Wall insulation for a new room addition

I’m thinking about this (not so) future project. One option is 2×6 studding with R-19 (6″) fiberglass batts in between studs. To gain more R value and reduce thermal bridging I was thinking of adding probably 2″ of type II EPS (4.2 R per inch they say)to the inside of the studs, for about R-27 for the wall. I’m assuming this needs to dry to interior since plywood and/or OSB are pretty impermeable to moisture and would limit drying to the outside. Is that correct, and if so is 2″ of EPS adequately permeable for interior drying? I would have sheetrock over EPS.
Or, I could do same R-19 batts in between studs, and then 3″ of EPS on exterior (R 11.25 needed in this arrangement, for a total of about R-31). With taped sheetrock on the inside this would certainly be able to dry to the interior.
Is one of these better than the other? I will likely be using vinyl siding, and one issue is the poor compatibility of vinyl siding with exterior foam. The other is the challenge of the added thickness of the wall (this is also true with interior foam, but seems less of a challenge than the exterior thickness).
Advice and input would be much appreciated.
GBA Detail Library
A collection of one thousand construction details organized by climate and house part
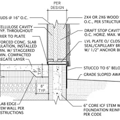
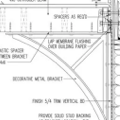
Replies
Howard,
Of the two approaches you mention, exterior rigid foam is by far the better approach, because exterior foam addresses rim joists and partition intersections better than interior foam. Moreover, the exterior side of the wall has fewer electrical boxes, making exterior rigid foam more effective at reducing air leakage than interior rigid foam.
Finally, exterior rigid foam keeps the sheathing warm and dry. Interior rigid foam doesn't.
For more information, see these two articles:
How to Install Rigid Foam Sheathing
Walls With Interior Rigid Foam
By the way, you didn't mention your geographical location or climate zone. We can provide better advice if you tell us where you live.
If you decide to install interior rigid foam, there isn't any need to worry about the vapor permeance of the rigid foam, especially if you live in a cold climate. Most walls with interior rigid foam can easily dry to the exterior.
Thanks Martin. I'm in zone 6, northern Vermont. I see the advantages of exterior rigid foam. But, the 3" of thickness I would need make installing vinyl siding very problematic. I'd forgotten I needed 3" of exterior as opposed to 2", and this makes for a critical difference. Also, I just realized I'm likely using a slab floor and would have no equivalent of rim joists. If I do a cathedral ceiling with raised heel trusses, as I'm thinking, I also have no equivalent of rim joists at ceiling level either, sort of neutralizing that advantage of exterior rigid foam.
Howard, have you considered using polyiso on the exterior instead of EPS? A layer 2" thick would just meet prescriptive code for condensation control. Due to polyiso's reduced performance in cold weather it would drop below the safe threshold during the coldest weather, but if you use a good variable-permeance membrane on the interior and have low rates of air leakage it shouldn't be a problem. Zip-R12 would provide shear strength, insulation, an air barrier and a nailing surface all in one shot. It requires a gun that will shoot 4" nails, but other than that it's pretty standard construction.
Another option to consider is framing with 2x8s. You don't get a continuous thermal break, but the entire wall performs well at somewhere in the mid-R-20's.
Michael: I've generally thought to avoid exterior polyiso because of the cold weather hit, and this is a very cold climate, but I get your drift and will bring it back into the mix. I'm not sure I get the advantage of 2x8 construction. Are you talking about my getting more thickness of fiberglass there? Like using a 10" batt and condensing a bit?
Howard, to be clear, 2x8 framing would not be my first choice, but in terms of whole-wall R-value (or U-factor) it will perform similarly to slightly thinner assemblies with continuous insulation. A 2x8 is about R-9, and fibrous cavity insulation can be anywhere from R-24 (8" fiberglass batts) to R-30 (mineral wool). R-30 fiberglass batts compressed into a 7 1/4" cavity will perform at R-25, not a big gain for the cost, but it may be worth it. You might be able to cram R-38 batts into a 7 1/4" cavity, for R-30 performance, but it would be a very tight fit.
Depending on your framing fraction (the ratio of framing to cavity) and choice of insulation, a 2x8 wall will perform roughly the same as a 2x6 wall with 1" of exterior foam (which is not enough foam in your case, but that's the thermal comparison). But if getting the first costs down, and/or labor skilled in exterior insulation is short, 2x8 framing provides decent performance using traditional techniques.
Another technique is called the Bonfiglioli approach, applying foam to the interior of the studs only. My math says it doesn't make sense in most cases but others think it's great.
A wall that is seldom mentioned is a 2" x 8" double stud wall. I have used this for new home construction and it is easy to build. Staggered 2" x 4" studs, 16" on center with common plates. 2 layers of R-15 insulation and 3/4" fiberboard sheathing will put the overall wall assembly close to R-30. House wrap and a rain screen underneath the siding will allow the wall to dry to both sides with MemBrain or the like as the interior air barrier.
Thanks Michael for your clarification on the 2x8 wall; I now see your point. Since Martin wrote I didn't need to worry about drying w/interior rigid foam if I went that route w/2x6 studs, I'm thinking 2" of EPS or polyiso would do more to limit thermal bridging and also give me more additional R value. With polyiso on the interior I wouldn't have to worry about the cold R hit. I may consider rock wool in between the studs if the addl cost is not too prohibitive. I like that rodents are disinterested, among other things.
I AM considering 2" of exterior polyiso based on your feeling that would work fine. I can do 2" exterior but not 3" (sort of a long story).
Doug - thanks for the suggestion. It seems I get about R-30 out of the above scenario too.
