Walls for very cold climate

We’re building a post-and-beam home in the Colorado mountains (Zone 7) and have an insulation dilemma. I’ve read a lot of articles here, but haven’t been able to determine the solution to our energy efficiency problem.
The panels between the posts are currently designed as: exterior log paneling (2″), wrap, osb sheathing, 2×6 studs filled with open cell foam, interior finishes (gypsum or osb/paneling). We would like to improve the overall R-value, but can’t add a great deal of thickness to the wall for appearance reasons with the post-and-beam style. Builder suggesting we replace wrap/osb with either 1.5″ Zip-R panels or 1″ Tuff-R panels to break thermal bridging and add continuous insulation R-value. This is about the thickest material the design will tolerate. If the cavity insulation remains open cell foam, doesn’t that potentially create a condensation point on the inside of the sheathing? Should we consider backing the sheathing with 2″ of closed cell foam and then fill the rest of the cavity with either open cell foam or other materials?
What are people’s experiences with Zip-R or Tuff-R insulating products?
J.J.
GBA Detail Library
A collection of one thousand construction details organized by climate and house part
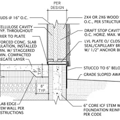
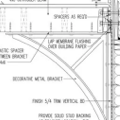
Replies
J.J.,
There are several issues here.
First, are you assembling wall panels to be inserted between the posts? If so, that's a very problematic approach, associated with air leakage at the vertical cracks between the wall panels and the posts.
You absolutely need a continuous layer of exterior insulation -- rigid foam or mineral wool -- that spans the cracks between the posts and the inset panels. The thicker the insulation, the better. You also need a continuous exterior air barrier that spans those cracks.
If your Zip-R panels are continuous, covering the posts as well as the inset panels, it's better than nothing. Ideally, though, any continuous insulation installed on the exterior side of 2x6 walls in Climate Zone 7 would have a minimum R-value of R-15. (To read why, see Calculating the Minimum Thickness of Rigid Foam Sheathing.)
A 1.5-inch-thick Zip R sheathing panel has an R-value of only R-6.6, which isn't enough to keep your wall out of trouble. That said, if you insulate between the studs with open-cell spray foam, and if you include an interior smart retarder with variable vapor permeance, you could probably get away with this not-quite-right wall design.
Martin,
Thank you for your thoughts. If I might add a few more details, we can probably get to the 'best' solution.
The posts are 14" fir and will be exposed both inside and outside the house for appearance. The wall panels will be custom constructed between the posts individually, not as inserts. Close attention will be paid to those connections to protect against leakage. The continuous insulation (which is not code in our rural county), would not cover the posts.
If we use Zip-R or Tuff-R and back it with closed cell foam in the cavities, the thought is that R15+ could be achieved because it would be continuous foam with no osb in the middle. So would that work with the cavities being finished flash-and-batt? Or are you recommending Zip-R plus open cell foam in the whole cavity plus smart retarder? Are the two options viable, and if so then it is a cost trade?
I've read many of your articles on this already and appreciate the vast knowledge you have compiled on this topic. It's very informative.
J.J.
User...687,
Unfortunately, once you make the decision to have a continuous timber structure exposed on both sides you are really behind the eight ball, both in terms of energy efficiency and moisture management of your building envelope.
This problem crops up quite regularly, I think because timber frame builders tend to have gone into the trade because they love complex carpentry, not building science.
There are a number of ways the post and beam frame can be modified to mitigate the problem, but I'm assuming that you already committed to the size and construction details of your timber structure. Given that, I would suggest finding a designer familiar with how to best detail the timber/conventional framing intersection and have them provide specific drawings for each situation.
J.J.,
I agree with Malcolm, who wrote, "once you make the decision to have a continuous timber structure exposed on both sides you are really behind the eight ball, both in terms of energy efficiency and moisture management of your building envelope."
I would go further than Malcolm, noting that you are really behind the eight ball in terms of airtightness as well.
During the winter, your timbers will be exposed to cold dry conditions on the exterior, and hot humid conditions on the interior. This will cause the timbers to warp and twist. The posts will want to pull away from your wall panels, as well as push against them, as humidity levels and temperatures change.
During the summer, your timbers will be exposed to hot humid conditions on the exterior, and cool dry conditions on the interior. Now the timbers will want to warp and twist in the opposite direction from their wintertime warpage.
This is a wall without a continuous air barrier and without a continuous layer of insulation.
Moreover, the timbers will be exposed to wind-driven rain and splashback, and will eventually get punky in the areas of your envelope that get the most exposure to rain and snow.
If you value your expensive timber frame, you should wrap it in an air barrier and continuous insulation. No one wants to see timbers on the exterior of your building.
JJ,
If you want the appearance of timber frame, but want a high performance wall, you could put the timbers on the interior. Put "decorative" shallow timbers/lumber on the exterior, as part of the exterior cladding (if you prefer that specific exterior appearance). Or just the exterior log paneling. There are plenty of options to create an insulated wall between the real interior timber frame and the exterior cladding.
Better to invest in a new home with sufficient insulation, air-sealing and no moisture issues, as well as attractive on the interior and exterior.
Robert,
I think we are doing much of what you suggest. The exterior will be clad with 2" sawn timbers to give a log-home look, but we avoided full log construction for a variety of reasons. About every 20', there will be a vertical 14" diameter post. What I want to optimize is the wall's thermal properties.
I'm mostly trying to understand whether a polyiso sheathing panel backed by either CCF or OCF will be effective in avoiding dewpoint problems. Is the OCF too permeable so it could have freezing occurring mid-way through the materials?
JJ
JJ,
To avoid moisture problems in a wall assembly clad with Zip R sheathing that is too thin to meet the usual foam-to-fluffy ratio guidelines, I would recommend the use of closed-cell spray foam against the interior side of the Zip R to raise the R-value of the Zip R + spray foam layer to the minimum requirements.
Good luck.
I'd replace the Zip R with plywood, then interior side polyiso and taped foil. This follows the alternative "much more breathable to the cold side" model and provides a little less thermal bridging (warm polyiso outperforms cold EPS at a given thickness).
Or use 2x4s to get space for enough external foam - outside the sheathing, not Zip R.
I expect that your only hope for reasonable air sealing is gaskets.