Wall assembly review?

Hello, again, GBAers.
I’m in the planning stages of a ~1850 sq. ft. PassivHaus-compliant home in Salt Lake City (5B) [1]. After reading Martin Holladay’s post on the Belgian PassivHaus home rendered uninhabitable [2], I am hoping to get some feedback on my wall assembly design [3].
Cheers,
Jan
[1] http://1010-design.blogspot.com/2012/02/more-detail.html
[2] https://www.greenbuildingadvisor.com/blogs/dept/musings/belgian-passivhaus-rendered-uninhabitable-bad-indoor-air
[3] http://1010-design.blogspot.com/2012/06/wall-assembly.html
GBA Detail Library
A collection of one thousand construction details organized by climate and house part
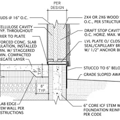
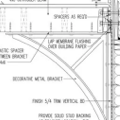
Replies
Jan,
I don't see any information on your siding. One of the reasons that the Belgian house got into trouble was because of the brick veneer -- so siding can made a big difference.
Jan,
At a cursory glance, given the compactness of the project, project's orientation and abundance of insolation in SLC, utilization of Zola's windows (which we really like and have been pushing to use) - I actually think your R-values may be overkill... Especially the R-119 roof. We've noticed a point of diminishing returns where because the add'l insulation adds to the surface area, in some climates (especially places like SLC, Denver) if we back out the roof insulation to something more nominal, the compactness ends up going down and results in the space heating demand improving. Less cost, better performance.
Also, I don't think there's anything wrong with the TJI wall - Chris Corson loves it, Carly Coulson uses it as well. We're finding it's overkill for our projects here in Seattle and when we move our projects to SLC, even more so. Corson had a bunch of his details in a recent JLC article, and if you send him an email I'm sure he'd be willing to talk about the merits/details of his assembly. The issues w/ the Belgian PH (if we can call it that, it busted the blower door test) seem to be a mix of poor construction quality and bad design. I don't think your wall is headed in that direction.
Jan,
I saw in your drawings that the OSB was to be "caulked at all joints".
We just had an exchange on our Passive House Northwest google groups re: Prohibition of glueing the OSB to the frame. It was posted by structural engineer Carissa Farkas who has been the structural consultant on many many PH projects regionally. To quote:
"Per the ANSI/AF&PA, Special Design Provisions for Wind and Seismic, 4.3.6.3.1:
"Adhesives: Adhesive attachment of shear wall sheathing shall not be used alone, OR IN COMBINATION with mechanical fasteners". (my emphasis in caps)
The commentary states:
"Adhesive attachment of shearwall sheathing is generally prohibited unless approved by the authority having jurisdiction. Because of limited ductility and brittle failure modes of rigid adhesive shear wall systems, such systems are limited to seismic design categories A, B, and C..... Tabulated design values... are based on assumed nail slip behavior..."
So consult your structural engineer and if it is not allowed, please make a note on the drawings prohibiting it to avoid it's potential use. There are other methods of creating a tight air barrier."
Consider the OSB gaps. OSB expansion is noted by most manufacturers and the gaps are called out. Also consider and note and joint sealing material if used. I suggest not using an adhesive caulking, but use tape or Tremco Acoustical sealant.
Run a WUFI based on the projects climate and envelope layers.
Hi Martin @1: the cladding isn't finalized, but I'm leaning toward stucco or fiber cement for the cost, durability, and clean simple look [1]. Advice welcomed.
[1] http://www.recampus.com/documents/book05_c01.pdf
Hi Mike @ 2: Thank you for the quick review and feedback. I'm not sure I understand everything you're telling me, so I'd like to ask you a couple of clarifying/pedantic questions. When you say "compactness [goes] down...results in the space heating demand improving" are you referring to the cost of the additional insulation at construction versus the reduction in the on-going heating demand, i.e., the return on investment of the additional insulation will not be recouped (regardless of whether the return is based on my ownership, my lifetime, or the home's lifetime) - is that right? If not, can you help me understand?
