Wall assembly

I am building a new home in zone 5 ( nw Wyoming) My plan is for 2 x 4 walls with 2 inches of cc spray foan on the interior, zip sheathing, 1 1/2 inches of xps rigid foam. Then 2 x 4 furring strips with an additional 1 1/2 inches of xps between the strips covered with a combination of metal and cedar siding. I am also going to cover the xps with tyvec for proper flashing for the windows. Is this wall assembly a good idea?
GBA Detail Library
A collection of one thousand construction details organized by climate and house part
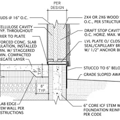
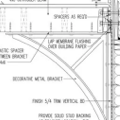
Replies
Charles,
Your plan has some good features, as well as some not-so-good features.
The best feature is your plan to install two layers of rigid foam on the exterior of your wall. That makes sense.
Your choice of Zip sheathing (presumably, with taped seams) is a good one.
Here are some suggestions to improve your wall:
1. You don't want to cut up any of the rigid foam into narrow panels and insert these panels between your furring strips. Instead, you should install both layers of rigid foam as continuous layers. Stagger the seams so that the second layer of foam covers the seams of the first layer. Once you have installed two layers of rigid foam, you can install vertical furring strips (either 16 inches o.c. or 24 inches o.c. -- whatever you need to do to match your stud spacing). You can use 1x4s as furring strips -- you don't need 2x4s.
There are many reasons for my advice. The continuous layers of rigid foam perform better (from a thermal perspective) than your approach, with cut-up panels of rigid foam. Another point: you want to have an air space between your siding and the rigid foam, in order to create a rainscreen gap. Your plan has no gap. Here is a link to an article with more information on rainscreen gaps: All About Rainscreens.
2. EPS (expanded polystyrene) is a better choice than XPS, because XPS is manufactured with a blowing agent that has a high global warming potential.
3. Once you have installed your two layers of rigid foam (following the guidelines in this article: Calculating the Minimum Thickness of Rigid Foam Sheathing), you need to choose what type of insulation to install between your studs. I advise you to install cellulose insulation, since cellulose is vapor-permeable -- it will allow the wall to dry to the interior if it ever gets damp. This choice is much better than closed-cell spray foam, which is vapor-impermeable (it interferes with inward drying), expensive, and manufactured with a blowing agent that has a high global warming potential. Mineral wool batts or carefully installed fiberglass batts would also work. If you take my advice, you should switch to 2x6 studs, to allow for a little more insulation in your walls.
4. At every stage of the construction process, remember to pay attention to airtightness.
Zone 5 in NW Wyoming? I'm surprised. I would have expected zone 6 at minimum. I see only two counties in Wyoming listed as zone 5 in SW Wyoming (http://en.openei.org/wiki/Climate_Zone_Number_5)
Martin, The reason for using 2 x 4 is that cedar manufacturers recommend fasteners to penetrate 1 1/2 inches into solid wood. My area often has winds in excess or 50 mph. The reason for filling between these was to not have that large of a rain gap. Perhaps just 1 inch of fill. The reason for closed cell is for air sealing. I am planning on using the 2 inch layer up the walls and on the underside of the roof deck. Additional open cell to reach the needed 49 r value on the roof. My thought was a totally air sealed assembly. My part of Wyoming is high desert with extremely low humidity levels.
Charles,
I've given you some advice, but of course you can build the house any way you want.
If you use taped Zip sheathing, and you seal your penetrations and transitions, you won't need closed-cell spray foam for air sealing purposes.
You can certainly use 2x4 furring strips if you want. I would still install the rigid foam in a continuous layer rather than cutting it into narrow strips.
If you want the belt-and-suspenders approach to air sealing of using taped seams plus spray foam, you could consider open-cell spray foam to:
1) Save money.
2) Avoid the major climate impact of the closed-cell blowing agent
3) Allow drying as Martin notes as an advantage for cellulose.
I would choose cellulose, as Martin suggests, but it is true that either open or closed cell foam would do more to seal up any spots that somehow escape being sealed otherwise.
