Vent space when using polyiso

My rafters are 2 x 8, I don’t want to use spray foam, and I can’t get a high enough R value using cellulose or fiberglass without furring out the rafters (which we really don’t want to do due to limited headspace), so my plan is to use layers of polyiso between the rafters in the cathedral ceiling in the attic room I am finishing off. There is room for me to leave an air gap of at least an inch between the roof deck and the polyiso so I get a vent channel connecting the ridge vent (above the collar tie) to the soffit (behind the knee wall).
But at one end of this room I have 2 valleys, where the rafter bays dead end at the valley rafter (but open to the ridge vent above). Should I also leave an air space between the roof deck and the foam board in the bays, or is ok to have the foam board in contact with the roof deck without an air gap?
Also, what do you think of putting sill seal along the sides of the rafters, cutting the foam boards a little narrow and using the sill seam to act as a compression device to block airflow. The bay is less than 8 ft long, so I don’t have any cuts in the boards, and I plan to seal the last board with foam.
Thanks,
Rob Silbajoris
GBA Detail Library
A collection of one thousand construction details organized by climate and house part
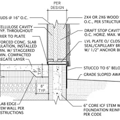
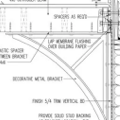
Replies
Rigid foam done well and continuously fails at the thousand feet of seams even for Joe L sometimes.
So what about putting rigid into framing instead of on top continuous? When someone wants to have 20 times the edges of rigid foam to fail, I say good luck with that idea. Two other facts. If you have air leaks, which is almost certain there will be some to start with or over time then two more problems may occur somewhere in your build. Either you lose much of the insulation ability or worse you start trapping moisture that rots the heck out of your structure.
Really? Yes, Much of what I have remodeled over the years where rigid foam was used somehow has has either mold or severe rotted to nonexistent wood structure hidden within. Structural headers holding up an entire second story so rotted that all looked like soil instead of something recognizable.
Saving money.... sounds good to me too... can you? good luck.
Rob,
If you have two valleys, your roof is NOT a good candidate for the creation of a vented insulated roof assembly. If you want to insulate the roof slope, and you have two valleys, you should create an unvented assembly.
The right way to proceed is to either use closed-cell spray foam on the underside of the roof sheathing, or rigid foam on top of the roof sheathing.
The "stack of pancakes" approach -- cutting rigid foam into thin strips and inserting the rectangles between the rafters -- definitely falls into a gray area when it comes to the building code. I think it's hard to make this approach airtight. (Don't try to seal the edges with sill seal -- it won't work. Use caulk or canned spray foam if insulate this way.)
I don't like the approach, but if you do it against my advice -- remember to install at least one layer of rigid foam under the rafters to form a continuous layer that interrupts thermal bridging through the rafters.
I'm trying to make the best of a bad situation here. I forgot to say I'm in region 4. The garage with the room above it that I'm finishing off butts into the main part of the house at a 90 degree angle, thereby creating the 2 opposing valleys where they connect. The main part of the room is about 24 ft x 10 ft and has 16" oc 2 x 8 rafters, forming 18 bays on each side, all of which are vented at top and bottom by the ridge vent and the continuous soffit. The 2 valley rafters meet at the ridge board. The bays that come off these rafters dead end at the rafter, but all are open to ridge vents. These dead end bays run from 5 ft to 5" in length.
There is no way we can afford to take off the roof and put foam sheathing on the outside, so we have to insulate from the inside, without furring down the rafters. I don't want to use closed cell foam because of the potential problem of not being able to tell when the roof has a leak, and I am leery of both closed and open cell foam because of the potential of long term odor/health issues. This room will be used very infrequently as a guest bedroom/grandkids playroom and there's a 25 seer Fujistsu mini-split to take care of heating/cooling as needed.
Given all that, I don't see anyway around using polyiso boards to insulate between the rafters (with a layer of rigid foam under the rafters, then sheetrock). The idea is to use 2 layers of Hunter H-shield polyiso (bonded on each side to fiber reinforced facers.), 4" thick (R25) plus 2" thick (R12.1), which will leave me with a 1 1/4" air gap under the roof deck. The spec sheet says that the moisture vapor transmission is less than 1 perm (57.5ng/(Pa•s•m2)). I realize that I have to seal the boards against the rafters.
Code issues aside, what is the best way to deal with the dead end bays? Construct as I described above, or add another layer of polyiso to fill the entire cavity with no air vent?
Ok or not ok to leave any air gaps at all between the layers of polyiso and should the final piece be flush with the ends of the rafters so that it's in contact with the layer of polyiso under the rafters?
Other than losing R value by not using a layer of foam board below the rafters, what problem(s) would it cause if I did not add this layer?
Other than insulation factors, how does this assembly impact water vapor movement during the different seasons? Should vapor retardant paint be used on the sheetrock?
After reading this over, I think that I have (at least) one flaw in logic. I said that I don't want to use closed cell foam spray because of the potential for undiscovered roof leaks, but then aren't I asking for the same trouble by using polyiso, which is basically closed cell foam?
Rob
Hire an insulation subcontractor. The price is right and liability is theirs. You could have high R batts installed, and a layer of rigid foam then drywall. Have vent space, even though some end at the valley.
