Vented roof assembly for tiny house

Hi,
I am building a tiny house on a trailer in southeast BC (climate zone 6). I am seeking some advice on how to protect the vented roof assembly from condensation.
The 2×8 rafters span the 8 foot trailer width. They slope only 1/2 in 12, the low slope chosen to maximize headroom in the lofts while keeping within height restrictions. The roof membrane is liquid applied EPDM over plywood sheathing. I’ll have about an inch gap for air flow below the sheathing between continuously vented eaves on either side. I understand that with such a low slope, the stack effect won’t help me much to push air through so I’m relying on wind and pressure differences between the two sides, and I thought the short distance between eaves probably helps too. Because I know this isn’t optimal, I would like to do what I can to guard against condensation on the underside of the sheathing.
My plan is to use Intello smart vapour/air barrier between the ceiling and rafters/insulation and not have any pot lights or unnecessary protrusions through the ceiling, and to carefully air seal those that are necessary. I’m using Havelock Wool batt insulation in the stud/rafter bays. To ensure the ventilated roof gap is maintained, and to avoid air currents through the batt insulation, I thought to use rigid mineral wool boards cut to rafter bay widths and with 1″ thick blocks fastened to the top surface here and there to maintain the space and contain the wool batts below.
(Does that make sense? So from the inside: ceiling (probably t&g ship lap), Intello, 5.5″HavelockWool, 1.25″ Comfortboard, air gap, sheathing, EPDM.)
My questions are about air and bulk water barriers between the insulation and air gap.
– I know it’s not an air barrier, but will the rigid mineral wool work well enough to prevent air currents penetrating my insulation? Or should I use a vapour permeable air barrier membrane between the insulation and air gap, air sealing the insulation from both sides?
– I’ve heard of rigid mineral wool serving as a drainage plain behind a rain screen on a vertical wall, but with the low slope, perhaps an air barrier membrane would also improve bulk water drainage.
– Any recommendations for such a membrane? Just seam-taped house wrap or something more high performance/technical?
– And lastly, is there a benefit to protecting the underside of the wood sheathing from the condensation? Like painting it with a wood sealer? Or will sealing the wood on both sides be worse, since if it does get wet, it won’t be able to dry?
Any input will be much appreciated.
Thank you,
Ari
GBA Detail Library
A collection of one thousand construction details organized by climate and house part
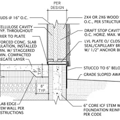
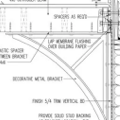
Replies
If you are tight and space, your best bet is an unvented roof.
Since you don't have to build to code, you can choose the insulation levels based on how much space you have.
You can easily span the trailer with 2x4 or 2x6, fill the cavity batts than install enough rigid insulation on the outside for condensation control.
With T&G ceiling, if you go higher on the ratio you can skip the interior air barrier.
For example, if you go with R14 batts, you would need R14 of rigid above (~2.5" of polyiso). I would bump that ratio up to 60% without a proper ceiling.
For such a small space, going nuts on insulation is not worth it. The energy savings is minimal and you just waste interior space. I would guess something around R20 assembly (roof,walls,floor) gets you most of your energy savings without taking up too much space.
Ari,
Considering your roof slope and limited available height, the unvented approach is best. Even if you paint the underside of the roof sheathing, condensation will occur and wet your insulation and rafters, degrading performance. A vented air gap actually cools the roof deck more and would increase risk in the absence of crosswind or a bigger air gap or enough flushing via stack effect.
For the unvented approach, make at least 50% of your thermal resistance air impermeable. Polyiso on top of airtight sheathing or closed cell HFO-blown polyurethane foam on the bottom.
Cheers,
I agree with Akos that going unvented is probably best here. I suggest an unconventional assembly here: frame out your rafters, put a “roof” of 2” polyiso on top with seams taped, then put your plywood roof deck on top of the polyiso. This gives you an air and vapor barrier, and also R13 of continuos insulation all in one. With your plywood outside of the polyiso, you won’t have any issues with your roof membrane.
You can use minimum dimension rafters (minimum being whatever is necassary for structural strength) and put mineral wool (or fiberglass) batts in to add to the R13 of the polyiso. This should give you a pretty robust assembly despite being a bit unconventional.
Bill
Thanks for your replies. I did consider the unvented approach but I decided to do a vented roof because:
1) According to code I needed at least 2x8 rafters to support the snow load for my area and then to apply double this depth again in rigid exterior insulation would take up too much of the limited height, like you said.
2) the friends in town who have done vented roofs in their tiny homes have had better success than those that tried to go unvented and had mould growth in the first few years. I thought since I am a novice builder, it would be safer to go with vented in case I don't get the detailing exactly right, it can dry out.
I have already framed, sheathed, coated and flashed the roof at max height so I don't have the option to add rigid exterior insulation at this point.
I don't think I will be getting any less airflow in the winter than many of the houses in my area with a ridge vent covered in 3 feet of snow. I am anticipating some condensation on the sheathing so that is why I am wondering if I can protect the rafters and insulation with some sort of membrane to shed bulk water.
You could use duravent, which is a purpose-made battle for exactly this purpose. You could also use small furring strips to support 1/2” polyiso acting as a baffle. There are many ways to do it. You want to be careful about sealing the rafters and reducing drying ability though.
Bill
I'm not aware of any means of controlling "bulk water" or meaningfully shedding condensation from the underside of the deck at 1/2":12" slope with a 1" air gap.
That said, your proposed roof is nominal R25. 2" of polyiso and R13 batts would have gotten you about same result, unvented. Even code minimum R value would be R25 rigid foam (about 4 inches of polyiso) plus R25 batt insulation. I'll wager your friend's mold issue resulted from too much batt insulation installed with too little rigid foam above.
I'm not the biggest fan of spray polyurethane foam, but I would honestly propose 2" of closed cell against the plywood deck plus 3 1/2" of the Havelock wool. This would be safer, same R value (or better considering it stays dry), more airtight and thereby more energy efficient.