Opinions on This Wall Assembly

Hi! Thank you for your help in advance. I am seeking an opinion regarding a wall assembly (New York Zone 5). The area is a basement (rather a walkout, please see a picture) build out of cinder blocks. Cinder blocks are covered with tar paper (only half of the wall fully below grade). Looking at 70 years old walls, I can tell that mold (perhaps some water) has entered the area in the past. I have not seen it in a liquid from (perhaps it is more like sweating and dampness), but cardboard boxes left on the slab disintegrated (perhaps it is coming from the slab). Photos of walls and what is behind them attached (wood paneling is 30 years old, not sure about the drywall).
I am considering building a french drain (is it necessary?) inside of the house and staple a dimple mat directly on the tar paper so the water can escape to the drain. Next I am considering foam boards (perhaps FOAMULAR NGX which can supposedly get wet, according to the manufacturer), planning to spray foam sill plate\rim joist area. Then I would like to build studs and likely rockwool in between them. Will top it with drywall and paint. Will do 6 mil poly on the slab before laying a vinyl floor. Obviously, waterproofing is done best on the outside, but this is cost prohibitive and not in consideration. Not expecting miracles. Trying to apply the best solution possible while keeping a cost somewhat reasonable, and not ending with a major mold problem. At the end, I still plan to install a central dehumidifier as part of HVAC system (as mentioned I would like to utilize the space as a living area, not “just” basement), but would like to minimize the “wet problem”.
Questions:
· Any red flags regarding the aforementioned wall assembly? Am I missing anything?
· Can the foam boards get in contact with the concrete slab at the bottom or should I have some other material between them?
· Floor joists rest on cinder blocks, hoping that air space crated by the dimple mat will not lead to mold production and then floor joists rotting, any concerns here? Second story is a brick as you can see (there is no flashing etc.)
Thank you!
GBA Detail Library
A collection of one thousand construction details organized by climate and house part
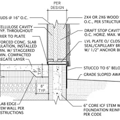
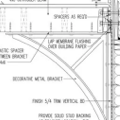
Replies
Search function is always helpful, some of my questions have been answered here - https://www.greenbuildingadvisor.com/question/basement-insulation-19#comment-206269
So I am still debating if I need internal french drain and the dimple mat, I guess I should go for it just to be save, and as I posted in the other thread, can this:
" So the best compromise here would be to install 1.5"-2" of unfaced Type VIII EPS (1.25lbs per cubic foot nominal density) trapped to the foundation with a 2x4/R11+ studwall,"
be replaced with foamular ngx (supposedly much less toxic gases and can get wet, not sure if I can believe it, but that less toxicity is driving my choice here, would prefer not to breathe it in), and can it be pair with R15 rockwool (2x4 wall) bats and not worry about condensation?
Can XPS get in touch with the slab?
The foam manufacturer claims Air Permeability at 75 Pa (L/s.m2), Negligible (0.001), but I do not fully understand this statement, I am not sure what thickness is that.
Thank you!
XPS can be in contact with the slab. Polyiso is the type of rigid foam that should have a gap to avoid water wicking issues. XPS can be used under the slab, on top of the slab, just about anywhere, without fear of water issues -- but you do need to provide a fire barrier if on the interior.
If you're worried about bulk water intrusion, the best solution (assuming you don't want to fix it on the exterior of the wall), would be to put a dimple mat behind the rigid foam, and have that dimple mat drain into a perimeter drain.
Bill
Sebastian,
I'll ask a question and give your post a bump. Is there any evidence of bulk water entering the basement?
Thank you for the bump. No bulk water entry at all. We just had two days when it rained continuously and the walls remained dry.
The 6mil poly with the vinyl on top may be a problem. I don’t want to bring it up again because we discussed it many times but you will have to think over that assembly. Some will say fine others will say moisture trap causing mold under the vinyl
Thank you for bringing this up, and for the nice and short summary. So an alternative is no poly, let the slab breath, and put vinyl directly on it? Thank you.
Vinyl flooring is about .05 perms. 6 mil poly is about .06 perms - which can result in more wetting than drying. 15 mil STEGO WRAP is < .01 perms - a better perm ratio that would be compliant with:
"ACI 302.2R-06, Guide for Concrete Slabs that Receive Moisture Sensitive Flooring Materials, has suggested that use of materials having 0.01 perms or less in situations where extremely sensitive flooring materials require protection"
As you are recommending it I assume it can put on the top of the slab? Asking as all info I can find referenced below slab application. In this case I would basically try to keep all moisture underneath STEGO WRAP, correct? Thank you!
I was able to get in touch with an original home owner (their father built the house in 1950s). There was never a water problem, apart one seepage after extreme downpour, and walls visible on photographs are over 60 years old. Not much mold there as for 60 years (at least for my taste). Slab and tile floor was always setting. Last but not least, supposedly there is a plenty pf footing drainage installed.
So are you saying 15 mil poly over concrete with vinyl on top actually meets building code. Not sure what ACI stands for but assuming it has to do with concrete
I don't know about code, but it fits better with theory and with recommendations from an organization that should know.