Vented Roof Cavity?

For annoying reasons (drawings were wrong, framer didn’t catch in time), the roof on an addition we’re doing was built lower than it needed to be to line up with the soffits on the existing house. We decided the easiest solution would be to just build up a 6″ frame on top of the sheathed roofing so that the new higher roof would line up correctly. The original roof is still in place and has 6″ of open cell foam on the underside. The result is that we have a roughly 6″ dead space between the foamed, sheathed and papered original roof and the new sheathing. We’re putting a metal roof on. Question is, do we need to vent this space? I don’t believe there is an ice dam issue since the foam under the original sheathing is an air barrier, correct? Are there other issues that are requiring this area to be vented?
Thanks!
GBA Detail Library
A collection of one thousand construction details organized by climate and house part
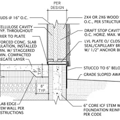
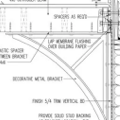
Replies
Mike,
Where are you located? Six inches of open-cell foam is only R-22. That's not much.
It's too bad you didn't shim up the roof with 6 inches of rigid foam instead of empty 2x6 rafters.
In virginia- zone 4.
The SPFA has been telling us that we only need 6" OC in this region for a while now, and the local installers agree. Code officials usually allow it without question.
I thought about shimming it up with foam board but that was way too cost prohibitive.
Thanks for your help.
Mike,
As far as I'm concerned, R-22 doesn't meet code. In case you want to learn more on the issue, here is a link to an article: It’s OK to Skimp On Insulation, Icynene Says.
The code officials allow it as long as we can show a RESCheck report that passes it. It typically does when the right windows and other air sealing are used.
Any ideas on the issue of venting?
Thanks again.
It may pass code under a RESCheck rule, but an R22 center-cavity roof is still prone to ice damming issues, even if perfectly tight.
If the upper roof deck isn't installed yet it's worth putting unfaced R15 "cathedral ceiling" fiberglass or rock wool batts in there, with a vented 2" air gap between the batts & deck, or laying down another 3" of open cell foam, whichever is cheaper.
Without exterior insulation open-cell R22 creates a wintertime moisture hazard for the original roof deck unless you installed an interior vapor retarder between 0.5-1 perms. If you went with interior poly it's a moisture TRAP, but if you leave it open the roof decking may develop issues over time (particularly on the north side.) See:
http://www.buildingscience.com/documents/reports/rr-1001-moisture-safe-unvented-wood-roof-systems
Take special note of the zone 4 locations in Table 3, fourth column, entitled "full depth ocSPF". Since you don't even have the full depth to meet code, you'd be accumulating even MORE moisture in the roof deck than was simulated. Adding the R15 of higher-density fiber above the roof deck would restore a safety margin.
And yes, I am aware that putting in 10.5" of open cell would be preferable to 6", but when you consider the extra cost, that was not an option. The consideration was that we would be better off using 6" of open cell foam (air barrier) rather than R-36 of batts or blown in. This allowed us to seal the attic space and put all mechanicals within conditioned, sealed space.
I agree with the logic of the article- more is better. But the article isn't confronting real world issues- if R-22 of open cell performs satisfactorily under real world test, as it's shown to do, it should meet prescriptive code. It shouldn't be considered "skimping" just because it doesn't meet an arbitrary R-38 number. By your logic, if the code was changed to R-60 tomorrow, I would be "skimping" by only using R-38.
I remember seeing a study a few years ago that showed a cost-benefit analysis on spray foam depths, and it explained that every extra inch past a certain point was only very slightly better on performance. Meaning, 6 inches is not twice as effective as 3 inches and 12 inches is not twice as effective as 6 inches. I can't find it right now, but if my memory serves, it showed 6 inches as having maximum cost-effectiveness.
I think we need to get away from simplistic R-values and use what works, both for the scientist and for the consumer.
Thanks again for your help and your insight.
Dana- thank you for your insight.
The sheathing is already on the second layer. Honestly, I'm really not concerned about the insulation depth. The article given here is again referring to the code, not the actual effectiveness. The SPFA has shown in their studies (supplied by Oak Ridge I believe) that 3.5" of most 1/2 pound oc foams will create the necessary barrier for dew point in our area. In very extreme conditions (below 10 degrees), this system may have slight moisture infiltration, but that very rarely happens in our area. I'm not super concerned about the few times it does.
What I'm really looking for is some insight on the static air versus ventilation issue. Any ideas?
Thanks again.