Want to learn about AAC – Hebel Block

I am considering using Autoclaved aerated concrete on a new home and would like to hear about others experience with the product. I will be working in a mixed-humid climate.
GBA Detail Library
A collection of one thousand construction details organized by climate and house part
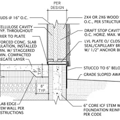
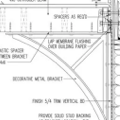
Replies
Carl
We looked into AAC and toured job sites where it was being used and checked with homeowners who had it in their homes and came to the conclusion that it was not a system that we were comfortable using in North Carolina.
The key was the lack of weather plane / drainage plane separation. The way they were installing windows was to set a treated wood frame in the opening, line it with Ice-and-Watershield strips no more than 16" wide, set the window and then just embed the strips in the stucco veneer. no provision for the stucco to fail, no drainage plane behind the stucco, nothing but AAC between the back of the stucco and the interior of the house, which was sheetrock applied directly to the AAC with plastic expansion anchors.
We have been hearing about window rot problems due to this lack of moisture management but I have not actually verified this.
The stuff seems to perform well from a durability perspective but you need to pour in concrete columns to support point loads. Through wall penetrations for plumbing or wiring or porch roof connections seem like they would be impossible to flash correctly without a drainage plane and carving it up for wiring channels seems tedious at a minimum.
The AAC sales people point out that it's "worked great for years in Europe" but I'm skeptical that it's going to translate to working great in North Carolina. We have horizontal rain and air conditioning in the summer and cold dry air outside and warm damp inside in the winter. Too much vapor drive and weather extremes.
We ended up using an ICF stem wall for the slab edge with a double framed wall above the floor. In this case the exterior foam of the ICF was too thick to provide adequate load transfer from a 2x4 wall to the concrete core of the ICF so we used a 2x6 exterior wall with 2 1/2" horizontal strapping and a 2x4 interior wall and 2x12 upper top plate to tie it all together and provide fire blocking. Insulation was 12" JM spider but could have been BIBS. I am enough of a curmudgeon myself that I refuse to install cellulose in walls in NC due to it's moisture holding potential. It's an R-46 wall that the electricians and plumbers love. We'll spray 8" of open cell foam under the roof deck to top it out.
We specified stucco as an exterior siding over drain wrap and tar paper so it looks like an AAC or ICF house. We had the walls table framed and sheathed at a local panelization plant and trussed the second floor and roof. the whole thing was up with tar paper on the roof in less than two weeks from a buildable slab. Do that with ICF or AAC! I can dig up the cost of the wall panels if you want but it was cheep and the embodied energy content was much less than AAC (which has both aluminum and also portland cement) or ICF's which are obviously full of cement and all the embodied energy there.
I've sent the drawings in to GBA for addition to their detail library. Next time round I would use a lighter ICF on the foundation so I could get away with a 2x4 exterior wall and a 3 1/2" strapping for a better thermal break and less cost.
I will now step away from my soapbox and let all the AAC and ICF partisans throw rotten vegetables at me.
m
Thanks for the feedback. AAC has obviously not caught on here, I have yet to hear from anyone who has actually used it in a house. I really like the idea of a mass material that has thermal and moisture management capabilities built in to it. I tend to not be terribly cautious about trying new products, so if I can figure this out, I may go ahead and try it. It will be for my personal house, so I won't have anyone complaining to me, in any case.
We are building an AAC cottage with attached garage in a northern climate. Finding no one with experience building with this material, we raised the walls ourselves. Using a laser level the walls were right on. The wall system is elegant - meaning functional, effective, and a clean sandwich design. The interior is plaster. The exterior has a layer of foam and cedar siding and stone. We did not find it difficult to rout lines for the wiring. In the small utility room, it was big advantage for the contractors to be able to mount hardware without having to search for studs. In the bathroom, the walls were tiled over the block and we used a narrower block for half height walls around the shower. I do not have complete records on utilities yet - but it is performing well as we make progress. The heating system is an in-floor radiant system and we have a small wood stove/fireplace with an exterior air-intake. We like the AAC. It provides a very solid feel. I like not having to use drywall everywhere. The southern exposure and thermal mass add even more efficiency. There are additional advantages of AAC...
