Wall questions

My new home was designed with 2×4 staggered stud walls on 2×8 top and bottom plates with 2.5″ closed celland 4.75″open cell foam.The engineer has specified areas in the main portion of the house (that has 17′ tall ceilings) to be balloon framed with 2×8’s and sheathed in plywood on both the interior and exterior. These are only 4′ wide sections at 4 corners, but would this combo cause any problems?
Also, the engineer was not familiar with staggered stud walls. Is there any study that looks at the strength of this kind of wall vs. a standard 2×8 wall?
GBA Detail Library
A collection of one thousand construction details organized by climate and house part
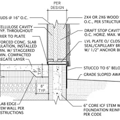
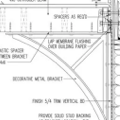
Replies
Kevin,
Where do you live? Advice is generally climate-specific.
Steve: Structural strength isn't a function of climate.
I'm surprised that an "engineer" can't actually figure this out, if not from tables, via math. But maybe it's been too long...
Kevin,
Q. "Would this combo cause any problems?"
A. I don't know what "combo" you are talking about. Are you talking about combining open-cell spray foam with closed-cell spray foam? Or are you talking about combining a wall framed with 2x8s with a wall framed by staggered double 2x4s?
Neither "combo" is a problem, as long as your engineer knows what he or she is doing.
Dana,
I was curious about all the spray foam in the wall assembly, but I probably should have said as much in my post.
2.5" of closed cell foam (R15-ish) is sufficient dew point control for 4.75" of open cell foam in any climate (maybe not at altitude in Antarctica though. :-) )
Whether or not the 2.5" is necessary or rational depends on your actual climate, and whether or not the engineer is specifying that much closed cell in order for it be structural.
I should have given more details. Zone 4 mountains of NC. The combo I was curious about was making a plywood sandwich filled with foam. Doesn't seem like the most "breathable" combo.
I would prefer staggered studs for the walls, but he didn't seem to get the idea. He was worried about 2x4's that were 32" o.c. I have to explain the details to him.
Kevin,
A wall doesn't need to breathe. A wall doesn't even need to be vapor-permeable.
The plywood on the interior of the proposed wall should be able to dry to the interior. The plywood on the exterior of the proposed wall should be able to dry to the exterior (assuming that no errors are made with the WRB or siding installation).
You still have 2x4s 16" on center with plywood on both sides, but the plywood is only attached every 32", which means installing the plywood with the 8' side running horizontal to not have weak seams in the middle somewhere. The fact that it's not attached 16" o.c. mean that there IS a shear strength issue to be sorted out/calculated by the engineer.
If the engineer isn't up to the task, installing let-in bracing for shear strength on the exterior studs is probably a more familiar problem, and far cheaper than 2.5" of closed cell foam for additional structural rigidity.
A 32" o.c. stud wall doen't make for very flat surfaces, even when clad with plywood. Ordering some finger-jointed 2x3s instead of milled 2x4s for the interior course of studs will have fewer aesthetic issues, and lower thermal bridging. Unlike milled lumber, finger jointed studs are very straight with no twist or bowing, and are more dimensionally stable. They come in different grades, and can be used as structural wall framing (with the right grade.) Finger jointed 2x4s would work too.
Dana,
I think Kevin is suggesting 16" oc studs on each face of the staggered stud wall. The 32" came from a misunderstanding by his engineer.
Malcolm: I think we need a picture, perhaps with a few dimensions (or at least I do...)
Two sets of 2x4 16"o.c. staggered onto 2x8 plates, each sheathed with plywood is pretty massively structural, and wouldn't be of any concern.
Kevin,
I imagine you have read Martin's article on "How to Design a Wall." (But if not go to https://www.greenbuildingadvisor.com/articles/dept/musings/how-design-wall). If budget is a concern (as it is for most of us), you could build a simpler, thinner wall that would perform well in your climate. Is there are particular reason you are going with this design?
To make what I think Steve Knapp is hinting at super explicit:
Instead of a 7 1/4" 2x8 sill with staggered studs and closed and open-cell foam, have you considered:
2x6 Stud wall with cavity insulation (R-20ish) + 1.5" of exterior rigid insulation (R6 to R8-ish, depending on the type of rigid). That's about the same total thickness, and is a more "conventional" wall assembly.
The 2x6 with rigid has about R-26 to R-28 worth of insulation. The staggered stud design looks like it has R-32 to R-35 of insulation. The staggered stud wall does have more insulation in it, but the standard 2x6 with exterior rigid might simplify things enough to make it worth it.
And if you want more insulation in the 2x6 wall, all you have to is increase the thickness of the exterior rigid insulation.
Food for thought.
Dana--Malcolm is correct. 2x4's 16o.c. on each side. The engineer thought 32" between studs on each side. I attached a pic of the back of the house. The main area that is vaulted is where the engineer is concerned about racking. So if you look on either side of those large windows, he specified 2x8 balloon framing, 12" oc, with the plywood on the exterior and interior. He repeated this at the opposite corners as well. For the rest of the vaulted area, he specifies 2x8 framing but without the need for interior sheathing. The rest of the house is framed with the staggered studs. I was just wondering if there was some weakness in the staggered stud approach, but the weakness my simply be in communicating to the engineer what we are doing. He also specifies 6 2x8 king studs on either side of those large windows---there goes any thought of thermal breaks!
Steve/Brendan--I discussed the exterior foam with the builder and they had not done it. I don't want to be the guinea pig for the builder/framer/siding folks. They had done staggered stud walls, so in the interest of getting a good job done, I went that route.
You have problems with the wall aspect ratio. It is a structural issue. In the SDPWS 2015 edition this referenced standard on page 28 limits the shearwall aspect ratio to 3.5:1 your wall exceeds this. 17'/4'=4.25 to meet this the wall needs to be 59.5 " wide, not 48. You can view the SPDWS here for free http://www.awc.org/codes-standards/publications/sdpws-2015
You need to look for a preengineered wall solution, be it from Simpson or Hardy Frame. They can provide a wall engineered, designed & tested to meet the load & deflection criteria. They are typically 3.5" deep or 5.5" deep. so that would leave room to frame the wall to the 8x dim & get the proper insulation.
Kevin,
I get that you want to pick an approach that won’t further complicate the build. (Been there. Done that.) if it were my house, I would price out blown in cellulose. A lot greener and probably cheaper than all that foam.
Steve--Open cell foam was actually cheaper than cellulose. Either way I was going to do some closed cell against the sheathing to avoid the thick wall condensation issues that Martin has tackled in his writings. I did not want a risky wall.
TimR--Thanks for the link. Interesting reading! I wonder if the structure of the wall essentially breaks it into two sections, one for the lower large windows and one for the clerestory windows up above. There is a massive header above the lower set of windows, then several feet of framing before the clerestory windows, which also have their own substantial header. If that is the case, then the aspect ratio would be much different. I'll have to speak with the engineer.