Vapor Flow in Light Frame Construction

I would like to hear comments from Scientists and “Others”
I am an Other, an Architect…not a Scientist
I am very interested in designing Low Energy Homes.
I am fascinated with Passivhaus and European Construction.
I have noticed the “Euros” usually do not use foam (spray, sheets or blocks)
They tend NOT to use membranes, peel and stick etc.
Here is an example wall mock up.
http://live.pege.org/2006-building-salzburg/passive-house-wall.htm
The most common type wall has an OSB type air barrier on the interior side of the structural wall
The “OSB” is air barrier (they call it air-tightness layer)and racking board (shear panel)combined
The gypsum board is always furred out about 2 inches inside of the racking board.
This creates a “service space” for all the wiring and avoids penetrations in the air barrier.
It also protects the air barrier from the occupants (hanging pictures etc)
Sometimes they insulate the “service space” sometimes not.
The outer skin of the structural wall they call sarking board.
It is a panel usually with tongue and groove or lap joints all around.
Many times the joint is not taped … but it appears to be reasonably airtight.
I assume that the outer face of the panel may be coated with a water shedding coating.
The panels seem to be very vapor open.
The panels seem to have High R-value.
Sometimes the outer skin looks to be gypsum board.
They do NOT usually use house wrap or felt.
They always use furring strips before attaching siding.
The siding seems to be always REAL wood not fiber-cement or vinyl or waswood.
The walls are very Thick with high R-value
The cavity insulation appears to be cellulose or rock-wool
At first glance this all seems very complicated and labor intensive.
The walls are very airtight yet rather vapor open.
My current thinking is that these guys are “ahead of us” and are on a better track.
Most of our(North America) “High Performance” Walls rely on foam products and are not as vapor open as these Euro-walls.
Our walls are starting to be just as complex and labor intensive as the Euro-walls yet less forgiving.
One thing the Euros seem to do to offset some of this complication is that they panelize offsite.
Here is a short video with a lot of fascinating details that they do in a different way.
One thing I noticed is they do not always “break” their sheet goods over the studs or rafters.
https://www.youtube.com/watch?v=wBQHBr7zn0M&feature=related
I have also noticed that when the “Euros” use Foam it looks to be always a vapor open foam.
My question:
Is it really important for Vapor to flow thru?
Or is it enough for it to flow in both directions?
GBA Detail Library
A collection of one thousand construction details organized by climate and house part
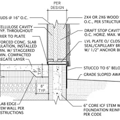
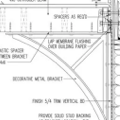
Replies
If water vapor can flow in both directions, then water vapor can flow through, unless there is a mid-line vapor barrier.
The fallacy of the "hermetically-sealed" thermal envelope is that is assumes perfection over the life of the structure. If there is ever a leak, from the inside or the outside, then the envelope needs to breathe to release that moisture. And, if it can breathe in both directions, it's going to be more durable.
I'm glad to see that PH attempts to make their envelopes breatheable, as that is a fundamental of that other German innovation: Bau Biologie.
Robert,
It is exactly the mid-line vapor barrier that confuses me.
BSC seems to think it is not a problem.
You and many Europeans seem to think it is a CONCERN.
If you're refering to peel&stick membrane on the outside of OSB sheathing or roof decking, I believe that's trouble waiting to happen. In many cases where water has leaked behind bituthene on OSB, the OSB has molded or rotted.
Robert,
I am talking about the Peel & Stick
and also the foil faced polyiso that seems so popular on the Building America Projects.
Caveat Emptor.
What function is a vapour barrier supposed to provide ? Is it necessary in all US climates ?
Dear interested,
The only location where building codes require vapor barriers is under concrete slabs.
For walls and roofs, building codes do not require vapor barriers. However, some building codes require vapor retarders.
The purpose of a vapor retarder is to slow down the transfer of water vapor.
Regarding the use of vapor barriers on the warm side of walls and ceilings with attics above.....
I am an architect who has for 50 plus years specified vapor barriers as described above. I have just designed a house to be built on the Maine coast and have detailed the walls etc with a 6 mil polyethylene vapor barrier on the warm side of studs, rafters and floor joists at unheated but ventilated attic. Some builders there are not including vapor barriers and are siting horror stories attributed to their use.
I have spoken with two engineers in Maine with substantial building experience who absolutely recommend the use of vapor barriers on the warm side of walls and rafters....
