Wall and Roof Assembly for Hot-Humid Zone 1A–Hawaii

I’m building a new custom home designed to look like an early-Hawaiian stucco structure (think thick walls). It’s wood framed with 2×8 stud walls, sheathed with 5/8″ plywood (not OSB), with 3/4″ XPS foam sheathing over that, and clad with 3-coat portland cement stucco. The exterior windows and doors will be recessed 4″ into the walls. We’re using the XPS foam sheathing to reduce thermal bridging through the studs, but also to add wall thickness. The house will be air-conditioned, but in use will mostly be open to the trade-winds.
The proposed wall assembly is as described, but with a layer of drain-wrap (building wrap w/ drainage channels) over the 3/4″ XPS foam, with a layer of Type-D building paper, as a bond-breaker, between that and the stucco. The drain-plane will be between the two layers of building wrap. The walls will be insulated with R-14 of either open or closed cell spray foam.
The roof assembly is proposed to be unvented with the sheetrock ceiling plane at the bottom of the pitched rafters, and insulated with R-19 of closed-cell spray foam applied directly to the bottom of the plywood (not OSB) roof deck. The plywood deck will be covered with a synthetic underlayment with clay-tile roofing over.
Because of the inset windows and doors, my current thinking is that a liquid applied moisture, air, and vapor barrier applied to either the plywood or the XPS wall sheathing, would be an easier and more secure way to achieve a water tight seal around the openings than using a building-wrap. We will use peel and stick flashing around the windows and doors in either case.
The project is near the coast, which I believe is designated as climate-zone 1A. The temperature varies between 62-95 with an average of 83F. Rainfall is approximately 42 inches/year.
Vapor Permeance of materials:
3/4″ XPS: 1.5-Perms
Drain Wrap: 10-Perms
Type-D paper: 5-Perms
Liquid Applied barrier: 5-Perms
Questions:
1. In this climate and considering solar vapor drive, which type of foam is appropriate, open, or closed cell?
2. Are there any issues I should be aware of with using a liquid applied barrier? (In this case
StoGuard, http://www.stocorp.com/index.php/productsandsystems/moisturebarriers/vaporpermeable)
3. The liquid applied barrier is typically applied over the plywood sheating. Are there any problems associated with moving the drain-plane inward between the plywood and XPS sheathing, and would a drain mat, or drain-wrap placed over the liquid applied barrier on the plywood provide a satisfactory drainage-plane?
4. Is there any reason why the liquid applied barrier couldn’t be applied over the XPS sheathing, with either drain-wrap or Type-D paper over that?
5. Which type of spray foam is appropriate for the ventless roof assembly, open, or closed cell?
6. Should the synthetic roof underlayment be vapor-permeable, or does it matter?
7. There is some enclosed attic space above a lanai outside of the conditioned envelope which we would like to be unvented. Is it okay to simply apply 2″ of spray foam to the underside of the roof deck and call it a day, or should the attic walls, and ceiling be insulated as well?
Thank you very much.
GBA Detail Library
A collection of one thousand construction details organized by climate and house part
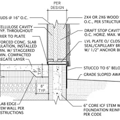
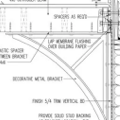
Replies
Aloha Drew. Seems like your design may have budget room for pro services such as Building Science Corporation. Also you need to find the best spray foam contractor in Hawaii. Check with there architects, builders, engineers and build what others build well in Hawaii. Mahalo
Yup, you're right, I could use a pro. I'd love to engage Building Science Corp, but they haven't answered my emails or phone calls. I'd send them a letter, but they don't publish their address.
I already have the best spray foam contractor in Hawaii and he's as eager as I am to get these questions answered. I'd appreciate a referral.
Thanks.
Drew,
Q. "In this climate and considering solar vapor drive, which type of foam is appropriate, open, or closed cell?"
A. Because you are using exterior XPS, I would advise you to use open-cell foam so that the wall asembly can dry to the interior. The XPS layer will prevent any inward solar vapor drive problems.
Q. "Are there any issues I should be aware of with using a liquid applied barrier?"
A. As long as you follow the manufacturer's instructions, I think you will be fine.
Q. "The liquid applied barrier is typically applied over the plywood sheathing. Are there any problems associated with moving the drain-plane inward between the plywood and XPS sheathing, and would a drain mat, or drain-wrap placed over the liquid applied barrier on the plywood provide a satisfactory drainage-plane?"
A. Once you have made a decision on where to put the WRB, make sure that all of your window and door flashings are integrated with that layer. I can't imagine that the WRB will need to handle much (if any) liquid water, but it can't hurt to use a wrinkled or bumpy housewrap product at that layer.
Q. "Is there any reason why the liquid applied barrier couldn't be applied over the XPS sheathing, with either drain-wrap or Type-D paper over that?"
A. I've never heard of anyone doing that. Check with the manufacturer of the liquid-applied WRB. According to my understanding, the Sto products are only approved for use over plywood, OSB, or gypsum sheathing.
Q. "Which type of spray foam is appropriate for the ventless roof assembly, open, or closed cell?"
A. Closed-cell foam.
Q. "Should the synthetic roof underlayment be vapor-permeable, or does it matter?"
A. Manufacturers of synthetic roofing underlayment do not allow their products to be installed on unvented roof assemblies. The only exceptions are the new vapor-permeable synthetic roofing underlayments, and these are very expensive. I suggest that you use asphalt felt.
Q. "There is some enclosed attic space above a lanai outside of the conditioned envelope which we would like to be unvented. Is it okay to simply apply 2" of spray foam to the underside of the roof deck and call it a day, or should the attic walls, and ceiling be insulated as well?"
A. If this area is outside of the conditioned envelope, then it doesn't need any spray foam.
Martin,
Thanks for the response. I should have mentioned that, for aesthetic reasons, the owner doesn't want to vent the attic space that's outside of the envelope. Would 2" of foam under the decking keep the space cool enough and comply with code?
Drew,
I have never heard of anyone choosing to insulate the underside of roof sheathing simply to avoid the requirement to install soffit and ridge vents. I don't think there is any provision of the code that allows for lesser amounts of insulation for people taking this approach. Either the insulation serves to bring the attic within the conditioned space, or you have to vent it.
I suggest that you choose unobtrusive soffit vents and ridge vents. They exist.
Ok, What was this outcome?