Wall Moisture without Vapor Retarder In Cold Climates

Its well known that improper use of vapor retarders can prevent walls from drying out properly and leading to moisture related issues such as mold and rot. Is it uncommon to have moisture issues in wall due to air leaks or vapor diffusion if the vapor retarder is left out? Would there be a concern with moisture issues for a standard construction wall (siding, plywood sheathing, 2×4 or 2×6 frame, fiberglass or cellulose insulation, drywall without vapor retarding paint) if the vapor barrier is not used in cold climates? Would this meet code in the Chicago area?
Thanks,
Ed
GBA Detail Library
A collection of one thousand construction details organized by climate and house part
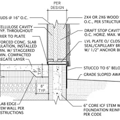
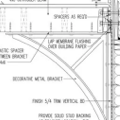
Replies
Yes, the walls would experience problems. You need to go back to why vapour barriers were introduced into exterior walls in the first place. Indoor moisture making its way into wall cavities really wasn't much of a problem until the 1970s when the push to conserve energy lead to widespread use of (mainly) batt insulation. In canada this was pushed by the CMHC, and it was the widespread wall failures of the houses they had sponsored that was largely responsible for that adoption of poly vbs as a way of mitigating air movement into the exterior walls. Recently other strategies have come into favour, such as air-tigjht drywall, or the use of exterior sheathing, but i don't think anyone is advocating building without some method of limiting the movement of air through exterior walls.
Edit: The problems you refer to being caused by vapour retarders occur when they are placed so that the wall does not have a path to dry to. The reason the wall would have moisture to dry in the first place would in most cases be that there was not an effective vapour retarder.
Ed,
Malcolm's answer is somewhat unclear -- I think he is confusing the need for an interior air barrier with the need for an interior vapor retarder.
If you pay attention to air tightness (by following the Airtight Drywall Approach), there is every reason to believe that your wall would function very well in Chicago, even without vapor retarder paint. However, your local building code probably requires the use of a vapor retarder on the interior side of your wall -- so you should probably go ahead and install kraft facing (the kind that accompanies fiberglass batts) or vapor retarder paint (if you choose celluose -- the better choice), just to keep the building inspector happy.
Martin, while there are important distinctions between air barriers and vapour retarders I took Ed's use of the term to be generic of all approaches that limit the permeability of a wall - whether it be through the materials or around them.. I may have misunderstood, but I took him to be asking whether the risks of trapping water in the wall cavity by using any material that limits the ability to dry outweighed the benefits and whether it might be better just to have a permeable wall. I think we would agree that it isn't a good idea.
Thanks very much for the replies.
Martin - How much concern would you have if the house was not airtight?
I realize my original post was not very clear. The builder for a house in Chicago is building the walls in the this manner from outside to in: siding, Tyvek, plywood or OSB sheathing, 2x6 wall with spray cellulose, and drywall. He doesn't use a vapor barrier to allow for drying, he doesn't take any extra steps to make the house airtight. It seems like every story I hear about wall moisture problems is because of improper use of vapor barriers, not because it was left out. Is there concern that leaving out the vapor barrier without making the house reasonably airtight lead to a moisture problem?
Ed,
You're writing for advice, so here's some advice: make sure that you choose a builder who understands how to frame a wall with airtightness in mind. It's probably a good idea if your drywall contractor also understands airtight construction.
There's no reason to build a brand-new house with contractors who don't understand these principles. "How risky is this?" is the wrong question. The right question is, "Why would I want to choose contractors who don't know how to do a good job?"
"It seems like every story I hear about wall moisture problems is because of improper use of vapor barriers, not because it was left out."
Ed, those stories largely concern highly energy efficient houses where something has gone wrong. Such houses often feature innovative envelope design and are like pure-bred racehorses in that they either perform very well or suffer catastrophic failures.
The standard construction as practiced for several decades of carefully air-sealing and using either the drywall or a poly VB to stop the migration of moisture into the wall cavity has not been associated with wall failures. The absence of air-sealing insulated walls has seen envelope problems that dwarf any of ones you site both in their number and severity.
This thread has gone asunder.
Ed, if your builder builds good homes, and you want to hire him, then you are done. You won't teach any builder how to build whatever we post.
Martin,
Thanks for your advice, I agree 100%. Unfortunately it doesn't appear very common for builders to use the the airtight drywall approach (or other methods to make the house airtight) in this climate zone. The status quo appears to add a housewrap and call it good.
I'm not the person building, just the person trying to help out by presenting the facts to someone who is. There is the obvious concern with energy loss but would you be concerned about potential moisture issues with the wall construction I previously mentioned? Are you aware of similar wall constructions that have had moisture issues? I realize this may not be an easy question to answer. I did find some info on the buildingscience.com website for the standard construction wall in Minneapolis.
