Wall Assemblies – Spray Foam vs Exterior rigid + cavity batt

I am wondering if there is a reliable tool or website out there to compare wall assemblies in terms of their thermal performance, including factors such as installation limitations?
Ekotrope (https://www.ekotrope.com/r-value-calculator) seems good but results cannot be saved and comparisons are not possible side-by-side.
Martin Holladay in his blog “Closed-cell foam between studs is a waste” (attached PDF) from Aug/Sept 2017 demonstrated how an actual foamed out 2x stud wall is likely to be less insulating than on paper due to the difficult trimmability of closed cell foam raised proud of the face of studs.
According to his blog the whole-wall R-value of a 2×6 wall is usually only 15.4, which accounts for the thermal bridging of the studs as well.
The finished assembly would in reality have drywall on the inside and ply+ finish (i.e. siding) on the outside, so the R would be a bit higher.
Per http://www.ekotrope.com/r-value-calculator such assembly is actually at 21.7, which means there is a discrepancy between Martin’s calcs and this one.
You see the confusion and my hope for a precise and reliable tool.
It should include the ability to run exterior monolithic insulation calcs:
Per http://www.builderscalculator.com/wall-r-value-calculator-for-wood-framed-walls/ a 2×6 Rockwool batt insulated wall with foil faced 1.5″ exterior Polyiso comes to R-26.21.
BTW, that calculator does not include a ventilated space behind the exterior siding, which is a construction liability and denies the assembly of an additional R-gain.
Considering the above discrepancies and tricky construction methodologies, it would be great to have a good wall assembly calculator, and please with save-able PDF results.
In my case I am designing a house in which the contractor chose to go with spray foam vs exterior insulation and I would like to make a case for the exterior foam. (This is climate zone 3, Bay Area.)
Such a tool would make a big difference.
Thanks!
Matthias
GBA Detail Library
A collection of one thousand construction details organized by climate and house part
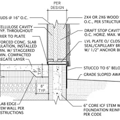
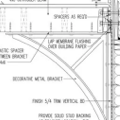
Replies
I'm not aware of any online calculators for this, probably because it's pretty easy to just calculate by hand. You can work out a simple average (which will slightly OVER estimate the whole-wall R value of the wall) by dividing out a stud bay into 1" segments. An example:
Assume 16" stud spacing and a 2x4 studwall with R15 mineral woold batts in the bays. Studs are 1.5" wide, and since each bay includes the half of the stud on either side of the bay, a bay is 16" with 1.5" filled with "stud". Let's allow R1 per inch for the wood, which is probably a bit on the conservative side. The calculation then goes like this: ((1.5" stud * (R1 * 3.5" stud depth)) + (14.5" of stud bay space * R15 mineral wool)) / 16" of total space per stud bay = R13.92 for whole-wall R value for that assembly. That's the simple average. The "real" number is a little different because the energy flow through the studs is a fair bit more than through the insulation, so a simple average is a little optimistic, but still pretty close, and just fine for basic comparison purposes.
Spray foam in a studwall will typically be close to mineral wool performance since you'll never get a full fill with close cell spray foam, and open cell spray foam doesn't have much R value advantage compared to mineral wool. Thermal bridging nearly cancels out the remaining benefit to sprayfoam in terms of R per inch, so you end up pretty close to mineral wool. The simple average for my above example using R6 per inch spray foam 3" thick gives R16.64, so a difference of about R2.7, and that's OVERstated by the average. We're also assuming a perfectly even 3" layer of spray foam, which is probably overly optimistic. In reality, spray foam will tend to be a bit less in the middle and a bit more towards the edges, and that same pesky physics problem comes into play again meaning that you can't just take the average thickness of the spray foam to arrive at a given R value number. I'd bet that in reality, closed cell spray foam in a 2x4 stud wall is unlikely to preform any better than around R15 or so if that, which means spray foam and mineral wool (or high density fiberglass) batts will likely perform the same as ccSPF in a typical studwall. Since everything DOES scale pretty linearly with thicker studs, a 2x6 studwall will show the same relative difference between different insulating materials as a 2x4 studwall using those same materials.
The big advantage to continuous insulation is that it covers the studs too, so you don't have thermal bridging issues (and fasteners through the rigid foam are way, way less of an issue than studs). This means that how ever much rigid foam R value you put up applies directly to the WHOLE WALL R value with no thermal bridging to reduce it's effectiveness. If you add an inch of polyiso to the 2x4 studwall in my original example, that R13.92 goes up to R19.92. For comparison purposes, a typical 2x6 studwall with R21 batts will show around R20.17 whole-wall performance, so only a bit better than an R1 difference from the 2x4 studwall with 1" of continuous insulation. The same applies to a 2x6 wall, which would go up to R26.17 with that same 1" of polyiso.
It's easy to see how upgrading to continuous insulation is a far more effective upgrade compared to using spray foam in place of batts in the studbays.
Bill
This is a pretty good calculator that does some moisture modeling as well:
https://www.ubakus.com/en/r-value-calculator/
You can also browse through here as they have a worked through a large number of wall assemblies:
https://cwc.ca/design-tools/effective-r-calculator/
In your very mild climate, anything high R value won't make much difference in energy use. I can't see spending too much money on wall insulation, SPF is definitely not worth it. I also can't see an ROI for exterior insulation. Maybe if you are tight on space a 2x4 wall with R5 CI is a good compromise.
I would rather focus on getting a simple solid wall with good details built. I would select high density batts (fiberglass or mineral wool) or dense pack for insulation.
Details like proper air sealing, good water management and vented cladding are not hard. These are not big cost adders and make a big difference in durability. Getting the building envelope tight is probably your biggest energy savings, so this is where I would focus most of your efficiency budget. Along with a tight envelope, designing in proper ventilation and air filtering is a must with the ever increasing wildfire threat.