I suspect that the horror stories may not have all the contributing factors and are just blaming the V.B.s....
I would like to lay this argument to rest.... Any comments?
Don,
I'm afraid you and your consultants are 30 years behind the times. Building Science has accepted that true vapor barriers, such as polyethylene or foil films, are necessary (if at all) only in extremely cold climates (zones 7-8).
Their original purpose in code was to control vapor diffusion and air flow through low-density fibrous insulations such as fiberglass. But it's long been evident that up to 99% of moisture intrusion into the thermal envelope from the interior environment in a cold-climate house is from exfiltration of air, not water vapor diffusion. So the emphasis today is on a continuous and contiguous air barrier and air sealing at all penetrations.
The codes have been revised to require only "vapor diffusion retarders", which means any material or coating with a perm of 1 or less, such as vapor retarder latex primer on drywall. And controlling interior relative humidity during the heating season, by source removal and mechanical ventilation, is more important than reducing vapor diffusion.
Particularly with the increased use of exterior vapor-restrictive layers, such as rigid foam, it is important that every part of the thermal envelope can at least dry in one direction, though drying in both directions is preferable for durability (since the moisture drive direction changes sometimes daily and always seasonally).
The most energy-efficient and durable thermal envelopes will be very air-tight but vapor open. Any vapor impermeable layer, such as polyethylene sheeting, will completely restrict drying and could be the cause of moisture problems and structural damage. If a cold-climate house is air-conditioned in the summer, then an interior vapor barrier will be on the wrong side and become a condensation plane.
Other than in sub-arctic climates, the only place a true vapor barrier is required is under the slab.
Robert Riversong... Thanks for your considered response to my inquiry... The project I am working on is in a zone of 7,500 to 8,000 heating degree days.... Exfiltration of air carries with it moisture vapor and preventing the entry of as much possible into the wall cavity is still to be desired...so why not a barrier with as little permeance as possible?
As little air permeance, yes. The Air Barrier Association of America uses unpainted ½" drywall as the standard against which all other air barrier materials must be measured. If your walls and ceilings are as air impermeable as gypsum board (with all seams and penetrations sealed, including wall plate to deck seams, no can lights, etc), then interior moisture will not become a condensation threat in the envelope.
Vapor permeance is simply a non-issue in a well-ventilated house (winter RH ≤ 40%) in terms of interior moisture causing condensation within the thermal envelope. However, vapor impermeance is an issue in terms of a thermal envelope's ability to dry if it gains moisture from any source, including exterior cladding or flashing penetration (most common), solar-driven vapor, ice dams, mechanical leaks, etc.
A warm-side vapor barrier, in other words, will do little to prevent envelope moisture problems but may do a great deal to extend and exacerbate them should they occur from any source or any direction.
When the external temperature is below 32F, the water vapor diffusing outwards will, at some position close to the envelope, reach the point at which it freezes. How is damage from ice formation prevented, or is it a minor effect which can be ignored ?
Dear Interested,
There are several ways that designers prevent wall damage from the phenomenon you are describing.
1. The most important approach is to include an air barrier. Stopping air flow through walls and ceilings goes a long way toward solving this problem, since most of the moisture that migrates from the interior into wall and ceiling cavities accompanies exfiltrating air. Vapor diffusion is a very minor source in comparison to moisture piggybacking on air.
2. A second approach is to include thick exterior foam sheathing. This raises the temperature of the wall sheathing. If the sheathing is warm, moisture can't condense on it.
3. The traditional approach — 2x6 walls filled with fiberglass batts — can work (I hate to write this) as long as the wall has sufficient drying potential. There are thousands of homes built like this in Vermont. Every winter, a little ice builds up on the sheathing. Every spring and summer, the ice melts and the moisture evaporates. As long as these walls can dry out during the summer — usually by drying to the exterior, but also (in homes without interior polyethylene) by drying to the interior — there is usually no damage. You see, the sheathing is moist during the winter — but the saving grace is, as long as the sheathing is cold, it can't rot. Once the sheathing gets warm enough to rot, it usually dries out.
This last strategy is risky. If the wall is leaky or the house is very humid, you can have a mess. So I don't recommend it.
Dear Martin and Robert,
Thank you for taking the time to explain the ins and outs (sorry about that) of vapor flow. Then only remaining question I have is, what sort of material prevents the flow of gaseous air and permits the flow of gaseous water?
