mistake and ordered it, so we get to have an extra R3 and thermal break for no charge, but need to think about managing moisture in our walls. FYI, exterior insulation is still only for millionaires around here. No builder we talked to could or wanted to do it. We intend to finish with drywall and vapor-blocking paint, monitor humidity and use a dehumidifier if needed. Does this sound like a reasonable strategy to control risks?
2. Roof: We have a single-gable cathedral ceiling, designed as 16″ parallel chord trusses with zip sheathing on top. Yes, we’ve done the tricky thing and designed a cathedral ceiling. We intended to fill this with cellulose, finish it with Intello Plus, and plan for zero penetrations by plumbing or electrical to keep air from the living space from entering. We are also thinking to make a vent channel on top of the zip sheathing, under metal roofing, and vent that channel at the soffits and ridge. Again, we also plan to monitor humidity and dehumidify as needed to keep the house in a safe range. Still too risky? Must we also put a ton of rigid foam on top of the roof to make it safe? Or install vent baffles and a vapor diffusion port at the ridge?
Thanks you all — this site has helped us a lot already in getting literate on these concepts.
GBA Detail Library
A collection of one thousand construction details organized by climate and house part
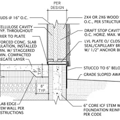
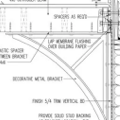
Replies
Faith,
I'll leave it to others to comment on what level of interior vapour-retarder you need to make the walls safe. Akos has posted links on that in past discussions. It's very doable.
The roof as you suggest building it is a problem, both from a practical and code perspective. You can not fill the rafter bays with permeable insulation unless you have either a vent channel below the sheathing, or exterior insulation. Your best bet is to choose among these five assemblies:
https://www.greenbuildingadvisor.com/article/five-cathedral-ceilings-that-work
With a parallel chord truss you should have plenty of room for both a vent channel and insulation. I would go with faced batt insulation, since you have 16" spacing that should be easy to source and easy to install. Then install a ridge vent and a soffit vent. (I'm assuming that when you say "16" parallel chord trusses" the 16" is the spacing.)
It would be hard to blow insulation in that space and since you're blowing blind I would worry about leaving gaps.
This is the closes assembly I can find:
http://effectiver.ca/calculator/wall.php?id=4319
Pretty close to your Zip R setup, it will work in your climte provided you have a warm side vapor retarder. VR paint can work but a variable perm membrane will work better plus give you a secondary side air barrier that is easy to inspect before the drywall goes on.
As for the roof, a top vented roof is not the same as a regular vented roof as all the vapor needs to move through roof deck.
This has come up before ie:
https://www.greenbuildingadvisor.com/question/exposed-fastener-metal-roof-better-than-standing-seam-for-drying
TLDR, can work, not as robust as regular vented roof. You need a solid vent channel above the roof deck and a 2nd roof deck over that. A large vapor diffusion port (high perm membrane or replace strip of the roof deck with densglass) at the ridge is also a good idea.
Depending your overhang length and snow load, the vent space can be formed by either 2x4 on flat or 2x4 on edge. You can extend these past your walls to form your overhang avoiding any monkeying with bolt on overhangs.
Thanks very much, you all. I've seen pieces of this info before but had difficulty connecting the dots. This seems pretty clear, and we've adjusted to a vented assembly (#1 in the handy guide linked above).
For the walls, your plan to monitor humidity and use a dehumidifier could help, though it’s important to ensure that moisture doesn't accumulate behind the vapor-blocking paint. As for the roof, the vent channel under the metal roofing is a good idea, but incorporating rigid foam or vapor diffusion ports could offer extra protection.