Wall assembly for Zone 5

We build in Climate Zone 5 and our typical wall assembly is 2×6 studs with BIBS (blown-in fiberglass) and 1” Halo foam. We have a vapor barrier inside and have started trying to push our clients to use Aerobarrier. We use let-in bracing or metal T braces whenever possible and not OSB.
Do you think there is a mold or rot potential with this assembly?
After reading several of the articles here it seemed like this may be an issue but it seemed like I may be in a zone low enough that it was not and or the fact that we are not using OSB may also be a good thing but I could not find any mention where Builders were not using a sheathing.
Thanks for any any helpful advice
GBA Detail Library
A collection of one thousand construction details organized by climate and house part
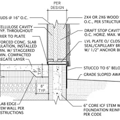
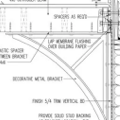
Replies
Justin,
I assume that when you are talking about 1-inch Halo foam, you're talking about graphite-enhanced EPS with an R-value of R-5. I'm also assuming that you install the rigid foam on the exterior side of the studs, not the interior -- and that when you say that you have "a vapor barrier inside," you're talking about polyethylene.
Here is a link to an article that addresses your question: "Calculating the Minimum Thickness of Rigid Foam Sheathing." In your climate zone, if you want to install rigid foam on the exterior side of a 2x6 wall, the rigid foam should have a minimum R-value of R-7.5. You've chosen rigid foam with an R-value of R-5, which isn't enough. That means that, in theory, you might get wintertime condensation on the interior side of the rigid foam.
Field experience has shown, however, that walls like yours that "break the rules" are usually OK, especially if the walls include interior polyethylene. Here is a link to an article that discusses walls that break the rules: "Rethinking the Rules on Minimum Foam Thickness."
My advice? Thicker rigid foam would be better than the R-5 you're using. But other builders have broken the rules and lived to tell the tale.
Mind you, Halo Exterra exterior sheathing is low density graphite loaded EPS that is could test as high as 75 ng/Pa-s-m2 (1.3 US perms) @ 1.5" (it's specified as 1.34 perms max @ 1.5" based on Neopor testing, no typ given) is more vapor permeable (and less moisture susceptible than) OSB or CDX. With a Class-II vapor retarder on the interior and any sort of rainscreen gap to the siding this is not a risky assembly.
http://www.amcfoam.com/PDFs/Halo%20MPDS.pdf
The wall assembly described doen't specify what's on the exterior side of the Exterra though.
I would follow the recommendations below. Including this:
"Avoidance of the installation of vapor barriers such as polyethylene vapor barriers, foil faced batt insulation and reflective radiant barrier foil insulation on the interior of air-conditioned assemblies – a practice that has been linked with moldy buildings "
https://www.buildingscience.com/documents/digests/bsd-106-understanding-vapor-barriers
If you feel there is a conflict between Class II and Class III recommendations, use MemBrain.
Justin -
It's important to remember that vapor retarder recommendation/code requirements are all about managing moisture by diffusion. Way more important to get your air sealing done right than to worry about walls getting wet by diffusion.
So, investigating AeroBarrier may be a good move. And check with AB on exactly which cavity fill insulations support including AeroBarrier. If the cavity fill is too air permeable--such as fiberglass batt--you can't use AeroBarrier.
Peter