Vapor Open Wall Assembly – Multifamily Project in Zone 4

I am working on a new apartment project in Frederick, Maryland (Zone 4).
The project consists of several four story wood framed buildings (units only on levels 2-4).
We are interested in building above “code minimum” buildings because we are long term holders, want our structures to last, and think it is the wise thing to do.
I am persuaded by the benefits of placing insulation on the outside of the wall (the “perfect wall” as described by Building Science Corporation).
I have recently been looking at using Roxul ComfortBoard IS as an exterior insulation because of its beneficial properties including resistance to fire, resistance to bugs, resistance to water damage, and because it is vapor open.
The wall assembly we are considering would consist of:
Cladding (vinyl or hardie)
1×4 vertical furring strip (ventilated rain screen)
1.5″ Roxul ComfortBoard IS (vapor open)
WRB (Drainwrap or Raindrop, etc…) (vapor open)
OSB (vapor open)
2×6 16″ OC wall with either
Dense Pack or Damp Spray Cellulose (vapor open) or
Roxul Batt (vapor open).
Drywall
Paint
I am uncertain/unclear whether an “additional” vapor control layer (vs air control) is necessary.
I have been referred to “smart” vapor control membranes to be installed behind the drywall.
These products would be “vapor open” in summer when warm moist air might might make its way through the assembly and into the inside of the wall and “Vapor Closed” in winter when warm moist interior air may try to make its way into the assembly to cold(er) sheathing.
1. Do I need an “additional” vapor control layer like the smart membrane or is the totally vapor open wall assembly fine “as-is” assuming I have properly air sealed?
2. Is it a problem that this assembly would not result in the rule of thumb 2/3 of my R-value being outside of my OSB sheathing?
3. Any suggestions on good/affordable method(s) of air sealing this wall assembly?
4. Does anyone see any other issues with this assembly particularly in my climate zone?
Thank you in advance for your help.
Shane Pollin
Comfortboard IS:
http://www.roxul.com/residential/products/roxul+comfortboard+is
Smart Membranes:
Intello:
http://www.foursevenfive.com/images-ezpages/475%20Proclima%20INTELLO%20system%20brochure.pdf
MemBrain:
http://www.certainteed.com/products/insulation/mold-prevention/317391
GBA Detail Library
A collection of one thousand construction details organized by climate and house part
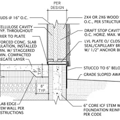
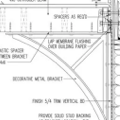
Replies
Shane,
1) No, you don't need an additional vapor control layer.
2) No, not a problem. The 2/3 "rule" was developed for other, colder climate zones.
3) My preferred air-sealing method is the air-tight sheathing approach. There are some good photos of this approach in this presentation - http://www.passivehouse.us/passiveHouse/2010_Passive_House_Conference_Presentations,_November_6_files/Darcy%20Bean-%20Passive%20House%20Conference%202010.pdf and also the article in the Journal of Light Construction (JLC) on Chris Corson's Passive House in Maine (paid access only at this point, I think).
A few other thoughts to add -
A) Vinyl siding effectively acts as "rainscreen" siding. If you go with vinyl you can skip the furring strips
B) Switching from OSB to plywood would lower the risk of moisture-related durability issues.
C) The fancy WRB's (such as DrainWrap) seem like overkill to me in a rainscreen cladding assembly.
I agree with the other posters that vinyl siding provides good ventilation without furring, but it is a real stretch to call a wall clad in vinyl without furring a rainscreen assembly. If you do fur I would use 1"x2" not !" x4" to maximize the size of the cavities and drying.
Shane,
Yes, Maryland has a tricky (mixed humid) climate. And I agree with John that the 2/3 rule doesn't strictly apply in a mixed climate - however in the winter it does get sufficiently cold that it is recommended to reduce the outward vapor drive on the warm side in that season - INTELLO would be a good idea (which is part of the Pro Clima enclosure products that I import), but plywood should work well as well, and OSB to a certain extent - any of these three airtight materials should be taped air-tightly on the interior side of the bulk of your insulation.
You will still need a weather resistive barrier - keep the water out of you sheathing/insulation. I recommend to put the WRB (solitex mento) on the exterior - so your mineral wool insulation is also protected against windwashing/thermal bypass. Some ideas for assemblies can be found in one of our recent blogposts
Trevor, When you refer to CIS, is that a Roxul product? Do you have the full name for the abbreviation?
Thanks
Using 1x2 furring will be more difficult to make flat and is far more prone to splitting. Go with 1x4 and save yourself the misery. The effect of wider furring on drying rates is truly miniscule, "in the statisical noise", given the very high vapor permeance of high-density rock wool.
Use 2x furring if you want it to look as flat as possible with vinyl. Getting it pretty flat with 1x furring using panelized fiber cement isn't as much an issue. Fastener retention can sometimes be a problem for heavier siding with only 3/4" of wood to bite into, but ring shank nails can work. (Pay attention to the metal compatibility specs for any fiber cement product though.)
In this stackup the OSB is still a Class-III vapor retarder, as is the interior paint. It's unlikely that the OSB will ever drop below the dew-point of the outside air in summer in an air conditioned house MD, but the gypsum almost SURELY will at times, but not for extended periods. Making the OSB layer as air-tight as possible and using cellulose for cavity fill rather than Roxul would mitigate summertime mold or blistering interior paint cropping up after torrid weeks when outdoor dew points hit the high-70s.
Aaron - I just realized that the product I referred to is not commercially available - I should not have mentioned it
Shane,
I have been researching a similar assembly and I have a few thoughts for you.
1) if you go with vinyl siding, no furring strips are required for ventilation. You will still need a strategy for attaching the rockwool, but screws with plastic washers will work.
2) OSB is not nearly as vapor-open under high humidity as plywood. Another cost hit, but if you are counting on drying through the sheathing, and thinking long-term, plywood may be worth it.
3) More exterior insulation would definitely be better. I am a believer in the Perfect Wall approach, especially in high risk applications, but it's probably overkill in your situation. As designed, you will be counting on your air barrier to minimize interstitial condensation, but a properly detailed air barrier (such as air tight drywall) can definitely work - as long as tenants don't knock holes in it.
4) If the air barrier is done well, then a vapor barrier primer will be sufficient to control vapour flow.
5) Make sure you address humidity control in winter. Proper ventilation that can not be shut down by tenants is good insurance against interstitial condensation.
Trevor
If you go with hardie, then the 1x4 strapping is good. We found that putting the capped nails 16" on center over the studs helped prop out the strapping at a consistent 2" (our roxul comfortboard IS thickness) and maintain an even plane to prevent wavy siding. Also it helped mark the studs to get a good bite when attaching strapping. See our blog for details http://agreenhearth.com/stone-wool-to-warm-the-heart-and-the-home/. We're using vapour retarder paint and airtight drywall but are in coastal BC
Thanks for the great responses. Patrick, can you share your window detail? Thanks