Wall assembly remediation with only exterior access (~1940/50’s home renovation) Climate zone 6A

As far of a larger renovation, I am re-siding and replacing all windows in an older home. The more demo I do, the more I am sure I need to address wall assembly issues in a wholesale manner. There is significant framing rot in existing RO’s and moisture damage throughout. The existing wall assembly (from ext to int) is clapboard siding>tar paper> gapped horizontal sheathing boards>wall cavity with old indeterminate cellulose-type insulation sandwiched in between two layers of black, kraft-like paper>horizontal strapping>hardwood floor underlay>vertical t&g boards. In other areas of the house there is original plaster instead of strapping and t&g.
The windows weren’t flashed at all, so the rot makes sense there. But enough moisture has found its way into the wall that the sandwiched cellulose sits in a sodden heap at the bottom of its paper casing, so it’s practically an uninsulated wall (some areas are worse than others).
I need to find an elegant solution to address water/air/vapor concerns while re-insulating, but the trick is I can only work from the outside. The client wants to save all interior finishes if possible. My primary concern is how leaky this assembly is. The laps in the floor underlay are hardly airtight, let alone the original outlets and t&g boards.
My best thought currently is to use some variety of rigid foam, cut and placed into the interior side of the stud bays, and spray foam seal the perimeter as well as receptacle boxes and other obvious holes.
My current proposed assembly (this time from int to ext) is t&g boards (or plaster)>strapping>spray foam sealed rigid foam>bulk insulation>sheathing>WRB> siding.
The type of rigid foam (thickness and perm) is a question mark for me now, as is style of WRB (Zip or Ply/Tyvek). In terms of ext insulation potential, I am limited by there not being any overhang on the gable ends. From outside of framing to outside of sheathing/ext insulation needs to be 1.5″ max. I could do Zip R6, but I see the equivalent in separate sheathing to foam I wouldn’t have the depth for nailing strapping.
Does anyone have any advice? How would you tackle this? I’ll include a picture of a reframed section of wall that was rotted out for context.
Thanks!
Stephen
GBA Detail Library
A collection of one thousand construction details organized by climate and house part
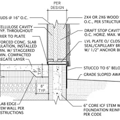
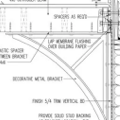
Replies
salxdunn,
I moved from such a home some years ago. All the deficiencies plus balloon framing and a much wetter CZ. Good thing you are in the dry part of CZ6 as you will need all the grace you can get to handle humidity loads. Plaster of that age can be a moisture problem because the surface has so much paint vapor can't get out. The back side of the plaster is of course open to the myriad vapor/air openings and ready to absorb. The saggy, soggy insulation is a good indicator of general loads over time. Wait until you get to the bathroom (if any) and pray the lath is still holding onto something. My plaster bath was quite the experience once I got into to it.
A dry to interior set up is probably going to be the best you can aim for. The 10,000 air leaks and gaps you currently have, have left their marks. The windows may have been poorly flashed, but if they were pocket weighted double or single hung, a lot of condensation likely worked on rotting the frame as well. Keep an eye on the sills and rim boards for rot and or insect invasion.
The overall total leakiness inside to out is what has kept your house (and mine) from completely sogging all wood. That and the heat loss through the walls. You will need to think about where your condensing points will fall in the final wall build you choose. My first impulse would be to set rockwool in the bays, not spray foam to protect the framing from experiencing the deeper cold point foam creates. It is true the closed cell foam will provide direct protection from vapor over more area of each stud, but this also reduces the surface area available for outward surrender of the moisture load as the seasonal situation changes.
Rockwool batts are permeable and allow for greater surface area for exchange. The batts are also much stiffer than fiberglass batts and will stay in place better over time. The lack of facing may seem like the sheathing will be more exposed to build up, but for this kind of house and wall finishes it will pay to keep permeability high in the stud bays. Any dreams of anything like a intelligent vapor barrier scenario are not happening.
You will need to be mindful when removing the board sheathing that you are also removing the wracking resistance on one side of the wall. I would be very hesitant to remove more than 8-9 foot sections without engineering confirmation. Interior finishes are providing similar wracking resistance, but given the mix of materials, I would not rely on them entirely during the rehab.
I am not entirely clear on the way you describe the limits thanks to the zero overhang gable ends. I can think of a few fudge moves to make up for some extra exterior insulation thickness, but if you are seriously stuck for depth your being in a dry climate can mean a reduced over-all risk of moisture build up. Maybe some more photos of bigger file size so detail can be seen.
If ZipR is the only practical option, it would be best to have an engineer verify that this will meet the same stiffness as the sheathing boards provided. Alternately, you could have him provide plans for let in bracing. Windows and other things may complicate this approach.
Onslow,
Thanks for your response!
First, let me clarify a few of my points I perhaps didn't communicate clearly.