Dear Interested,
1. Unpainted drywall.
2. Asphalt felt (except, of course, at the joints).
3. Tyvek, Typar, etc.
4. Many other similar materials.
Interested Onlooker,
You might think that anything that would stop an O2 or N molecule would surely stop an H2O molecule, but it's not simply the size of the particles.
The primary difference is in the driving force. Air moves by pressure differentials. A blower door tests a house for leaks at 75 pascals of pressure difference, which is the equivalent of a 30 mph wind on all house surfaces simultaneously. In normal winter operation, a house might experience a 5 pascal pressure due to the stack effect, which is just 1/10 pound per square foot pressure.
On the other hand, water vapor diffuses by vapor pressure differential. With the indoor air at 68° and 40% relative humidity, and the outside air at 30° and 90% relative humidity, the vapor pressure differential is 425 pascals, more than 85 times as much driving force as experienced by the air. If the indoor humidity rises to 50% at the same outside conditions, the vapor pressure increases by 55% to 660 pascals.
So, a material like conventional drywall can easily stop air flow, even with a 30 mph wind, while being unable to resist water vapor flow very well at nearly 6 times the pressure. That's also how a Goretex jacket can keep the wind and rain out while letting your insensible perspiration (water vapor) diffuse to the outside.
In addition, water moves by capillary suction due to its extraordinarily high surface tension (with pressures 1,000 times as much as diffusion pressures), and by osmotic pressure (with pressures 10,000 times as much as diffusion pressures).
Robert,
I am going to bookmark your last post.
I suggest that your comments deserve a grey box with a dark border.(at the least)
perhaps a green box ;-).... with a disclaimer
Robert
If a wall has a vapor barrier (foil faced polyiso for example) somewhere in its assembly of layers, then it cannot sense the difference between the inside and outside humidity levels. No sensible difference, no vapor drive, correct? Would this not be a good thing?
Garth,
It's not that a vapor impermeable wall cannot "sense" a vapor pressure differential, but it can resist nearly any realistic differential - just as an immovable object feels but doesn't respond to an inertial force.
But, as we should all know by now, vapor diffusion (at least from inside to out) is not a significant problem unless you're living in a greenhouse at 100% relative humidity (which is why I advise against attached greenhouses). With reservoir claddings, such as stucco or brick, solar-driven vapor drive from outside to in can be significant, which is why a drainage space and moderate perm weather barrier (like felt or kraft) is important.
The most significant moisture transport mechanisms, by far, are bulk movement, adsorption and surface diffusion, and capillary transport (ignoring the most destructive osmotic pressures caused by efflorescence and salt deposits in masonry).
Murphy's Law states that all building envelopes will leak at some time (or many times) in their lives. Since liquid water migration is the most powerful and destructive, it's just as important to allow a thermal envelope to be able to dry as it is to (attempt to) keep it from getting wet. And drying occurs mostly by vapor diffusion - the weakest force - and surface evaporation. So we are wise to make it as easy as possible to dry.
Thus, any impermeable layer anywhere within or on either side of a thermal envelope will substantially reduce the drying potential and increase its susceptibility to moisture damage. The common compromise is to leave one side of the thermal envelope vapor-open. My "belt-and-suspenders" approach is to leave both sides vapor-open. And then I add a safety pin to the belt and suspenders by using hygroscopic materials that can safely store (buffer) excess moisture and release it diurnally or seasonally.
Robert
You are indeed a good teacher...wish I was close enough to attend one of your classes.
I do want to bring up one more issue. There is a big difference between your philosophy of allowing drying to both sides and using hygroscopic materials, and the BSC approach preached by Lstiburek and Straube. They argue that it is dangerous to have hygroscopic materials on the outside of a building where they will adsorb a large amount of moisture over the winter season when RH is very high even though the absolute humidity is quite low. Come spring and early summer, the race is on to get these materials dry before the bugs go to work on them. This is especially troublesome on the north face as there is very little energy exchange to drive the moisture transfer. Lstiburek argues that this problem is made worse when there is no airflow or convection between or behind the siding and where cellulose insulation is used.
I am sure you have read Joe's BSC Insight #028 "Energy Flow Across Enclosures"
Looking forward to your "Insights".
Garth,
I'm not advocating using hygroscopic materials to buffer the relative humidity of the earth (or even the microclimate around a house), but to buffer the changes of the interior environment just as we use thermal mass on the interior to buffer thermal variations.
