Opinions on this Wall Assembly for Climate Zone 6

First timer here, so be gentle with me…
Just under 2 years out from building my retirement home in southeastern (Harrison) Maine (Zone 6) and have been doing a ton of reading on wall assemblies. Looking to construct a energy efficient house, but not to passive house standards… I am willing to spend the money for a good product, but not ridiculous amounts.
Here are my thoughts right now.
2×6 walls… unsure as to if I’m going to frame 16, 19.2 or 24 OC
zip r3 sheathing
Dap Air Stop to airseal the framing.
2”closed cell (flash) for vapor barrier
3.5” of Rockwool (batt) for fire properties and dries out if it does get wet.
5/8 drywall on the inside
Hardie Cement siding with Keene easy fur for a rain screen behind.
looking for recommendations… most notably do I need the 2” closed cell for a vapor barrier (I think I do) or can I just fill the whole cavity with thicker Rockwool?
Thanks
GBA Detail Library
A collection of one thousand construction details organized by climate and house part
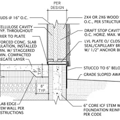
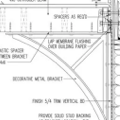
Replies
Hi Willy,
Welcome to GBA!
Your proposed wall will work but your whole-wall R Value will be around R-24. I suspect you could build a wall with a much higher R-Value for same cost as the one you are proposing. There are lots of great builders/designers in Maine that could help.
Back to your wall:
"do I need the 2” closed cell for a vapor barrier (I think I do) or can I just fill the whole cavity with thicker Rockwool?"
In your climate, exterior rigid foam should constitute about 30% or more of the wall's R-value. The exterior R3 foam in your wall is not thick enough to bring the interior sheathing above dew point in winter in your climate. However, the CC spray foam mitigates this risk by acting as a vapor retarder. If your exterior foam were thicker and/or your stud walls thinner, then you could get by without using closed cell spray foam.
Some other quick thoughts on your wall:
1. How were you planning on using the DAP Air Stop? I would avoid sealing the stud cavities with DAP (I think that it is how it is often used). That will be laborious and superfluous with spray foam anyway. Tape the seams of your sheathing and take care to tie the roof with the foundation and ceiling air barriers. Air sealing wall sheathing is wicked easy. Its the transition points and ceiling that are difficult.
2. Most spray foam has a blowing agent that is really bad for the environment. Insist that your insulation contractor use a newer spray foam that doesn't use the harsh blowing agents, like this one: https://www.demilec.com/products/closed-cell-insulation/heatlok-hfo-pro
Good luck!
> The exterior R3 foam in your wall
Note that the R3 foam in this wall isn't exterior. The sheathing will be cold.
Rick,
Thanks for the words...
1. I’m just using the dap to hit a few of the big ticket items in the framing around corners etc., not planning on treating all the framing. I am going to use zip liquid flash to seal the joints, window sills and cover the foundation to floor transition...I figure this will handle 75% of the air sealing, the closed cell vapor barrier should handle a majority of the rest of the air sealing....
2. Thanks for the link... yup I’m planning on trying to using the least harmful blowing agents i can find. I had been reading about Icynene but had not seen demilec.
Welcome to GBA, Willy,
I think the discussion that follows this article might be of interest to you (and although you have worked out your assembly for the most part, I bet the article itself will be too): Five Walls that Work. Also, regarding blowing agents, this article about a new product called Foamular NGX went up yesterday:XPS Makers Announce More Planet-Friendly Formulations. It’s an XPS rigid foam alternative, which I realize you aren’t considering, but since you are aware of and concerned about blowing agents, I thought I’d share it.
Hi Willy,
I'm in the same boat, but CZ 6b so perhaps not quite so concerned about moisture. I'm thinking the best solution that is traditional construction (i.e. easy to build), efficient, and low cost is, from the inside (after 5/8" drywall):
1) advanced framing - 24 OC 2x6, insulated headers, etc
2) dense pack cellulose in bays (green, good moisture control, a bit more "thermal buffering" (that'll likely generate comments ....)
3) OSB covered with WRB (this is the primary air barrier; taped and detailed appropriately)
4) 2" rigid foam; preferably used polyiso, but not sure this is practical due to facing on most used foam. This is the drainage plane so also needs to be taped & detailed appropriately.
5) strapping and cladding (likely 1x4 then HardiPlank)
The zip sheathing seems desirable, but also quite expensive. I'm not sure whether the labor savings of Zip even come close to the additional material costs - hopefully others can comment on this.
Here are two important references for wall design. Follow at least one of them.
Table 2 A or B here
https://www.appliedbuildingtech.com/system/files/200311_abtg_rr_1701-01_moisture_control_guidelines_figure_update_final.pdf
https://www.continuousinsulation.org/content/2021-ibc-and-irc-adopt-improved-vapor-retarder-requirements
I just purchased a load of Foamular. Some was labeled the new low GWP formulation, so it's working into the pipeline. I, too, vote for exterior insulation. 3" of foam over conventional framing, and you're there. No spray foam, no interior vapor retarder, and the framer builds what he normally builds. You can use 2x4 or 2x6 walls. You can decide on osb or zip choice based on price (have you priced zip lately?), and place your air/water barrier where you need it. I'm in zone 5 and 3" of foam gave me options for substituting one layer with ledgers to add porch roofs and decks. I extended the 3" XPS down to the footing for crawl space insulation.