Water pipes under exterior foam?

I’m in Climate Zone 2B and live in a house with slump block walls and a flat roof w/ no attic. The house was re-plumbed by the previous owner by running the water lines across the roof. With radiant losses, the roof gets cold enough to risk freezing the pipes 20-30 nights a year. Standard box store pipe wrap was not sufficient to keep the pipes from freezing. (I’ve dealt with it up to now by shutting off the water supply and draining the pipes on these nights.) The supply lines come in near the front of the house, where the kitchen is; the water heater and laundry are at the back of the house, more than 50 feet away. The side yards in between are grouted flagstone, so there’s no easy way to bury the lines. The bathrooms are served from the hot water heater by lines that go over the roof, penetrate the roof overhangs and then follow the back exterior walls until they reach their destinations.
I thought about recirculating pumps but I’d prefer to get the lines off the roof to minimize roof penetrations and simplify future re-roofing. I am planning to put 2-4 inches of foam on the outside of the exterior block walls as part of an energy retrofit. I haven’t decided yet about the final siding, but stucco is most common here. Would it be foolish to mount new plumbing lines to the exterior walls and bury them permanently under the foam?
My instinct (and lack of trust in my DIY skill) says yes, so I’ve been pondering ways to make the pipe accessible for repairs. One possibility (based on reading) seems to be to run PEX in a sleeve under the foam, to make it easier to replace in the event of failure. Another thought is to terminate the new foam/siding assembly six inches above the ground and build some kind of insulated, accessible channel in which to run utilities (I want to bring some dedicated electrical circuits to the front of the house, one of which will serve a tankless heater for the kitchen sink).
Thanks in advance for any advice!
GBA Detail Library
A collection of one thousand construction details organized by climate and house part
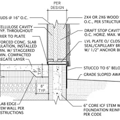
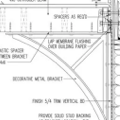
Replies
The plumbing in question is currently ABOVE the roof, fully exposed to the elements (except for the pipe insulation)???
Adding 4" of foam on the exterior of a CMU wall would be FOUR+ TIMES the code minimum R4 under IRC 2015 for mass walls:
https://up.codes/viewer/utah/int_residential_code_2015/chapter/11/re-energy-efficiency#N1102.1.2
Even 2" of EPS would be 2x code, both easier & cheaper to build than 4" of exterior foam.
The concept of an insulated air sealed electrical & plumbing chase (vertical or horizontal) makes sense, but it will work better when the insulation of the chase is continuous with the wall insulation, without the substantial thermal bridging of the CMU. A horizontal chase near the ground is easier to access, but more exposed to degradation from elements than building the insulated chase under the roof overhangs. My personal instincts would be to put the horizontal chase near the top of the wall, behind a removable facia board, protected by roof overhangs. As long as there is at least 1" of foam behind the facia board it'll still meet code minimum, so it needn't be hanging an unaesthetically far distance out from the plane of your siding. Be sure to insulate the top of the chase with at least 2" of foam so that the radiation-cooled roof doesn't still cause it to freeze during colder weather.
Can we assume this house has a slab on grade foundation?
Thanks Dana. The answers to your beginning and ending questions are both yes - pipes fully exposed to the elements, slab on grade foundation. I'm now spending what I saved buying the cheapest house in the neighborhood!
Thanks for pointing out the excess on the foam... I'll redirect that part of the budget to put more foam on the roof.
I have access to some nifty foam channeling tools, so I'm thinking I could glue 2" EPS to the back of the fascia, channel out just the space I need (an inch or less) for the utility runs, run my lines and attach the assembly to the CMU just below the roof overhang. Then everything will line up neatly with the 2 inch foam the rest of the wall will get, with the fascia proud of the foam but more or less where I want it for future siding.
If you haven't already discovered this fact, there is a lot of surplus reclaimed foam from commercial building demolition out there, often in near perfect shape at about a quarter to a third the cost of virgin stock foam. These folks are on the pricey side compared to what reclaimed & surplus foam costs in my neighborhood, but still cheaper than distributor retail:
https://phoenix.craigslist.org/cph/mat/d/special-on-extruded/6354868529.html
https://phoenix.craigslist.org/cph/mat/d/rmax-thermasheath-foam-board/6355035682.html
https://phoenix.craigslist.org/cph/mat/d/rigid-insulation-22-inches/6339031668.html
If you search your local craigslist occasionally for the terms rigid + insulation you can probably find it cheaper. If know what you want need a whole truckload you may get it through Nationwide Foam ( http://www.nationwidefoam.com/ ) for less, even or Repurposed Materials Inc ( https://www.repurposedmaterialsinc.com/Used-EPS-Insulation ) after shipping from the nearest regional depot.
There's no foam product greener than re-using existing foam.
Thanks again Dana. I would have thought there would be lots of cheap recycled foam coming out of all the flat industrial roofs in Phoenix, but so far I haven't found it. The third Craigslist link is within a penny per inch-ft2 of Home Depot bulk pricing, and the second one is 50% more! I'm all for re-using foam, but I'm not inclined to rent a truck and spend 5 hours on the highway and pay retail prices for it. Since my roof order will just about fill a 28 foot trailer, maybe one of the national recyclers will make me a deal when I'm ready. In the meantime, I'll keep an eye on our local Craigslist.
Everyone should have a friend down the street with 8' X 8' X 16' blocks of EPS and a computer-driven hot wire cutter. Thank you Dave Taggett of Mikey Block (ICFs)!