Vapor Diffusion Through Open Cell Foam on Cathedral Ceiling

I’m having a tremendous amount of trouble understanding how vapor permeability and air impermeability interact in terms of moisture issues caused by open cell spray foam in a cathedral ceiling, and what to do about it.
I have a mono-slope, 2:12 roof with 70% lacking attic. It’s essentially one big cathedral ceiling. Very simple. One penetration from the wood stove pipe on the high side, and one penetration for a bathroom skylight (don’t tell Martin). The walls are ICF.
Standing seam roof, ice and water membrane, OSB roof deck, and then 10″ of open cell spray foam applied directly under the deck for ~R-38 in my climate zone 3A. Image attached.
Now, I understand there have been moisture issues observed with this kind of assembly (many articles here and elsewhere). The moist indoor air rises up and encounters the open cell foam. The foam is air impermeable, so the air stops rising up through it, but it seems that the *vapor* is effectively dropped off at that point of impermeability and continues to spread throughout the foam (from moister areas of the foam to drier areas of the foam, I believe?).
1. Am I correct in my understanding of how vapor permeability and air impermeability interact? Essentially the air stops but the moisture stays in the foam and continues to find equilibrium with the surrounding foam?
2. Is there any reason that a proper HVAC keeping the house at ~50% RH wouldn’t prevent this from becoming an issue? Are these moisture issues always because the interior air is just allowed to get too moist?
3. I’ve seen suggestions for something like a MemBrain vapor retarder between the ceiling finish (if it’s tongue and groove) or using drywall with latex paint as vapor retarder between the interior moisture and the open cell foam. This seems to make sense if we’re trying to prevent moisture from entering the open cell foam — but again, if that air is being conditioned and interior humidity is kept at a proper level, does it actually matter?
4. In my example, the roof sheathing cannot dry to the exterior due to the I&W and metal. Would open cell be *safer* if interior humidity is well managed, by allowing the roof sheathing to dry to the interior (essentially, the moisture would be drawn out of the open cell into the drier air below)?
5. Are there any better strategies for this kind of roof? Like everyone, I’ve read the horror stories about any spray foam potentially failing and off-gassing forever. I figure if millions of homes have been sprayed, these are definitely outliers — but perhaps I should be considering other things as long as they are similar on the budget.
Thank you all for any help in increasing my understanding of the realities of this kind of assembly. I’m trying my hardest to not use closed cell spray foam given the environmental impact and cost, so I’m attempting to understand and solve for the potential problems with open cell instead of giving in.
GBA Detail Library
A collection of one thousand construction details organized by climate and house part
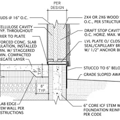
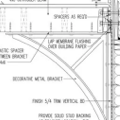
Replies
What you are missing is that humidity rises. My home (crawl area) is kept at 48% RH or below, as you go to the living area, it is 50% RH, and as you get into the attic, at the peak of the late afternoon, attic RH near the ridge can reach over 60% RH.
The way to deal with it is either closed cell foam (bad for the environment, expensive and risky) or a vapor diffusion port (99% of the roofers out there have no idea what it is...)
Thanks for the reply. If I have HVAC supply in the attic and a clear return path for that air, as well as supply vents higher up in the house, I wonder if this would be enough to limit the stratification there.
This is a good summary:
https://www.energyvanguard.com/blog/will-open-cell-spray-foam-insulation-really-rot-your-roof/
Sounds like you have the conditioned part sorted. The only thing to watch is with light color roofing as it can cool the sheathing enough to create issues. If you are going with low SRI roofing, an inch or so layer of close cell SPF before the 10" of open cell foam will protect the sheathing.
Thank you Akos! When you say "low SRI" that means hot roofing. It'll be a matte black metal roof, so definitely low SRI. Did you mean high SRI, as in line with your comment about "light color roofing"?
Yup, got it backwards. Meant to say high SRI.
Great. I should be good then!
Why do you think closed cell has a worse environmental impact than open cell? They both use “green” blowing agents nowadays. You’re probably fine by conditioning the attic and controlling interior humidity, which should take care of damp sheathing during the cooling months but why not spray 1” of cc foam first and you can do whatever you want to achieve the remaining r value without any concern damp sheathing. I’m pretty sure you can make an argument for way less environmental impact of 1” of cc foam and 9” of batts vs 10” of oc foam.