Am I correct that plywood is more permeable than OSB and might be the better sheathing choice with this arrangement I'm considering? (I know it is somewhat more expensive. Is the perm difference negligible?).
Doug, there is nothing wrong with a wall design like yours, but also not much of a thermal advantage over continuous 2x8 studs, as there is about the same total insulating value in the wall assembly either way. Offsetting the studs will reduce potential cold spots on the interior of the drywall, will improve sound resistance, and may cost less for materials, but labor will be easier with a single 2x8 stud.
Howard, most EPS is rated for roughly R-4/in, so 2" won't provide the condensation resistance you need. Unfaced EPS is somewhat vapor permeable, but not enough to make for a safe assembly (or to meet building codes) in 2" thickness in zone 6. (Even if you're not required to follow the IRC, it's a good reference for reasonably safe assemblies.) If you changed to 2x4 framing and used at least R-10 sheathing (2 1/2" EPS) you would have a safe assembly that meets the building code.
When walls can dry to the exterior, the sheathing perm rating does matter to some degree, and CDX is more vapor-open than OSB when it's wet. But if your exterior foam is thick enough in comparison to the interior insulation, the sheathing should not get wet, and it won't matter.
It looks like none of us recommended this piece of essential reading for you: https://www.greenbuildingadvisor.com/blogs/dept/musings/calculating-minimum-thickness-rigid-foam-sheathing. Maybe it will clear up some of the confusing points.
Michael,
I agree that there is not much of calculated thermal advantage to the double stud 2 x 8 wall. Framing with all 2 x 8 lumber is expensive and typically 2 layers of 3.5" insulation will be less expensive than an 7" batt. The cost savings on material should offset the additional labor for the double stud wall. What I have described is a very cost effective and high performance wall that dries to both sides using common and cost effective materials. There is no splitting of insulation batts for electrical wires as they can run between the studs.
Michael; I likely wasn't clear in my post. I am aware that 2" of EPS exterior is short of the needed R value, and I know that is a no go. My question was about 2" of polyiso on the exterior, with higher R value, and which you felt would work. I was considering 2" of EPS on the interior, but it seems polyiso would work better here for the added R value. I was mostly concerned that polyiso would not have enough permeance, while EPS might, but this is where Martin said not to worry. So, I am thinking 2" of polyiso on the exterior with either fiberglass of roxul between 2x6 studs.
Howard,
If you end up using 2 inches polyiso, which (when de-rated for cold weather) doesn't quite meet the R-11.25 goal you're aiming for, make sure to include the smart vapor barrier on the interior recommended by Michael Maines.
Martin: I will remember the smart vapor barrier; very good insurance. I also plan on doing other small things like going around with the fine tooth comb of my foam gun and filling any voids, beading the seam at the stud/sheathing interface on the interior, etc.
My somewhat educated guess is that any amount (say 1" to 3") of exterior unfaced EPS will improve moisture performance in a cold climate. Build a wall that is OK with no exterior foam and adding exterior unfaced EPS will make it better.
This can be an important point because of the step increase in external foam cost when it exceeds 1.5".
Note that the R value of external foam to use a Class III retarder only reduces (not prevents) condensation and is apparently specified assuming no outward drying. EPS allows some outward drying and so it's logical that somewhat less R value would provide the same moisture performance as foil faced rigid foam at a somewhat higher R value.
More specifically, given these options with a 2x6 wall in a cold climate:
a) R8 of exterior unfaced EPS
b) R11.5 of exterior foil faced polyiso
c) interior foam of similar R value.
For moisture performance, I'd take a). All are IRC compliant.
Jon R,
Builders who are tempted to ignore the rules for minimum foam thickness make me nervous. As I wrote in a recent article, "Rethinking the Rules on Minimum Foam Thickness," there aren't any reports of widespread failures in homes where builders have installed exterior rigid foam that is too thin.
Nevertheless, I still advise builders to follow the rules on minimum foam thickness for new construction -- since deviating from the rules raises the risk level, especially if a future owner operates the house at a high indoor humidity level.
One inch of unfaced EPS has a permeance of 2.0 to 5.8 perms. Two inches of unfaced EPS is obviously less permeable -- in the range of 1.0 to 3 perms. Outward drying through 2 inches of EPS would be slow.
> since deviating from the rules raises the risk level
Does it always? I'd like to see the data showing that option a) in my example isn't the lowest risk (at any interior humidity).
With Lstiburek's varied advice, I'd call them "Holladay's rules". In no case should the IRC 1405.3.2 be used as support for "these designs perform better".
Even so, I agree that there is a lot to be said for sticking with simple rules. And Holladay's rules produce a good wall.
> Outward drying through 2 inches of EPS would be slow
But far faster than through foil faced polyiso. And drying to the interior can still occur (especially with smart retarders). So it comes down to a trade off between drying in two directions vs more condensing hours. Where exactly these balance out is an open question.
"So it comes down to a trade off between drying in two directions vs more condensing hours. Where exactly these balance out is an open question."
It's not a truly an open question, since fairly accurate answers can be gotten from a WUFI analysis (if all of the right parameters are entered.).
But it's complicated, not simple enough that can be condensed into an easy to follow prescriptive table broken down by climate zone that can be adopted by the IRC, such as Table R702.7.1 (IBC Table 1405.3.2 ). People have a hard enough time figuring out how to use Table R702.7.1 correctly.
My personal view is that any stackup that requires a seasonal moisture accumulation to dry by passing the moisture through a layer of OSB or CDX isn't sufficiently conservative design in zone 6, whether the drying side had 2 perm EPS or 20 perm rock wool, even if it (sometimes) can work.