Wall construction – exterior vs interior-facing foam/sheathing?

Long time reader, first time writer…
I’m in climate zone 4 on the east coast (right on the edge of 5) and am renovating an older house with 2×4 construction. My plan is to remove the existing sheathing and windows, add 2″ of foam (outside of the framing), and install new windows (as if the walls were 2×6 construction).
Based on my limited understanding, and on what I’ve seen here, the “standard” approach for this would be (in short):
(1)Put new sheathing right on the framing, then WRB, then 2″ foam board, with bucks to bump out the windows so they are flush with the outside of the foam. Then siding/rainscreen, probably (clap or something) attached to vertical-running spacer strips (to get an airspace behind it).
However, given the existence of insulated ZIP products, and some others (i.e, “insulated nailbase” panels), it seems that another alternative would be (again roughly):
(2) Screw insulated sheathing directly into framing with 2″ of foam facing inward and ply/osb facing out (using the specified fasteners). Probably also use bucks to bump out windows so flush with the osb/ply. Then WRB over everything, then siding. In this case, you end up with a continuous nailing surface on which to potentially install shingles (over, say obdyke slicker or something along those lines).
It seems that the latter option might save a bit of time from the perspective of being a single install layer (instead of sheathing and foam separately). On other hand, this might be offset by greater cost of materials.
However, regardless of cost considerations, is one approach (specifically, having the foam layer inside or outside of the sheathing & WRB) notably riskier/or superior to the other, from a strictly functional (i.e., vapor drive, condensation) perspective? Forgive me if I sound like an idiot…
Many thanks,
C
GBA Detail Library
A collection of one thousand construction details organized by climate and house part
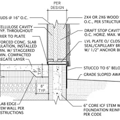
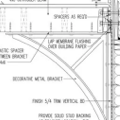
Replies
Why are you removing the existing sheathing? (Seems like an unnecessary expense.)
Structural issues become problematic when there is a foam layer between the sheathing/nailer and the framing, especially with thicker foam.
It doesn't take much foam in an zone 5 location to have adequate dew point control on structural sheathing attached directly to the studs. The IRC calls out R5 (3/4" of foil faced polyiso would do it).
If the goal is to make it the exact wall thickness of a 2x6 wall, using 1.5" foam (R9, if polyiso) with a half inch asphalted fiberboard nailer (R1.3) through screwed to the studs with cap screws would pretty much double performance of a 2x4/R13 type wall, and would have twice the exterior-R called out by the IRC for dew point control. Asphalted fiberboard is extremely moisture tolerant, and would have no issues with cedar shingles + Rainslicker or Max on the exterior sans-WRB, if mounting the windows "outie on properly flashed window bucks.
A WRB between the foam and structural sheathing would only be needed if going with an "innie" window mount. See:
https://www.greenbuildingadvisor.com/article/where-does-the-housewrap-go
Check with the shingle company to see if the size & type shingle you are considering can be nailed to half-inch fiberboard, or whether it needs to be OSB or plywood. If the nailer needs to be OSB/CDX a WRB would be required even for outie windows, and the R-value of that layer would only be R0.6 - R0.75 (not that it would matter from a dew point control perspective.)
Be sure to detail the existing structural sheathing as your primary air barrier before adding layers. The seams can be taped with a suitable tape before adding the foam, but also use polyurethane caulk or purpose-made sealants the full perimeter of each stud bay, and on every double-up framing seam (top plates, jack studs, etc) and where the bottom plate meets the subfloor before insulating and finishing the interior.
Thanks so much for your input Dana,
Good question re: replacing the existing sheathing; it appears that the sheathing is also the siding, if you know what I mean. It looks like T-111 kind of stuff... and it is showing signs of rot in a few areas. With that said, I suppose that for the most part it is structurally-sound, so I could theoretically leave it on there and put foam + WRB over it (after taping seams, etc). Part of me was also thinking that pulling it off would allow me to replace the existing fiberglass batts with Rockwool for some extra R-value, noise reduction, and peace of mind...
I'm not stuck on making it a 2x6 wall (provided I can get the windows made to the correct wall thickness). Maybe my most cost effective option would be to leave the T-111 on there (replacing the rotten bits), and then putting 3/4" polyiso on top of it with WRB over that. I think I'd go the "outie" window route (i.e., the nailing flange effectively flush with the outside of the foam)...
Definitely will pay attention to air-sealing as you suggest prior to foam/WRB install.
Many thanks again,
c