We are considering the following insulation strategy for a second story addition; does this cause any potential problems?

We are looking at the following wall insulation profile for a second story addition, considering cost, R-value and air sealing. The walls will be constructed with 2×6 framing. Starting from the interior: 1/2 gyp. board, 2″ dense pack cellulose, 3.5″ closed cell spray foam, 1/2″ plywood sheathing, vapor barrier, 1″ XPS foam board, cedar shingles.
For the ceilings we are considering 15” of blow-in cellulose.
GBA Detail Library
A collection of one thousand construction details organized by climate and house part
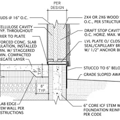
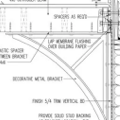
Replies
I forgot to mention we are insulation zone 6 in the central US
A myriad of potential problems.
1) sandwiching the sheathing between two impermeable layers is a recipe for disaster
2) the vapor barrier, or more properly vapor retarder, goes on the inside in a cold climate (but you probably mean housewrap or weather-resistant barrier or air barrier and not exterior vapor barrier)
3) spraying an irregular 3.5" of foam will not leave a sufficiently open cavity to blow cellulose - you may be able to do a damp spray, but with exterior foam there's no reason not to fill the cavities with dense pack cellulose
4) cedar shingles should not be applied directly over foam board - there must be furring strips and a rainscreen cavity to allow drying to the backside
There are simpler and better ways to accomplish your goals. What is your climate zone?
David, Robert nailed the main issue I saw with #4, & the slight mis-wording on #2
Speaking of #2 though - I noticed there is no vapor barrier inside which is fine based on the way you are building the wall, my only question is do you need another 1" of foam on the outside to guarantee you that the failure point is outside the wall
#3 is also correct for the most part, but then you would definitely need to have more foam outside - I actually like how you are planning on doing it as there have been issues with foam panels before & this helps guarantee your insulation values
Robert as for #1 - it is not an issue when done right & some XPS foam as I recall is also permeable / allows drying
Why not either:
1) 5-1/2" dense pack cellulose in the wall cavities, 2" of XPS over the sheathing with felt, furring strings and shingles outside, or
2) ~5-1/2" of ccspf in the wall cavities, with felt, Homeslicker, and shingles outside.
David,
Well, at least you have a good plan for insulating your ceiling.
I agree with Robert, however, that you need to come up with changes to your wall design.
1" of XPS is, according to the current classification of vapor retarders, vapor semi-impermeable (≤1 perm). But, more pertinently, it not only restricts drying potential to the outside but also keeps the sheathing somewhat warmer, which potentially puts it into the mold/decay danger zone for some part of the year.
"When done right" can be more wishful thinking than likelihood, since preventing moisture problems in a wall assembly with relatively impermeable layers on both sides requires perfection of initial installation, perfect long-term maintenance, and no unusual weather events that might violate the integrity of the shell.
Thank you for all the prompt responses. We are located in Minneapolis, MN which I believe is zone 6. We are in the process of getting bids for our remodeling project. I have read many articles from fine home building and other periodicals from which it seems there is little consensus on the “best” options for insulation. To respond directly to Robert:
1) The 1st reason for the exterior foam board was an attempt to reduce thermal bridging. Secondly, to add to the overall R value of the wall. And lastly, to add additional air-sealing. I have seen the spray foam/sheathing/foam board in several Fine Home Building articles.
2) Yes, Robert is correct I meant house wrap.
3) The reason for combining spray foam and dense pack cellulose was to gain the additional R value and air-sealing from the foam and reduce cost by using (yes damp spray) cellulose to fill the remainder of the cavity which also eliminates the cost of removing any spray foam over spray. I intentionally specified a thicker layer of spray foam rather than a flash coat because I was concerned about creating a condensation layer in the interior of the wall.
4) Would a mesh rain screen be sufficient behind the cedar shingles? Or would I still need the furring strips?
Thank you for the other responses as well. Given this additional information for what we are trying to accomplish and our climate zone what would be the recommended wall profile?
David,
Since this is new construction, all possible options are available. The greenest option that would satisfy all your concerns and goals would be a double-stud or parallel-chord truss wall, as deep as you'd like, filled with densepack cellulose (avoid damp spray, since it adds too much moisture) and sealed with air-tight drywall on the interior with latex vapor retarder primer.
The exterior could then be a simple as plywood sheathing (avoid OSB because of its moisture vulnerability and insufficient vapor permeance), a weather barrier/rainscreen membrane like Home Slicker with Typar, and cedar shingles. You would also be fine with traditional #15 felt (which in some ways is superior to all the plastic membranes). It's best to not put cedar directly on a polymeric WRB because the extractives can reduce the surface tension and encourage water infiltration.
Again, thank you Robert.
As the home owner I am also concerned about losing interior square footage, hence one of the reasons for the addition. I have even received some hesitance from some of our possible contractors in using 24” OC wall studs (again to reduce thermal bridging and reduce framing costs). One contractor wanted to increase the thickness of the sheathing and gypsum board because he was concerned about the possibility of the walls warping. Obviously this would not be a concern with a 16” OC double-stud or parallel-chord truss wall as you suggested. I just do not want to lose that additional sqaure footage required to constuct that type of wall (which is the other reason I was proposing the exterior foam board). In your opinion what are the better options for 24” OC 2x6 wall framing. As off topic as this may be, with spray foam providing the best R-value, I have 2 young daughters aged 1 and 4 should I be concerned about possible health concerns?