1. Concerning the gable end overhang, I mean that there is no soffit. The fascia under the rake drip edge of the roof sits directly on the frieze board where the siding terminates. More plainly, when the siding and current sheathing is removed, outside of framing to outside of frieze board is ~2", and the entire assembly outboard of framing to the outside of finish siding needs to be contained within that two inches or the wall assembly will be beyond the roof, at least on the gable ends. This is why I feel pushed towards zip-R over ply>ext insul>strapping>siding; so the sheathing and siding nailer is integrated into one and I don't have to account for another 3/4" in depth for strapping.
2. Concerning cavity spray foam. I didn't mean spray foaming the entire cavity. My main sources for various approaches for cavity insulation have been IRC tables R702.7(4) and (3). Of course I would love to be able to slap on ≥ exterior R 7.5 as recommended for class 3 interior vapor retarders for drying to the inside purposes, achieving that exterior R value would run me into the no-soffit issue. So my eyes settled on the recommended continuous ext insulation of ≥ R3 for pairing with a class 2 interior VR. So concerning the use of spray foam, my best idea for achieving a class 2 VR install from the outside was to use rigid foam (say 1" thick for the sake of example) cut slightly undersized and sealing the edges to the framing with spray foam. The majority of the cavity and framing would be insulated in a different way, probably cellulose given the now custom depth of the cavity. My logic in this was to air seal as best as possible, not necessarily vapor seal. I am also wary of this middle of the road option without a clearly vapor open direction, thus my leaving a question mark by the exact materials to use, and their perm ratings.
So do you mind if I ask the order of assembly you would recommend? Rockwool directly in the bays? I do have concerns at the least about air sealing gaps around outlets and other obvious penetrations if achieving some sort intelligent vapor barrier is impractical. If the exterior insulation is insufficient to keep that point of condensation at bay, wouldn't I be compromising back of sheathing/outside of framing. Or is that your logic in Rockwool? Anticipate moisture but choose resilient materials and keep things vapor open in both directions? How would you incorporate what kind of exterior insulation?
Sorry for the million questions. I would offer more pictures but this is not my house (thank god). I'm an experienced carpenter recently gone into business for myself, but I am not as learned in building science as I would like to be and I am doing my best to change that. As an employee building new homes, the assembly was almost always some variation of "perfect wall", so attempting those standards in old houses is relatively new to me. I had mostly been aiming for small to medium projects (ample in my area) but this client took a liking to me and gave me gradually bigger and bigger projects. So here I am, but I like a challenge!
salxdunn,
I may have mistakenly lumped you in with another OP in Colorado, so you might be in the wet part of CZ6A not Colorado. All of Colorado is considered in the B zone of reduced humidity and sometimes rainfall.
I am ruminating on your situation and need a bit of time. Family arrived for the holiday and I am sneeking this in.
Hey, thanks! No rush here. And no secret I care keeping that I am in Vermont. I'm onto a few other projects while the other client perhaps ruminates on her choice in renovations!
Stephen
salxdunn,
Finally found your post fourteen levels down. I am basically very leery of how to best handle this bucket of worms. Being in Vermont will likely mean an extended cold cycle for any wall insulation method. Given the leaky interior details combined with a currently restricted exterior insulation option, I am afraid that your risk of long periods of condensation on the back of your exterior foam will lead to problems over time. The summer "drying" period may not be long enough what with the higher summer humidity in your region.
Once you put foam on the exterior the wall becomes a dry to interior setup. With no way of controlling the interior surfaces for vapor/air transfer it becomes very important to up the exterior foam R levels. You haven't indicated how much eave over hang you have to work with. Are you going to have problems on those walls like the gable ends? Will you be re-doing the window openings? Plans on flashing same?
I have been wracking my brain for some clever way to extend (without re-roofing) the gable end roof overhang that would allow for a proper amount of R value to the interior framing into safer territory over more of the year. Unfortunately, I have not been able to figure out an answer. I would suggest poking at Mr. Halladay for some local Yankee ingenuity on the matter, but he is/has retired from GBA for the most part.
Maybe chanting "Help me Obi Wan Kenobe" will bring him back long enough to save your project. Worth a try. Sorry I can't offer a better answer.
Former spray/injection foamer in VT ...
I would use slow-rise, injectable closed-cell foam in the walls.
https://www.dap.com/products-projects/product-categories/spray-foam-insulation/spray-foam-insulation-kits-refills/slow-rise/
I would cut 4' X 8' sheets of zip r (into 2' X 8" sections), then screw these to the studs.
Do two, 1-foot "lifts" of foam ...
Build a test wall to time how long a "shot of foam" will fill one foot.
Thanks for everyone's responses!
The problem ended up solving itself. My client told me she planned to re-roof anyways, and she liked the idea of creating the overhang we would need to get adequate exterior insulation. So with that off my mind, I will be pretty happy to blow cellulose in those cavities. Thanks again for your careful consideration and seeking out the thread again!
Stephen