Vented vs unvented attic

Hi all, new here and seeking advice.
New construction. 2,200 square foot footprint with full walkout basement under it.
Far Western edge of climate zone 5a. 1/3 of the way up from the South edge of that climate zone.
Walkout basement will be mostly ICF. Planning on 2×6 walls with Rockwool R23 in the cavity, ZIP sheathing and 2 layers of 1.5” Comfortboard 80 externally. Looking for R65 ceiling.
Not going for certification but still shooting for 0.6 ACH50 or better.
My builder has not built to these performance levels before. I’ve studied air sealing to this level quite a bit more than he has so I’ll be helping some with it.
He’s more comfortable with a normal vented attic. I’m having a hard time visualizing the “pencil test” on the ceiling. Is the drywall on the ceiling going to be the air barrier? Or do I need something else? What about light fixtures and other penetrations?
For me it’s easier to visualize a climate controlled attic but I don’t think it’ll be easy to convince him to pursue that route and I want to be respectful of what he is comfortable with.
Thanks
GBA Detail Library
A collection of one thousand construction details organized by climate and house part
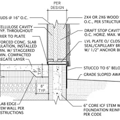
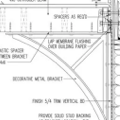
Replies
What ceiling penetrations are you anticipating other than lights and other electrical? Rather than can lights, it's better to put in electrical boxes and flat fixtures. That way you can caulk around the electrical box when the drywall is installed. If you use fiberglass boxes they don't have any holes other than the one you open for the wires, so they're easier to seal.
Some other considerations on vented vs unvented: Do you have significant snow? Vented is less prone to ice damming. Do you have a fire risk? Unvented roofs are safer in wildfires. Do you have hurricane risk? Unvented roofs are less likely to blow off.
To pass the red line test with a vented attic you need to connect your ceiling air barrier to your sheathing.
This can be done a couple of ways, the simplest is a wide piece of flashing tape or a plywood flange installed over the wall top plate before the rafters/trusses are set. You can than connect a sheet good of some kind (6 mil poly, air barrier membrane or OSB) to this flange for air barrier continuity. Since this can be done before any drywall is hung or insulation is installed, you can do a blower test while the walls are open to seal up any major gaps.
For light fixtures, there are also vapor tight device boxes that have a gasketed flange that seals against the drywall. If you want another layer of sealing, there are vapor barrier hats you can install in the attic over the device box as well.
A conditioned attic is an act of desperation and poor planing.
The only time a conditioned attic is useful is when someone insists in the bad idea of putting their HVAC equipment in the attic. Then the silly idea of a conditioned attic with HVAC is marginally better than the stupid idea of HVAC in a vent attic.
The sloped surface of the roof line will have a much larger surface area than the flat ceiling 40% maybe more. The larger surface area will lose 40% more heat than the flat ceiling if it has the same R value.
Insulating the sloped ceiling almost forces you to use expensive and ungreen foam insulation. The high cost of foam insulation leads most people to install fewer Rs of insulation dew to the fact they need to 40% more of something that costs five times as much. It is common for people to end up with less than the code required R value in their spray foam attic.
Every post on this board about a moldy rotten attic comes down to unvented or poorly vented
An unvented attic is complex, expensive and risky choice.
Making the ceiling tight in new construction is not that hard. Before the drywall go in caulk every hole in every top plat in every wall. Mostly wires and a few plumbing vents. 3 or 4 tubes of caulking take less than an hour. Part of your choice to build a tight house means you have decided to forgo recessed lighting as even the “air tight” one leak like sieves. This means 100% of your ceiling light will be mounted to standard round electrical boxes. After the ceiling drywall is up and before the insulation goes in get in the attic with 6 tubes of caulking where the wire come out of every ceiling box and caulk the joint between the box and the drywall. No need to be neat just fill the gaps.
My guess is if you get a bid for an R65 cellulose blown on the attic floor will cost 66% less than. R65 at the roofline.
Be sure to specify staged joints between layers of comfort board.
Before you commit your self to ICF consider the cost VS the benefits. This is a very costly option and it sound nice on the TV shows. Do not forget to include the often over looked required cost that all of interior and exterior foam must be cover dew to the fire risk. Consider other options.
Walta
I'm a big fan of conditioned attics. I won't get into the advantages here but there are many.
Regarding the air barrier question, another well understood approach is to place it at the exterior face of the structural sheathing, the OSB/plywood of your wall and roof. Matt Risinger has featured several homes, including his own, which use this approach.
It requires some thought and planning as far as roof overhangs. But it greatly simplifies the air barrier layer overall because there are very few obstacles and interruptions in it. The most straightforward approach is simply to tape all the sheathing joints before installing the house wrap.
I'll spare you the details here and refer you to Risinger's videos, which are on Youtube as well as his own website.
I design stock home plans and I'm going back through my entire catalog this year and re-detailing them all to use this approach.
I'm in the land of 2.5 story houses, full attics are rare even in older houses and pretty much not existent in new build here. Unfortunately most are done with spray foam.
Whenever I see these larger roof structures with nothing in the attic, the only thing I can think of is all that space that is already enclosed but now is wasted. If you are not limited by height or building footprint, it is still the cheapest and most energy efficient way to build though.
I have yet to see a bolt on overhang detail over rigid that is buildable especially when you are looking for larger ones. Very small one, no problem but even something like the standard 18" one becomes a challenge. Add in there the fact that the roof sheathing should extend over to the overhang and this becomes even more of an issue.
I think the monopoly house type of construction with an unvented roof and taping the walls directly to the roof works well with no overhangs. I've done this, simple to build and looks good. No overhangs are rough on the siding so I would only do it with metal siding. Once you need to add overhangs, I think the simplest is standard construction and a small amount of spray foam to seal the area from the top plate to the roof.
Check out Risinger's videos for overhangs.
And yes, there are limitations to the approach. But for people prepared to work within them there are advantages, such as the elimination of a large number of penetrations that have to be sealed.
The issue is that it is very far from standard build work flow. With enough resources it can be done but the question becomes if it is worth the cost.
There is a good chance of a new roof being built with trusses. Once you are into these 2' height roof spaces, anything unvented becomes a challenge as you now either have to figure out how to hold insulation up aginst the roof deck, need a lot of exterior rigid for condensation control or have to use spray foam. It gets complicated quick:
https://www.jlconline.com/photos/slideshow-overroof-for-a-mid-century-modern-home
Doesn't matter if you are build with lumber, I-joists or trusses, vented is still the simplest way even with cathedral ceilings. With that the air barrier is at the ceiling level so you can have all the overhangs you want for free.
Jgsg,
I agree with Akos: applied overhangs are at best a niche technique. You simply don't get enough benefit from all the added complication they cause for them to make sense in almost all situations.
Exterior air barriers are great at performing one of their two functions (stopping air movement between the conditioned interior and the exterior). But something that often gets lost in discussions about exterior air-barriers on both walls and roofs is that to perform their other task of stopping moist interior air from getting into and condensing in assembles, they need a secondary air barrier on the interior.
Has anyone thought about, or come across, using solar panels as applied overhangs (see picture)?
Your point about exterior air barriers is well made. However, this is not an issue (I think) if you are using appropriate levels of exterior insulation.
I am building a 2000 sqft house with the same goal of .6 ach50. My attic will be vented. The drywall in the ceiling will be an air barrier which is requiring much attention to detail, especially considering that I'm using double stud walls. I am using led recessed lighting, in order to get around the air leaks of these penetration I will create small foam boxes that I will use to cover each light in the attic and spray foam around it to maintain the air barrier.