There is more to the climate impact of foam than the blowing agents; the resin and other chemicals used for the solid portions of the foam also have significant embodied carbon emissions. Open cell foam is around 1/2 pcf whereas closed-cell foam is around 2 pcf, so four times the mass for only 50% higher R-values.
Open-cell foam uses water as a blowing agent, but even the best closed-cell foams have an HFO blowing agent with a global warming potential of 1-2, which is not benign, that just means that it's comparable to CO2. And new evidence shows that HFO combines with other compounds in the atmosphere to potentially be more damaging than legacy HFC-blown foam.
Michael's take on this has been a fairly big driver in my decision. One of the local guys also sprays the new "Sucraseal" Open Cell from Enverge. I don't know how much of it is "greenwashing" the problem, but I'm all for increased awareness and solutions on that side of the equation.
That Sucraseal has 17% biomass and doesn't require an intumescent coating. Batts are hardly a panacea of environmentalism either, so just trying to weigh all of this and do my best.
I also just like the idea that the roof decking can dry to the interior. Sandwiching the deck between ice and water and closed cell just seems strange, even though apparently it's fine.
You wrote:
"Am I correct in my understanding of how vapor permeability and air impermeability interact? Essentially the air stops but the moisture stays in the foam and continues to find equilibrium with the surrounding foam?"
I think you need to figure out what the "first condensing surface of interest" is ...
To just say "moisture stays in the foam" seems a little too vague - is the moisture vapor or liquid or frozen liquid (ice)?
Where will the "dew point location" be in this assembly under different conditions (humidity/temperature)?
https://buildingscience.com/documents/insights/bsi-049-confusion-about-diffusion
Fantastic reply and article. Thank you.
Here's where I get stuck. Let's say I have 10" of Open Cell foam against my roof sheathing, which is R-38. Open Cell is "vapor impermeable" at ~3.5". All of the foam is inside the conditioned envelope, attic included.
It's 25 degrees outside (the average low for my location in January). I have the heat running at 72 degrees. Heat rises, so I'm guessing it's more like 73 or 74 degrees right against the start of the open cell foam.
I take a hot shower and don't run the bathroom fan. That hot, moist air rises up to the open cell. Air starts moving through the first inch of foam, then the second, then the third, and somewhere around the fourth inch it has slowed down sufficiently to effectively stop.
Now, at that point, if within that 4" of foam the temperature is still above the dew point, is it true that no moisture will be dropped into the assembly?
If instead it's -10 degrees outside and that cold has spread deeper from the outside into foam, say 7-8" deep, then it's likely the temperature within that first 4" of foam will have dropped below the dew point and moisture will be deposited into the foam. At that point that moisture will continue moving from warmer to colder (open cell is vapor open) and eventually wind up at the roof deck sheathing, the coldest surface, and condense.
Is this accurate?
There are two was to deal with this issue...
1. Control the inside relative humidity
2. Control the first condensing surface of interest
In my post about what I did at my own home, you can see that I felt more comfortable controlling the first condensing surface of interest
former spray foam contractor ...
This is what I did in my own house Climate zone 6 in NH
2.5" of EPS on top of "hot roof" (~ R10)
3.25" closed cell spray foam underside of roof (~ R20)
5.5" open cell spray foam onto closed cell (~R20)
Over 50% of my R-value is closed cell foam which controls the first condensing surface of interest - any vapor that comes in contact with that surface will never reach the dew point ...
Yeah, you've done the impermeable sandwich that I'm thinking about as well. In CZ 3A on-roof insulation is incredibly rare, so I'd be looking at something like 2" closed cell (R13) followed by 7" of open cell (R26) to reach/exceed the recommended R38. That's if I go the closed cell route.
Otherwise it's just a straight 10" of open cell. I'm weighing the cost and environmental impact of closed cell vs. the "risks" of open cell, and what I'm hoping to determine here is whether or not those risks are manageable with my design.
The piece of this I'm still missing is whether or not the 3.5" air impermeability feature of open cell foam means that, as long as the temperature of that air hasn't gone below the dew point by the time it's 3.5" into the foam, it won't create condensation.
It seems a little too black and white for how these kinds of things function. But I would feel much more comfortable going with the low GWP benefit of open cell if I have a grasp on how the vapor permeability and air impermeability interact with regard to dew point and condensation.