Vented or Unvented Roof for Hot + Humid Climate 2A

rkarsen
| Posted in Green Building Techniques on
I am an architect working almost exclusively in New Orleans LA. Many of my residential projects would benefit from a cathdral ceiling for architectural desires, or semi-conditioned or conditioned attic to allow the retention of the HVAC equipment being located in the attic (most are installed in conditioned attics which I understand to be a horrible idea). I should start by saying I think Ive read most if not all the articles on this topic on this website + building science, but am hoping to have this thread focus specifically on this climate zone. With the new Fortified Roofing standard which many homeowners are choosing for the insurance benefits, exterior continuous insulation, or venting above the roof sheathing doesn’t seem to be allowed. This leaves the options described in the code, which might be summarized as: vapor diffusion ports, vented roof assembly, or using closed cell foam spray or rigid boards to deal with condensation potential in the rafter cavities. The State Historic Preservation Office typically discourages the use of spray foam. Foam boards are often expensive to fit between rafters on existing historic buildings with a lot of careful sealing required. For the sake of putting this question in context of a specific example, Ive got a 2 story rectangular simple building 24′ wide x 70′ long with a hip roof, 5:12 slope, 2′ overhangs on all sides. New plywood roof sheathing + ice + water shield + asphalt shingle roof is planned and to be installed in compliance with Fortified Standards. This leaves me with weighing these options.
a) open cell spray (air impermeable) insulation in direct contact with underside of the deck and making sure to air seal at the rafter”tails” as they penetrate the exterior wall
b) fiberglass batts in the roof with vapor diffusion port at ridge (everything air sealed)
c) fiberglass batts in the rafters with vented baffles (vented roof) – soffit + ridge vents
so two questions:
– since condensation on the underside of the roof sheathing in winter is still a risk with open cell spray insulation, is there any reason not to include a vapor diffusion port with that insulation approach?
– if not using spray foam, and weighing options b & c above, Id lean towards b since it doesn’t invite hot + humid air into the volume of the building, but not sure if that out weights the benefit of the tried + true approach to ventilation.
Probably too much to ask, but I thought Id give y’all a try!
GBA Detail Library
A collection of one thousand construction details organized by climate and house part
Search and download construction details
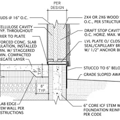
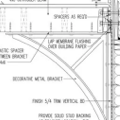
Replies
“ With the new Fortified Roofing standard which many homeowners are choosing for the insurance benefits, exterior continuous insulation, or venting above the roof sheathing doesn’t seem to be allowed.”
This is not my understanding of their certification requirements at all. The only hard part I have found attempting to meet this standard is the outrigger requirements on gable ends that must originate from structural parts of the framing and cannot be purely applied after roof and wall sheathing are up. Not without engineer approved alternatives, at least.
All three of your options are equally bad because they put vapor permeable insulation at the roofline. Don’t do any of those. Either use rigid exterior insulation to keep the sheathing above dew point at all times or use non permeable insulation on the underside of the roof decking like closed-cell spray foam or cut-and-cobble rigid foam.
Thanks for the feedback. On the Fortified + exterior insulation, you may be right but its not clear in their guidelines. They make no reference to the possibility of exterior insulation, and all the diagrams and language regarding the decking show it flush to the framing, and likewise the roofing to sheathing. I can see that this isn't necessarily at odds with the use of two layers of plywood/sheathing (i.e. above and below the exterior rigid insulation boards), but its not clear. I would be happy to learn if its acceptable from anyone who may know.
4.1 - Minimum thickness
4.2 - Nailing pattern
4.3 - (for re-roofs only)
4.4 - Sealed roof deck
4.5 - Drip edge
4.6 - Flashing
4.7 - Roof coverings (>= 2:12 slope)
4.8 - Roof covering (<2:12 slope)
4.9 - Attic vents and covers
4.10 - PV Systems
You say they make no reference to ALLOW exterior insulation and I say they make no reference to DISALLOW exterior insulation. Your sheathing will still attach directly to the framing members, your WRB will still attach directly to the sheathing and your drip edge can attach directly to sheathing over the WRB (detail F-DE-1) under the insulation. The only possible problem you might run into is the "DP" rating of the roofing material. You would need to make sure your assembly meets ASTM D3161 Class F or ASTM D7158 Class H ratings.
If your family honor demands that you put your HVAC in the attic then the vapor port seems like it is worth a try but understand it is a relatively new idea and has no real history.
Option A has a problem in that it has no vapor barrier and moisture is free to move thru the open cells find the cold surface and condense.
Options A, B and C have the problem that the rafter depth is likely to shallow to meet the minimum R value in the limited space. With a truss roof one might only have 3.5 inches of depth.
To my way of thinking installing HVAC equipment in a vented attic is the horrible idea. The conditioned attic full of HVAC equipment is marginally better idea. The smart move is to make a plan that has room in the conditioned space for the HVAC equipment and cover the flat ceiling with R60 of cheap fluffy insulation and vent the empty attic.
Walta
Thanks for the feedback and your comments make perfect sense. Doing your preferred method is a challenge, but still might be the right path. I have an AHU location that works pretty well, but the existing ceiling height in this second story is 8'8", so getting ductwork below that heights starts pushing the ceiling height below 8'0" pending final duct sizing. Id obviously try to find the least compromising locations for that to occur, but not terribly desirable. I do wonder for that reason, if I shouldn't use minisplits. Less attractive, but would resolve this issue, and keep us in budget as the recommended approaches towards attic semi-conditioning (cut + cobble/exterior rigid insulation plus all the air sealing) are probably most expensive options, and yes, my rafters are only 2x6's so its hard to get upto R38 without extending the rafter depth ($$$).