"The analysis of the air leakage condensation potential from a poorly detailed air barrier results in approximately 4500 hours of potential condensation", page 30, http://www.buildingscience.com/documents/reports/rr-0903-building-america-special-research-project-high-r-walls
It didn't state explicitly whether this was a concern, it did give the wall a durability rating a 3 out of 5.
Thanks everyone for your comments.
Ed
Re: "... poly VB to stop the migration of moisture into the wall cavity has not been associated with wall failures." That depends. Check here: https://www.greenbuildingadvisor.com/blogs/dept/musings/when-sunshine-drives-moisture-walls
Ed,
I don't think that the wall system is particularly risky. However, I still urge you (or the builder or owner of the project in question) to pay attention to airtightness.
If the exterior siding has a vented air-space aka "rainscreen" (even 1/4") between the sheathing and the siding it would have excellent drying capacity toward the exterior and would meet IRC code for zone 5.
Vinyl siding is inherently back-vented (not that I'm a big fan of vinyl), and would need no special accommodation for making rainscreen gaps. There are commercial mesh underlay products for providing 6mm(1/4") or 3.8" (10mm) the spacing which work, but using 1x furring at each stud on which to hang the siding is another common method.
Cellulose is inherently more air-retardent than batts, and reduces air-transported moisture even if the interior isn't super-tight. Using dense-packed cellulose @ 3.5-4lbs/cubic-foot density takes that down another order of magnitude, and with even 1/4" mesh underlayment on the siding the wall assembly is super-protected. Cellulose has the capacity to safely take on quite a bit of wintertime moisture from vapor-diffusion or minor air leakage without losing effectiveness, protecting the structural wood in the process.
The primary cause of moisture/mold/rot problems in walls is still bulk-leakage from improperly flashed windows & doors, followed by air-leakage, with vapor diffusion at an extremely distant third place, as much attention as vapor-retarders get in code. If an assembly can be designed to work without poly vapor barriers, it SHOULD be built without them, IMHO, since A: In practice the poly rarely air-tight, and B. Poly severely inhibits drying, whether air-tight or not.
John, Wrong side or improperly installed vapour barriers can cause all sorts of problems, but to attribute the wall failure the article details to the presence of a VB is to only look at one part of what went wrong.
I'm not advocating for their use, but at present, outside the rarified world of green building and it's one-off projects, sealed poly represents a viable method of stopping air movement that doesn't interfere with common building practices as they are done throughout most of this continent.
Unlike air-tight drywall, applying and sealing poly is a separate stage which can be inspected and tested. The drywall that follows, which may include it's own separate acoustical and fire code demands, doesn't compromise the air-sealing, Having worked on many large multi-unit residential projects I don't se how you could currently adopt an air-tight drywall approach without re-organizing both the sequencing and skill sets of the sub-trades.
As Dana points out, the second most common source of damaging moisture in walls come from inside air making its way into the cavities. Because some projects used materials where their impermiability caused problems isn't any reason to give up on air sealing.
Malcolm's advice is appropriate for many locations in Canada, but is not recommended in the U.S., especially for buildings that will be air conditioned. Leave out the polyethylene unless you have a maple leaf on your flag.
True Martin - however the topic is "Wall Moisture Without Vapour Barrier in Cold Climates".
...but the location in question is Chicago, not Winnipeg, and the presumption is that Ed is looking for advice relevant to HIM, not a generic answer broad enough to cover any arbitrary cold climate. ( In Antarctica you should skip the poly and use foil instead, but I doubt Ed really cares- I know I don't. :-) )
In most of the lower-48 of the US the rampant mis-application of poly in locations where it can just as easily be designed-out has caused as many real-world problems as it was intended to solve, and that would include Chicago. Summertime dew points in Chicago are high enough that a drying-toward the exterior only approach can create mold problems in an air conditioned houses with interior poly and fiber insulation, with or without air-tight sheathing (or air-tight wallboard), especially those with stucco or brick cladding. (Brick cladding & interior poly can be an issue for air conditioned buildings in Winnepeg too.)
Dana You may be right. I don't know enough about warmer climates and defer to your experience. I am still a bit sceptical about the real damage done to houses in northern climates during the brief summer period during which they are air-conditioned. Have you heard of any actual examples that were built with standard construction materials? All the reports I've seen, like the example John linked to, also had unusual elements such as very permeable sheathing, which makes me wonder how significant the presence of the vapour barrier really was.
Again, I'm not convinced that vapour barriers are necessarily a good idea. It's just that right now alternate means of air-sealing require a skill set not readily available in the building trades. No doubt in the future that will change.