When you say "[TJI is] overkill for our projects" is that also a construction cost issue, i.e., you can achieve the objective in a less expensive wall assembly design? If so, would you be willing to share what kind of R-50+ wall assembly is more cost effective for you? Presumably, labor is lower for TJI but higher cost of materials resulting in a net higher cost - is that right?
I'll chase down details on your Chris Corson [1] and Carly Coulson references - thanks, again, for your insights!
[1] http://www.jlconline.com/cgi-local/viewnew.pdf/0/2ec24b200e71616e7e0f73693d8940a9/www.jlconline.com/cgi-bin/jlconline.storefront/4fcea5ed0ee16ec927170a323cb406f9
Jan,
When I say compactness, a better way to think about it is in terms of surface area/volume, or surface area/treated floor area. The more compact your building is, the less heat loss, comparatively (Hayden Robinson had a good blog post on this: http://prospectstreetpassivehouse.com/2011/06/05/compact-building-forms/)
With as thick as your roof insulation is, there may be a point (which we’re finding on our projects) that the specific space heating demand goes down if we reduce the amount of roof insulation (due to the corresponding surface area reduction). Especially if the rest is optimized fairly well. Conversely, due to diminishing returns, adding insulation doesn’t really get us much in terms of ‘savings’ on the specific space heating demand, plus we have to add in the 'hit' from increased surface area. All of this is going off the assumption that you’re not calculating out your negative psi values at building intersections (though I recommend it, it’s a free bonus and can save costs elsewhere).
Being connected to the design community and trying to balance perceptions of Passivhaus/bring along our high design brethren, I'm hypersensitive to perceptions around overinsulation. I know a lot of architects who want a thinner roof plane, not a thicker one, so telling them it needs to be 3x thicker than code because I’m not optimizing their plan will not win the hearts and minds. Furthermore, a house in a mild climate incorporating an R-100 roof when it isn't needed becomes an easy underbelly. It's sort of like the bike rack issue for LEED.
For us, the TJIs are overkill because we're opting for decent windows (Zola is great, our project just placed order with Intus) and balanced the fenestration for maximizing solar gain while maintaining light/views/etc. So for our project(s), R-50 is too much by a large factor. Given our lots are not large, that means we’re putting money into the envelope, instead of into the living area. If we’re working on a house that can have a max footprint of 25’x40’, and have designed in 17” exterior walls (rainscreen, 9.5” TJI, 2x6 structural wall) – that leaves us with 824sf/floor of actually livable space. If we can get away with an 13” (total depth) double stud wall that is cost neutral to the TJI, our livable area is 867sf/floor. That’s a net increase of 86sf over 2 floors. Median sales price is $283/sf here, that adds $24,338 to the value of the house. When working with developers (which we’re doing) that makes a huge difference (e.g. we just covered the increase in their window costs).
On the project we're about to submit, our numbers are slab R-38/wall R-45/roof R-58 with a high envelope:TFA ratio at 3.7. We're not designing this one, so it's not as optimized in terms of fenestration and massing as we'd make it - but it's not bad. Our anticipated space heating demand is 4.44kBTU/ft2a. When we move it to SLC, our space heating demand drops down to 3.5kBTU/ft2a once we adjust for the overheating due to the increased insolation. This means if we were shooting for certification there with our project as it’s designed, we could do several things, including the following:
Leave it and just have lower annual heating bills
back out some of the insulation (potentially saving cost)
add more glass to the north
Basically, what this says to me is that your climate should be easier than ours given the right orientation (which your project has), even though SLC has 25% higher HDDs than SEA.
Jan,
If you are cladding your house with stucco, you definitely don't want to use vapor-permeable sheathing, in my opinion. If you choose fiber-cement siding, you'll probably be OK with your chosen sheathing.