David,
Installing exterior foam sheathing to cut down on thermal bridging is a good idea. Be sure it is thick enough to keep your plywood sheathing above the dew point: in Minneapolis, a 2x6 wall needs foam sheathing with a minimum R-value of R-11.25. (More on this topic here: Calculating the Minimum Thickness of Rigid Foam Sheathing.
Once you've decided to install exterior rigid foam, you shouldn't use spray foam with a low vapor permeance on the interior side of the sheathing. I suggest you fill your 2x6 stud bays with cellulose.
Hesitant to frame 24" OC with 2x6? That sounds a bit odd...
In the most basic sense it seems I have two options. One, spray foam the 2x6 wall for and an approximate R-value of 33 not considering thermal bridging. Two, use blown in dense pack cellulose with an R-value of 19 again not including thermal bridging but with the possibility of adding 2” of polyiso (R-12) to the exterior. It seems that option two would provide the best whole wall R-value when considering thermal bridging. Another option I was considering was spray foam in 2x6 framing with 1 inch exterior horizontal furring, approximate R-value of 39. Is this an option our would I see similar issues with only 1 inch of additional spray foam causing condensation on the exterior of the framing?
David,
I vote for the dense-packed cellulose in the stud bays, with 2 inches of exterior polyiso to address thermal bridging through the studs.
Your last question is confusing. You ask about "spray foam in 2x6 framing with 1 inch exterior horizontal furring, approximate R-value of 39. Is this an option our would I see similar issues with only 1 inch of additional spray foam causing condensation on the exterior of the framing?"
1. I think your assumption that your spray foam has an R-value of R-7 per inch is overly optimistic. R-6.5 per inch is more realistic for closed-cell spray polyurethane foam.
2. Your question about "only 1 inch of additional spray foam causing condensation on the exterior of the framing" is confusing. Is the plan to install 1 inch of spray foam on the exterior side of your plywood? How is that spray foam integrated with your proposed horizontal furring?
If you are located in Minneapolis, then 1 inch of closed-cell spray foam is not enough on the exterior of the sheathing -- as I wrote earlier, you want a minimum of R-11.25 -- and in any case you don't want to create a foam sandwich, with plywood sandwiched between two layers of foam.
Martin,
Let me explain more clearly. The 1" furring strips would be attached horizontally to the exterior of the 2x6 wall studs then the sheathing would be applied. The spray foam applied from the interior would then also fill the 1" gap (created by the horizontal furring) between the 2x6 and the sheathing. So the spay foam thickness could be 6.5" except where the furring attaches to the 2X6. 6 X 6.5 = 39
David,
OK, I got it.
I bet that the solution you just described will cost more than 2" exterior polyiso plus dense-packed cellulose.
Many interesting ideas... 6.5" CC spray foam sprayed in multiple layers... better be done right... wrong is a horror story. And... sounds super expensive unless your sprayer cheats the install.
Neat idea the horizontal strapping to the outside, its been done to the inside quite a bit. I bet the building inspector would be scratching his head on that one in most jurisdictions.
Robert, tell us what you think structurally about the exterior sheathing being acceptable to carry shear wind shear loading if nailed to horizontal furring.
You might get away with attaching structural sheathing to 1½" strapping (KD 2x4 flat with full 1½" nail penetration) but certainly not to nominal or actual 1" strapping.
adding to my preceding post.
CC foam would of course make the horizontal furring strip wall able to handle shear loads. So say the case was Icynene or some non structural fill. And still the question of codes ... most likely would have to find an engineer to approve the assembly or use angle bracing so as to obtain building permits?
That is more of an advertising slogan than a demonstrated fact. Rigid foam certainly stiffens an assembly, at least initially until the foam shrinks or degrades, but it won't meet any code standard on shear bracing.
On the other hand, interior drywall is counted toward the shear resistance of a wall system, at a conservative 100 plf.
You will want to put the vapor barrier on the inside of the wall, closest to the heated space. Probably in the form of a semi permeable paint. The moisture barrier should go on the outside, on top of your plywood and under the 1" foam board.
It is very important to understand the difference between vapor and moisture.
David,
I disagree with GreenGuy. None of the wall options under discussion will benefit from an interior vapor barrier. Don't do it.
Vapor-retarder paint is all you need.
So if I decided to go with closed cell spray foam in the 2x6 cavity, according to http://www.cedarbureau.org I would just need 30# felt on the exterior sheathing behind the cedar shingles. On the interior would I just need drywall with a vapor-retarding primer?
If I decide to go with the cellulose cavity and 2” of exterior foam board, again I could use felt but would need the additional horizontal furring to provide a nailing base for the cedar shingles. The furring strips have a secondary benefit of increasing air circulation behind the shingles. On the interior I would again use drywall a vapor-retarding primer.
In both cases plywood would be a superior option for the exterior sheathing.