Done. Have at it. Good condition shingles and homeowners insurance have your back along with the subcontractors.
How about Spider dense pack fiberglass (R4.2/inch) instead of batts?
Yes Spider, which will supposedly performs much better than batts. Get err done.
See the discussion on Noah's thread:
https://www.greenbuildingadvisor.com/community/forum/general-questions/25516/rigid-foam-attached-underside-rafters-good-idea
You can't just dense-pack Spider up against the roof deck in climate zone 4, and with the thermal bridging of the framing the R4.2/inch is fairly meaningless- it's performance wouldn't be measurably better than R3.6/inch cellulose or R3.5 inch open cell foam. But neither of those solutions would work either.
With thermal bridging of R7 rafters, even a full cavity fill of closed cell foam or cut'n'cobble iso has REMARKABLY little difference in the actual thermal performance of the cavity, despite an R40-ish center cavity R.
With a 1" flash of 2lb foam on the roof deck ANY of the blown/sprayed solutions would work. The notion that cc foam is a problem for finding leaks isn't a very good reason. Closed cell foam PREVENTS leaks- it's waterproof to liquid water (where open cell is not. If you have a localized shingle leak any roof damage is very localized as well, and if it costs you a sheet of OSB at the time of re-roofing do you really care? You're far more likely to run into extensive roof-deck replacement if you DON'T put the closed cell foam at the roof deck, since even small air leaks in a cut'n'cobble iso fill ends up transporting moisture to the roof deck, and the aluminum facers prevent it from drying quickly. A flash-foam air seals the wood from any air currents, and forms a non-wicking condensing surface.
Save the rigid-foam budget for the interior side, and put up 1" of XPS (which is semi-permeable, and allows the assembly to dry, unlike foil-faced iso) as a thermal break against the framing, and delivers far better performance/$ to the assembly than a high-R cavity fill. But don't skip the flash-foam on the roof deck, it's critical.
Thanks Dana. If it matters, the polyiso I was thinking of using does not have foil faces.
Even the fiberglass or asphalted-fiber facers are usually rated under 1 perm, and with 2 layers of rigid board it'll inhibit drying rates. The specs are pretty squishy on those- sometimes <1 perm means 0.5 perms, other times it's closer to 0.8, so at 2 layers you're about half that. the kraft facers on batts tend run ~0.5 it might be ok.
Scrap rates on cut'n'cobbled rigid foam are high. Using reclaimed goods is pretty cheap (cheaper than batts), if you can find a local source.
Thread gone astray....
Dana, no spray foam or cut-n-cobble foam (was....the direction this thread was headed in regard to posted question and needs, yes?).
The build for the seldom used room ... Vent space, then glass either Spider or high R batts, then continuous taped foam, then drywall, then standard paint, done.
cut'n'cobble , "stack of pancakes" "lobster traps"
;) green slang... Not slime... Slang... I like it
Ok AJ, your idea of vent/Spider/foam/drywall appeals to me, but your earlier comment about having good shingles and homeowners insurance makes me think that you think this solution may cause problems in the long run, so I would appreciate it if you shared your concerns. Also, if the foam under the rafters is left out, does that only affect the thermal performance, or would it lead to more nefarious issues?
Leaks in airy construction dry. Leaks in tight construction rot stuff. In my proposal since you do have a ridge vent all should be ok. My other statement is that you have backup too. I think the foam is worth using but yes it may hide leaks somewhat. Valleys love to leak unless I was your roofer. My valleys have double wide double thick protection as melting snow here in valleys leaks in if done the normal roofer style.
I think you'll be fine. Get err done my man.
Rob - As i see it you have two 5' x 5' triangles against the valley rafters where you have limited ventilation out the top but will still have 1" x 14.5" open across the bottom. I thin you have sufficient drying potential there that there is very little risk of humidity and moisture damage esp in a rarely used bonus room over the garage. Spider blown through a scrim against 1" batts will really just give you R-3.6/inch at 6.5" you will get R-23.8
The sill seal is just a suggested way to hold the foam in place and fill the variances in the framing and doesn't replace the need for ventilation above or foam or duct mastic to air-seal at the bottom as I think you understand. The reason to use two layers is so the foam can fit tight on the right on the first pass and fit tight on the left on the second but there really will be little difference with just using a singe thickness of the final r-value so long as you stuff the gap between the wood and foam with something to prevent air flow and hold the foam snug to the drywall at the bottom for the same reason.
Probably the biggest issue is getting a good seal between the drywall and thee foam over the knee wall. If you had space to run even a half inch of foam between the drywall and the rafters it would be great but as it is I think you woud be better served with two layers of three inch foam at R-38 than the spider and less risk of odor than the spray foam. it's a small job so really not worth bringing in a foam truck so it's likely to be cheaper than closed cell spray foam.
You'll probably end up ripping all the 8' x 14.25" strips on a table saw though so it will be very good idea to have a vacuum set up to extract and contain the dust under the saw and set the blade to stop 1/4" shy of the top of the foam to keep tht nasty dust from spraying up in your face. Still wear a good dust mask, poly iso has less flame retardant in it than poly styrene or spray foam but it's dust is still nasty.