Vapor Retarders/Double Air Barriers

May I ask to ensure we haven’t missed anything in thoughts on building our home. I was under the impression we would use Closed Cell Spray foam for the entire assembly, but my husband is now thinking Open Cell for the above grade walls. Will these assemblies work?
Unvented Cathedral Ceiling
Metal Roof/Air Gap/Asphalt Felt/ZIP Roof Sheathing/Closed Cell (still negotiating the amount)/Back Venting/USG Ultra Light Drywall
Vented Unconditioned Ceiling
Metal Roof/Air Gap/Asphalt Felt/ZIP Roof Sheathing/Air Gap/Fiberglass Insulation with Kraft Paper (Kraft needs to be on which side, I get confused where everyone states “warm in winter” side)/DensArmor Drywall
Wall Assembly
Brick Veneer/Rain Screen Gap/ZIP Sheathing/Open Cell Spray Foam/(Vapor Retarder needed?)/DensArmor Drywall
I worry about the Open Cell Spray Foam and the need for a Vapor Retarder in Climate Zone 5. I will not put plastic in the walls, that caused damage in our last home. I am reading up on the Primer that can be applied to the drywall to act as a vapor retarder, so that might be an option.
Any thoughts?
GBA Detail Library
A collection of one thousand construction details organized by climate and house part
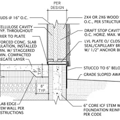
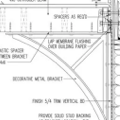
Replies
Where are you at in the design process? Is this new construction or renovation? What's negotiable in terms of the wall assemblies? Are these 2x4 walls? 2x6 walls? Double stud walls?
Why did you settle on these particular wall and roof assemblies? There are probably options that are either cheaper, better for the environment (closed-cell spray foam typically has a really high global warming potential) and/or better performing. But perhaps you have other design criteria that require this approach.
As to your question, in your wall with open cell spray foam, I would think you would want a vapor retarder. A 2-mil nylon like Certainteed Membrain, or a vapor retarder paint. I believe you would also be required to have a vapor retarder by code in this case, so you don't have too much choice about it. Check out R702.7: http://codes.iccsafe.org/app/book/content/2015-I-Codes/2015%20IRC%20HTML/Chapter%207.html
If you are able, it's generally a good idea to use a wall assembly that allows you to use a allows you to use a class III vapor retarder per table R702.7.1
New Construction, 2x6 walls. We decided to go with the Closed Cell in the Cathedral, due to all the research that this might be the best option, and make it unvented. My husband is set on the Cathedral.
I want to ensure the walls or ceilings can dry in at least one direction.
If you don't deal with thermal bridging through the rafters, using very expensive closed cell foam may be a waste of money, as well as environmentally dubious.
If still in the design stage, have you considered raised heel scissor trusses? You can still have the cathedral ceiling, but insulate with cellulose and have a vented roof.
Trusses are up, and the closed cell is being installed this week. Can you recommend anything for thermal bridging, other than exterior insulation?
Are you targeting a code min R-49 roof and R-20 wall? Assuming you can't put exterior insulation on your walls or roof (which would be ideal), here are some ideas you could research further:
In your walls you could do 2" of closed cell foam + 3 1/2" of batt/cellulose. This should alleviate the need for an interior vapor barrier (due to the thickness of the foam) and minimizes the use of the closed cell foam. GBA has some articles regarding the ratio of foam to fluff.
In your ceiling you could do R-20 worth of closed cell foam + R-29 worth of batt/cellulose/whatever. This is still a lot of closed cell foam, but it's better than R-49 worth of foam!!!
The foam to fluff ratios are dependent on your climate zone (5) so that's where I came up with those numbers.
I've read that you can use strips of rigid foam insulation on the inside of your ceiling joists to fur out your ceiling gypsum board and create a thermal break. Maybe give this avenue a bit of research. You could probably do something like run 2x4 crosswise from your joists to reduce thermal bridging somewhat.
Yes, I am beginning to think interior to address the thermal bridging. Starting to research that now. There are so many articles.
Also, does anyone know if any downfalls to Class III Vapor Retarder (latex paint) on the drywall, with the open cell as the insulation?
Insulation on top of the roof sheathing (under metal roof) appears to be another alternative.
https://www.greenbuildingadvisor.com/blogs/dept/musings/how-build-insulated-cathedral-ceiling
Class 3 vapor retarder is fine as long as the sheathing behind it stays warm enough to inhibit condensation.
R49 is IRC code min for US zones 4 & higher, which takes about 8" of closed cell foam. At about $8 per square foot that is VERY expensive and un-green way to deliver the code-minimum, and due to the thermal bridging issues it's lower performance than a fiber between rafters solution or an unvented foam+ fiber solution.
A cheaper and greener way to get there without using fiber insulation would be to mount the steel roofing on purlins through-screwed to the deck with 6" of rigid polyiso. That would be about R36 of insulation, but would still meet code on a U-factor basis due to the low thermal bridging.
An even cheaper even greener way to go is to put rigid foam above, and open cell foam below, as long as it meets the prescriptive ratios of above-deck-R to below-deck R found in Chapter 7 of the IRC. The minimum ratio needed varies by US climate zone, and in zone 5 that number is 40% closed cell foam above, 60% open cell foam or fiber insulation below.
The vented all-fiberglass solution works if you use high-density fiberglass, but suffers in performance if mid or low density goods are used. In US climate zones 5 the kraft facer (if any) faces the ceiling gypsum side, not the air gap.
The IRC code min for walls in zone 5 is 2x6/R20 + R5 continuous insulation, or 2x4/R13 + R10 continuous insulation. The 2x4 + R10 would not need interior vapor retarders other than standard interior latex paint to be moisture resilient, but the 2x6/R20 would need either "vapor barrier latex" or (preferred) a "smart" variable permeance vapor retarder such as 2-mil nylon (eg Certainteed MemBrain). If it's in the budget, the 2x4 solution is best, using 2" of foil-faced polyiso on the exterior of the sheathing, facing the (code required for masonry) 1" air gap, with open cell foam or R13 batts (or 2" of EPS and R15 batts) would be the more resilient code-min solution, but requires longer masonry ties. Some masons will just flat-out refuse to bid on anything with more than 1" of foam, but you need at least R7.5 on the exterior to do it without interior side vapor retarders.
Anybody building in zone 5 can take a lot cues about this sort of stuff from the Mass Save Deep Energy Retrofit Builder Guide, developed by the Building Science Corporation for the state of Massachusetts (all of which is in zone 5.)
https://buildingscience.com/sites/default/files/migrate/pdf/GM_DER_Guide_2013-01-18.pdf