Wall assembly in Vermont for Habitat for Humanity

Attached is a proposed wall assembly for a Habitat for Humanity, single family, one story house, in Vermont to meet the High Performance Standard per Efficiency Vermont. It uses a double stud wall on a insulated slab foundation. The interior wall is bearing and supports a roof only (we got some 2×12’s for rafters donated). As I have not seen something quite like this I’m wondering if you see problems with it?
And, there is a dream of preassembling wall sections on the State House lawn but I am lobbying against it. It will need a very flat sound surface to assemble properly and I’m sure there will be bugs to fix.
Many thanks, Neil
GBA Detail Library
A collection of one thousand construction details organized by climate and house part
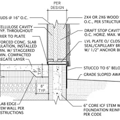
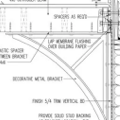
Replies
Seems like it would be simpler (and more volunteer friendly) and perhaps lower material costs to make the studs shorter and let the ceiling joists bear on top of both studs.
Why do you want to hang the ceiling joists from the wall?
If this has something to do with the donated 2x12's, be wary of letting a donation drive you to do something - the donations need to fit the mission, not the other way around.
Also, many affiliates have done off site builds for publicity and move the wall sections into place. There is probably even a procedure for this. Contanct HfH International and they can help with resources for lessons learned and how they have created a flat surface - Probably build a floor system on the uneven surface and shim it to level, and then go from there. Building off site is never the most efficient but is sometimes does wonders to raise awareness and funds, which are also part of the mission.
Somewhat complicated about the ceiling joists and soffits and ERVs, but that's not the question. The question is about the wall assembly. Is it a reasonable wall system and is there something I'm not thinking of with it?
Building on the State House lawn would be a nice publicity stunt but at this point my opinion is it's more trouble than it's worth. Creating a flat surface on a lawn I have serious doubts about. Perhaps 2 ML beams could be set up parallel about 7 feet apart and leveled to each other on saw horses (or concrete blocks or some such) to lay the studs across and work up from there but.... Keeping them level to each other as weight is added and over several days will be a challenge.
Have you had an engineer look at it?
I'm not an expert, but it seems flimsy around the windows. It doesn't say the spacing of the rafters or the width of the windows, but it seems to me that unless you have a stud directly under the rafter you need a double 2x top plate and doubled studs alongside the windows.
It seems like the outer wall is supported entirely by plywood gussets, am I reading that right? I'd want an engineer to opine on that.
If you want to assemble the walls off-site, I'd use the 2x12's you have for the rafters to build a platform to assemble on. Put it together with screws and then unscrew them when you're done and put them up on the roof.
Rafters line up with the wall studs. The inner wall is structural, the outer wall is supported by plywood gussets off of it, construction adhesive and nailed to the inner wall. Plywood top and bottom plate because plywood does not shrink, or come warped and out of true. The plywood laps the joints in the 2x4 top plate.
I have concern the let-in shear bracing will weaken the 2x4s too much. Can metal strap bracing, without letting it in, be effective enough?
Openings at windows and doors will need a king and jack stud either side.
Building a platform for the preassemble has the problem of keeping it supported, level, and weather protected on a lawn over several weekends. It would need to be built and dis-assembled quickly. And probably people will dance on it between times. Why I am opposed to it, but I'm only one voice in the group.
"Rafters line up with the wall studs."
So do you have no windows or doors in the eave walls? Or are they all under 24"? Or is the rafter spacing wider?
"The inner wall is structural, the outer wall is supported by plywood gussets off of it, construction adhesive and nailed to the inner wall."
I got that. The outer wall has to support its own weight, which includes the weight of the window in it. And possibly doors, or are they mounted as "innies"? It's cantilevered 6.5" over the foundation, held up only by 3/4" plywood below and a gusset. Any movement in that wall could cause the waterproofing around the windows to fail which would be serious. Even if the door is set as an innie, the 3/4" bottom plate has to extend over the insulation, that's a big, wide unsupported and overhung piece of plywood, flexing would be problematic. And people will be walking on it.
In any case this is not a prescriptive assembly, and even though you say it's not structural it really is, while it's not holding up the roof it is holding up key parts of the structure. It needs to be approved by a structural engineer. Which I am not, I'm just a guy on the internet with an opinion.
I design a lot of double-stud projects and this looks mostly good to me.
The note that the interior wall is the structural wall is very important, but the outer wall will also carry some load from cladding, and especially from windows. When I proposed a very similar assembly, my engineer beefed up the bottom plate to a 4x12.
Intello is spec'd as the air barrier. I recommend treating the sheathing as the air control layer, and the Intello as the vapor control layer. The Intello can also be a secondary air control layer but it's hard to keep it continuous, which is important for an air control layer.
As long as the siding remains vinyl, you shouldn't need a separate rain screen, but if the cladding changes, you should add a rain screen.
2x3s are usually not very good quality, or longer than 8'. I would use 2x4s instead.
The water table flashing, and all flashing, should be taped to the sheathing. You might be surprised how important that is, and how often it's overlooked because people think cladding keeps water out. Vinyl is particularly leaky, which is why you don't need a separate rain screen.
Is there a detail for what happens at exterior doors? How about window sill and flashing details? Are there any large windows or doors?
Thank you,
The doors will be innies or middies and supported on the slab. The sill outside of them will be fully supported and connected to a deck. I'm not worried about that.
The window opening widths will be less than 33" so they are are small. And there will be a king post either side next to an inner stud to add support for the plywood surround.
Openings will be flashed, window flanges taped to the sheathing
The 2x3's we have been getting have been surprisingly good. I only need 8' lengths. I went with them to reduce load on the exterior wall layer that overhangs the insulation and cost. Also why vinyl siding. Perhaps there is a way to connect the outer layer to the rafters (hurricane clip for both the inner and outer stud layers) to aid in support. I'd not want to use a 4x12 if I can help it.
Neil,
I wonder if you could provide support for the outer cantilevered wall by making the plywood gussets taller so they could resist the verticals loads, a bit like a Larson Truss?
Good luck with your project!
Deleted
I know you didn't come here to have your project re-designed, but I think it would be a lot simpler to put the bearing wall on the outside. Have it rest on the concrete, just build it like a normal exterior wall. The sheathing is your bracing and air barrier, no need to worry about letting in bracing. The interior wall then becomes truly interior and rests on the slab floor, no need for gussets. You can get rid of the exterior foam which is going to be a pain to install and allows a pathway into the house for insects and rodents. If you have a deck it can bolt to the foundation. You can do the whole thing as a prescriptive design, no need to involve engineers.
That's how I usually do it, but with a raised slab and stepped stem wall. In a cold climate the interior slab needs to be insulated from the cold outdoor air. If you want to do a mono-pour slab, the insulation has to go on the exterior.