Wall section? Attic insulation? Energy / Moisture / Storm

All,
I’m a licensed GC designing an addition to my personal residence which we built in the late 80s. The original house was built with 2×6 studs and might very well have been the first house built in NC with a sealed crawl space. (I gave my building inspector a copy of a sealed crawl space article by the TVA, and he OK’d the sealed crawl space.)
I would greatly appreciate some input on a couple aspects of the design.
Thanks,
Bill
Project synopsis:
Project consists of an addition (den / guest bedroom & bathroom) as well as an exterior renovation (siding, windows, doors, roofing) of the existing house.
Energy: NC Zone 4A, immediately adjacent to 3A. Energy goal is to get close to net zero with PV panels. Addition will include wood stove. We live on an 80 acre farm, 60% wooded, that typically generates more than enough firewood in a year to heat the house from down stormed trees, pruning, etc.
Storm Resistance: Guest bedroom / bathroom will be built to high levels of storm resistance, possibly to the levels of a FEMA Storm Room. The FEMA details call for a double layer of 3/4″ plywood with a layer of 14 ga steel for impact resistance, and FEMA rated storm doors and window shutters. I will not sell this house as having a “storm room” unless I meet all the FEMA specs.
The addition will be built with a crawl space (which is a variation from the FEMA plans) and a bonus room on the second story. The crawl space walls will be Ivany block with both vertical and horizontal rebar. The footings will be deeper, wider and thicker than required by code.
My initial questions are:
1) Re the wall sections for the guest bedroom/bathroom, will the following wall section perform well as far as energy / moisture?
From exterior to interior: Vinyl siding (200 mph rated) / Housewrap / 3/4″ plywood / Double layer of 1/2″ foam / 3/4′ plywood / 14 ga steel plate / 2×6 studs @ 16′ oc with unfaced fiberglass batts / GWB. I may go with a double layer of 3/4″ foam instead of 1/2″.
Would there be a better location for the steel plate as far as moisture control?
What type of foam would be best?
Since this wall section would have to have some drying capability to the exterior, what should I look for in a house wrap?
2) Re attic (story and a half semi-conditioned bonus room), would a vented roof system or sealed perform best?
The 1st story ceiling / 2nd story floor will be a full floor system with a perimeter band joist and floor sheathing covering the entire deck including band joist. Rafters will bear on a 2×6 plate on top of the floor sheathing. Overhangs at the eves will be “scabbed on”.
Roofing will be galvalume metal roof panels.
GBA Detail Library
A collection of one thousand construction details organized by climate and house part
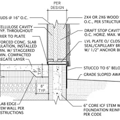
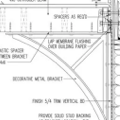
Replies
PS:
Air barrier would be by taping both layers of foam. Both layers of plywood and the foam would extend down and lap both the 1st and 2nd story band joists.
Drywall would include airtight details as overkill.
The steel is on all of the wall? I would try to get the steel adjacent to the air barrier and it will also also be a moisture barrier having no perm. Then set up the rest of the layers to dry out and in away from the steel. So steel next to foam and go with 3/4 foam layers.
The steel would be on the entire perimeter of the bedroom/bathroom.
OK, a double layer of 3/4" XPS or EPS would be somewhat of a vapor retarder, if not a vapor barrier. So the wall should ideally be able to dry from the foam both to the exterior and the interior. So the steel (a vapor barrier) needs to be next to the foam to avoid a double vapor barrier. Makes sense.
Apply plywood to the exterior of the studs. Then steel plate, taping the seams. Then 2 layers of foam, taping each layer. Then the second layer of 3/4" plywood, which would have to be fastened to the steel plate, or, through the steel plate to the 1st layer of plywood (or through the steel and 1st layer of plywood into the studs).
I might consider substituting a 3rd layer of plywood for the steel, applying a double layer to the exterior of the studs, taping the exterior of the second layer, then the double layer of foam with both layers taped, then the exterior layer of plywood.
Many thanks AJ.
Bill,
Q."Will the following wall section perform well as far as energy and moisture are concerned?"
A. Yes from a moisture standpoint. From an energy standpoint, the walls are so-so. Thicker rigid foam or a higher quality insulation between the studs would improve the thermal performance of the wall.
Q. "What type of foam would be best?"
A. Most green builders have concluded that polyiso is the most environmentally friendly type of rigid foam. For more information on this issue, see How to Install Rigid Foam Sheathing.
Q. "Since this wall section would have to have some drying capability to the exterior, what should I look for in a housewrap?"
A. As you have evidently already figured out, the wall needs to be able to dry out in both directions from the layer with the lowest vapor permeance -- in the case of your wall, from the steel layer. Almost all brands of housewrap are vapor-permeable, so I wouldn't worry. For more information on this issue, see All About Water-Resistive Barriers.
Q. "Would a vented roof system or sealed perform best?"
A. For a story-and-a-half (Cape Cod style) house, it makes sense for the insulation to follow the sloped roof assembly. If you take this advice, the rafter bays can be either vented or unvented, as long as your roof has no dormers, skylights, chimneys, valleys, or hips. If you have a complicated roof geometry with some of these listed features, you should create an unvented assembly.
For more information on these issues, see:
Two ways to insulate attic kneewalls
How to Build an Insulated Cathedral Ceiling.
Martin:
Many thanks.
I'll explore the costs of higher R value in the 5-1/2" stud depth.
Foil faced polyiso is what I used on the exterior of the walls on the original house.
I'll read up on water resistive barriers.
The roof is a simple 10/12 gable. There is a wood stove chimney near the ridge, and a level ceiling at 8'. So after re-reading the several articles on this site about cathedral ceilings, I was thinking I'd vent the roof with a 1-1/4" air space (1x furring and 1/4" plywood or OSB); insulate between the rafters with either fiberglass or closed cell foam; 3" foam under the rafters; air tight drywall with no recessed fixtures. Insulate the roof slope from the eves to just above the ceiling, insulate the ceiling flat to min. R 40, fabricate a well insulated, airtight scuttle, vents only at the eves and ridge, pay attention to air tightness where the chimney penetrates the 1st floor ceiling and the 2nd floor ceiling.
I think I can get the chimney penetration of the level 2nd floor ceiling flat more airtight than trying to get the penetration of the sloped roof air tight. Insulating the level ceiling also allows a more cost effective higher R value.
I have experience getting drywall airtight. A rental house that I built a couple years ago passed the Energy Star blower test even when a window was open 2". So I feel pretty confident I can get the GWB air barrier in the second story very tight.
Please let me know if I appear to have missed anything.
Thanks again.
Bill
After reading the article on water resistive barriers, I came away with a question.
Are you advising using a house wrap such as Home Slicker Plus Typar with vinyl siding?
There would be an airspace, but it would be continuous vertically only through the nailing slots. The vinyl would not absorb any moisture.
Would you think that the vinyl is loose enough not to require a wrinkled house wrap?
Thanks,
Bill
Bill,
Home Slicker Plus Typar is not necessary with vinyl siding. Vinyl siding is inherently well drained. All you need is ordinary housewrap or asphalt felt behind vinyl.