Martin, I appreciate the advise. Most of what I have learned has been from this forum. I will modify the plan to incorporate your input. Thanks. BTW I meant zone 6.
What Charlie & Martin said. With as little as 2" of EPS on the exterior you would have more than sufficient dew-point control against interior moisture drives at the sheathing in zone 6 with a full-fill of open cell foam (or R15 fiber, if you went that route.)
A full fill 3.5" of half-pound foam you'd have higher performance than 2" of closed cell, due to the longer path through the studs, and it would use less total polymer than 1" of closed cell foam, less than half the polymer of 2" closed cell. Between the lower total polymer use, and the fact that open cell foam is using water as blowing agent instead of HFC245fa it would be a lot nicer to the planet. Open cell foam would air seal as-well or better at 3.5" than 2" of closed cell foam too.
Of course, R15 rock wool would be slightly higher performance, and nicer than open cell foam. Cellulose would be about the same performance as 3.5" of o.c. foam, (still higher performance in the assembly than 2" of closed cell foam, remember), and nicer to the planet than R15 rock wool.
On this wall assembly, in a CZ6 with 2x6, OSB, 2" polyiso insulation board, WRB, rainscreen furring, and exterior cladding...does there need to be a membrane of any sort between the drywall and studs inside the house?
Thanks.
Steve,
Q. "Does there need to be a membrane of any sort between the drywall and studs inside the house?"
A. No.
Martin is probably being a bit coy here, since you haven't specified any cavity insulation. In zone 6 the real world performance of 2" polyiso is a bit marginal for that assembly if you also put fiber insulation in the stud bays.
IRC chapter 7 prescribes R11.25 minimum for using class-III vapor retarders on the interior of a fiber-insulated 2x6 wall. At 2" the labeled performance of 2" polyiso would be R12 -R13, but the real wintertime performance would be R10-ish when the foam on the exterior side of the assembly. With truly air-tight drywall and latex paint it'll probably do just fine, but 2.5-3" would be better.
Thanks Dana and Martin, Sorry I forgot to mention cavity insulation is cellulose between the 2x6 studs. I'm pretty sure just 2" of polyiso only won't cut it in this CZ6 that hit -18 a couple weeks ago ;-)
Also, can foil faced polyiso be taped and act as the WRB? How might polyiso be affected behind a rusted corrugated steel clad wall that is west facing in 95 degree summer heat? This will be a rainscreen wall, but am I best to use a foil faced polyiso, or is the paper/fiberglass OK considering the heat that might build up behind the steel (could it melt)?
Thanks again for your help :-)
Thanks for everyone's response. After a looong conversation with the building inspector this is my plan for the insulation. I am bringing rigid foam panels (R 20) on the exterior, from the basement footer up the walls to the trusses. The ground level walls will have open cell foam sprayed in the cavity also. No interior insulation on the basement walls. I am using r 49 blown in cellulose on the ceiling deck. 2 questions. 1. Should I insulate the rim joists from the inside? If so should I use closed cell or open cell? What thickness? 2. Since the roof will be ventilated I want to air seal at the wall rafter connection. After installing a vent channel should I use closed cell or open cell at this connection? What thickness?
Steve,
Q. "Can foil-faced polyiso be taped and act as the WRB?"
A. Here is a link to an article that will answer your question: Using Rigid Foam As a Water-Resistive Barrier.
Steve: It's fine to use other facers, but it won't make much of a difference from a moisture perspective- it still has to be set up to dry toward the interior.
Polyiso doesn't melt, so no matter how hot it gets under the steel siding you won't see thermoplastic deformation of the foam (with polystyrene you could, if the temps got north of 200F.) By the time it got hot enough to melt polyiso, wooden girts or furring holding steel siding would be literally smoking hot.
Charles: With R20 on the exterior it's fine to use open cell foam on the interior of the band joists. Open cell is also fine for air sealing at the wall/rafter connection, if the exterior side of the wall is still R20 at that point.