We have been building with ICF Blocks since 2002 and have completed approximately 170 townhomes and single family homes alike. We have a fairly dry climate in SE Washington State but experience all four seasons during the year. ICF's allow us to completely control air infiltration, and offer a recongized R-value that contributes significantly to our abiilty to meet the $2,000 frederal tax credit requirements. As with any single "signature" building system, wheather it be SIP'S, ICF's, geothermal, or wind power for example, I have found that incorporating basic building science, along with quality control, applied to all aspects of what goes on with the shell and mechanical system, are what allow for peak performance at the lowest price point.
Example; Guy comes to my shop looking for one of those new vertical wind turbines as seen on Jay Leno's green garage. this Guy already has geothermal heating and is looking for more high tech (and usually more expensive) technology for his home. I asked him if he sealed his interior walls and sheetrock penetrations, had a basic blower door test on his home, checked for minimum ventilation or had the ducts in his HVAC system sealed. He had not. My point is that all the high tech he is installing is going to significantly under perform because he didn't follow basic steps as outlined in most of the country's basic "Energy Star" programs.
Incendently, we build with ICF over a standard foundation. We insulate the outside of the foundation instead of the inside so that the foam on the block lines up with the 2" foam on the outside of foundation. This allows the 6" core of the ICF to line up with a standard 6" foundation wall / concrete slab. It takes three guys 4-5 days to set and pour the ICF walls (including cleanup) with a total factored additional cost to the home of around $8,000. With ICF's as the starting point, we continue by meeting the "Northwest Energy Star" requirements, and complete the project using E-Stars MPV (Mistake Proof Verification) system to insure a high quality install on all componants. the end result is $40 power bills and $20 gas bills on homes ranging from 1,650 sq ft to 2,200 sq ft. While individual owner habits cause some homes to have high bills, "ALL' our homeowners are very happy with their power bills and the lower bills are definately not unusual.
Hopefully this info shows that energy efficiency can be affordable. This formula is definately working for us!
I designed an AAC block for a two-story residence in a hot-humid climate ten years ago, and yes, there were one or two places where the windows were not detailed properly, but those were quickly fixed and the owners are still very much pleased with the material. I am in the blueprint phase for another AAC residence close to the Texas coast (hurricane region) that will incorporate the AAC planks for the floor and roof to incorporate with the AAC block walls. The roof will also be vegetated. As the previous answer stated, it's important that the installer and contractor are familiar with the slightly different detailing required at penetrations, but the material itself is very dimensionally stable, easy to work (bandsaw is the primary tool for block trimming), and not having wall cavities or worry about fire or termites is icing on the cake.
I have build a few houses as a builder in different areas ( southwest florida , Georgia )
since 1996 and all the owner are very happy with the results, very low energy bill, no bug probleme, no sound transmission from one room to another, just to name a few. I personal live in my house since 1999 what I have build out of AAC nad my energy bill is not even 1/3 of my neighbors with Concrete block and old style frame houses. my house is completly build with AAC blocks no stud walls no sheet rock ( drywall) on the walls, interior wall finish is plaster direct on the block , exterior is regular stucco direct on the blocks too. sure it was difficult for the plumber and electrician because they could not see the whole house from every place in the house. I did the routing of the chanel by my self with a special made tool in all the houses what I have build and even drilled the holes for the down rods up to 10 feet hight. I have build many houses in germany where I am from too.
I f somebody have a question just draw a line at [email protected]
WHAT IS THE R-VALUE ON A 8" X 8" X 24" HEBEL BLOCK WALL THAT 1/2" SHEETROCK IS GLUED TO IT INSIDE
Dave,
The R-value of an 8-inch Hebel block depends on its density; the manufacturer makes three different densities.
Here are the R-values for the different 8-inch blocks:
AAC 2400 series: R-10.85
AAC 4500 series: R-9.1
AAC 4600 series: R-8.9
Note that these R-values are for the entire 8-inch block; these are not the R-values per inch.
Half-inch drywall has a negligible R-value.