The best interior moisture-buffering materials are end-grain wood (such as in cordwood masonry) and earthen materials (such as clay plasters), though large timbers, cellular concrete, unpainted plaster or masonry, cellulose insulation and gypsum drywall also function in this capacity. What's required is a good balance of diffusivity, absorptivity and water capacity so that, like with the diurnal heat coefficient of thermal mass, it's qualities allow diurnal absorption and desorption of moisture.
Lstiburek, et al, have no truck with reservoir-clad buildings which have stood for centuries. Their concern is for energy retrofits of those old classics or building new with unventilated reservoir claddings that aren't hydraulically separated from the structure and thermal envelope.
I see lots of claims, statements and explanations. Where are the references to the research?
Peter,
I was thinking of dragging this old post out and hoping that Dr Feist might offer some Insight from Germany.
Peter, can you be more specific with your question?
I simply want references to research rather than stated explanations and opinions. It's like the geothermal issue; everyone has opinions, but where is the hard cold unbiased peer-reviewed research?
The original link to the "Euro" wall was just one example and with no research references to back it up. And what about climate? which climate was it intended for?
And on that page are multiple other examples of walls. Which, if any, are really "best" practice? Where is the research to prove it?
We really need to try to be objective.
Actually, it's time we cease being "objective" - that is, stop building objects of habitation for human objects.
It is way past time, in fact, for us to come back to our senses (as the saying goes), and trust our intuitions and our direct sensory experience of the world.
Every global crisis we now face is, in large measure, a result of "objective" or "scientific" or "economic" thinking.
"Lose your mind - find your way" is inscribed in a Torii gate I built to help people return to their senses through direct sensory communion with the living world which birthed us and which is struggling to sustain us - against the onslaught of "objective" thinking.
John - I'd like to echo Peter's note, perhaps even give it a twist . . .
Your question is at the heart of what I'm trying to understand about the different techniques. Each has its own risks. Neither is without compromise. But which is more appropriate? (I'm quite sure it starts with, "It depends . . .")
"We" started building superinsulated houses in the '70s. At the time, most (I believe) were insulated with dense packed cellulose and incorporated an interior vapor barrier. Some used exterior insulation to help increase wall R-Value. In time it seems we've gotten away from the vapor barrier and concentrated on the air barrier.
So, we have a stock of buildings in this country that are >30 years old, yet can you find much in the way of a detailed study showing which system has weathered those years better?
Or to put your question another way, which building is more durable? At least, I think that's where you were headed when you stated that the "peel and stick" walls were less forgiving . . .
Robert makes some convincing arguments against hermetically sealed enclosures and exterior foam wall insulation (both from a quality of life perspective AND drying potential). John Straube makes some convincing arguments against double-stud walls that don't incorporate some sort of exterior insulation.
I know the answer is not so simple or easy as "This one is right, this one is wrong."
But to echo Peter again, where's the data? Has anyone inspected a large number of these '70s houses to see? Where are the studies?
Maybe we should post a new question. These older posts don't get any traffic.
Possible Titles:
Double-Stud wall vs. Exterior Foam insulation. Which is more durable?
Are Passivhaus Walls Durable?
Exterior foam insulation: Is it a 50 year solution? 100 years?
What do you think? There are definitely two camps. They arrive at the same place through different paths. They have more in common than they know. I don't want to create further divisions (or offend anyone). But this really could use some more air . . .
I am dragging out this old "EURO- thread" because lately we have had some very good comments, questions and links coming from the other side of the Atlantic.
I am still trying to become more familiar with the units and the Jargon from the other side.
Comments are always welcome from both sides.
i'm confused about the thinking that passivhaus/minergie etc. don't use peel and stick? those guys adore tapes...
also, a number of passivhaus projects use fiber cement boards (swiss pearl, fibreC to name a few) but w/ a rainscreen you could theoretically use anything from OSB or plywood to corten.
there are some really slick wall assemblies that utilize fiber board and rockwool in an exterior foam-like manner exterior. (similar to REMOTE, but not as thick and less embodied energy)
the furring strips work on both sides. on the exterior - rear ventilated rainscreen, an elegant solution for rain shedding assemblies. the assemblies we used incorporated 2 layers of battens (vertical and horizontal) for increased air movement and more room to plumb the rainscreen.
the interior furring serves a couple functions:
1. won't penetrate air barrier
2. provides chase for electrical
3. shim a wall to normal
4. provide additional insulation to whole wall assembly