Vapor Barrier for Double Stud Wall with Batts

I am considering some alternatives to dense packed cellulose for a double stud wall assembly in case I have issues finding a competent contractor. I am looking at a DIY friendly approach. I know batt insulation has been proposed on GBA in the past, but I have a specific question about using a kraft faced HD fiberglass batt as a mid-wall vapor barrier.
The wall assembly from the outside in:
1) Vinyl siding
2) Fully adhered or fluid applied air tight/vapor open WRB
3) 1/2″ Plywood
4) 2×4 stud wall (load bearing) with kraft faced HD fiberglass batts (R15)
5) R15 Rockwool in 3.5″ cavity
6) 2×4 stud wall with R15 Rockwool
7) 1/2″ Drywall with latex paint
I am trying to avoid using Intello or other sheet goods. My thought is other than a hose bib or too and outdoor lighting there should be few penetrations to worry about in the exterior wall. The WRB would be the air barrier. And R15 should be enough to avoid condensation at the inner surface of the outer wall in Zone 5.
Thoughts?
GBA Detail Library
A collection of one thousand construction details organized by climate and house part
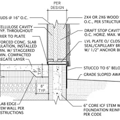
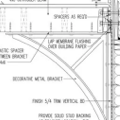
Replies
Kraft paper is something of an old-school vapor RETARDER (not BARRIER), but what are you trying to achieve here? I would think it would be easier to use something like Intello or MemBrain on the interior face of the wall and dense pack the cavities than it would be to try to install batts in the middle of the wall.
Note also that the R value alone isn't the only thing you need to consider when thinking about condensation issues. Moisture can migrate through most types of insulation, which is why a seperate vapor barrier or vapor retarder is usually recommended.
If I were building this wall, using batts, I'd use all the same type of batts and use a smart vapor retarder on the interior. I suspect this would be less labor, since it would be easiest to install the vapor retarder on a continuos surface where you wouldn't have all the rest of the wall structure in the way as you would if trying to work in the middle of the wall. Trying to install any type of vapor barrier before framing is done is asking for trouble too -- none of the materials are strong enough to avoid getting punctured by the end of a 2x4 or a framing nail.
Bill
I agree with Bill. I have a few additional opinions...
-You could detail the Membrain/intello as your air barrier as well as the vapor retarder. Then you could use Tyvek or other more affordable housewraps outside of the plywood sheathing. Fluid applied or self adhered is going to be much more costly and I don't think there is a practical gain in performance (assuming you have a midwall air barrier/vapor retarder. Membrain is flimsy but in this case free from penetrations and densepack it would work well.
-R13 unfaced fiberglass should be available in rolls and batts. I think it would be cheaper and easier to use that, especially in the airspace between the walls. Mineral wool is great, but here it costs about $.30/sq ft more than fiberglass.
-Between the housewrap, membrain, and fiberglass I think you could save at least $1.00 sq ft on the assembly
-On my remodel project I flirt back and forth between the doublestud airspace with membrain and batts/rolls OR using faced EPS/polyiso and taping the seams. If it's faced EPS or foil faced polyiso it can be detailed as the air and vapor barrier, and recoup some cavity depth. I hunt craigslist constantly for a deal on rigid foam that would make it worth it.
Good luck
Brandon
ADA (airtight drywall) is harder to detail in my opinion than MemBrain or the like. The advantage of a film interior air barrier is you get it in place with all joints sealed before the drywall. Airtight electrical boxes are available for ease of warm side installation of the air barrier. When the drywall installers come to the site the hanging of the drywall is a typical procedure. Trying to gasket all of the connection points for ADA in advance and relying on drywall installers as part of the performance team is a leap of faith. Here is one more important consideration on using ADA. Construction lumber shrinks as it ages in the wall, 5 1/2" becomes 5 3/8" over time. I have been in many walls over the years and this is reality. If the ADA gasket material was a caulk of some type, all of those connections can be subject to leakage as the house ages. If a film is used as the air barrier and is sealed to the framing or joints taped, the shrinkage of framing lumber will not affect the building performance.
I would really wait to see what your options are for dense pack cellulose. The option you described seems so laborious and inferior that it should be an absolute last resort rather than a back up plan.
Unlike Fiberglass or Mineral Wool, Cellulose can really help preserve the sheathing in a double stud wall. Also, when applied at proper density (3.6 psf+) it limits air movement much more than a high density batt (2.3-ish density). Cellulose is really inexpensive and shouldn't cost too much to blow in. Installing batts is laborious, itchy, frustrating work. Great care will be needed to achieve a Class I install with batts. Its almost guaranteed with a dense pack cellulose install.
Your thinking is heading in the right direction. I'm an old retired gummer who has designed, built, and lived in (for more than 26 years) several super insulated homes. One of these had
the wall you are proposing - I lived in it about 13 years - in the 1978 to 91 range - in Flagstaff,
Az. (zone 6 at approx. 7000 feet) - a very dry climate. It works well in a very dry climate. By the time I built the next one I realized that it would probably not be so good in other climates.
Here is the better way: works well in nearly every climate, costs about the same, is easer to
construct, but you have to adjust the foam thickness for your zone. For your zone the wall (
from the outside in:
1) Vinyl siding
2) WRB of your choice
3) 1/2″ Plywood
4) 2×6 stud wall (load bearing) with mineral wool insulation
5) 1 or 2 inch foil faced polyiso attached to interior stud face ( all seams taped)
6( 2x4 stud wall not load bearing with fiberglass insulation
Here is the logic: The total wall thickness will be the same + or - !/2", the whole wall R value (real or actual) will be either 28 or 33 (your proposed wall would have been 29). But! The
important part is that the interior foil surface of the foam becomes the condensing surface
in the wall and this surface is only 21% of the thermal distance into the wall. It very seldom
drops below zero f (not never but very seldom) and even less often does the interior humidity
exceed 50% when it gets that cold outside in zone 5 meaning that the temperature of that
condensing surface will always be above the dew point down to below zero - meaning no moisture buildup in the wall.
A few words about that foam: The foil surface becomes both an air barrier and a moisture barrier(the best that money can buy) - the foam is protected on both sides by the stud walls
(protected from unintentional physical damage, insects, fire, & thermal loss as the outside
temperature drops. It's best if in addition to taping the seams you also tape and/or caulk it
to both the floor and ceiling ,window boxes, plumbing/wiring penetrations, etc.
GOOD LUCK
Thank you for the feedback Forrest. Do you see any advantages to the 2x6/foam/2x4 approach you mention vs 2x4 walls for both inner and outer and thicker foam?
In response to your question: going with the exterior stud wall as a 2x4 and adding more foam would require an additional 1 inch of foam to maintain the same R value but the R value of polyiso drops with temperature drop (especially below 40 degrees). So, at outside temperatures below 15 degrees 2 inches would be necessary to be certain of maintaining the same whole wall R value. Therefor the question becomes is a 2x4 wall with mineral wool (with 2x4 studs at 16 inches on center) plus 2 inch polyiso less expensive than a 2x6 wall with mineral wool (with 2x6 studs at 24 inches on center) with no additional foam? I doubt it and I can't think of any other performance issues. This is also the reason for the mineral wool in the outer stud wall - using fiberglass (cheaper) would lower the temperature of the polyiso and consequently the whole wall R value -
this would in turn reduce the temperature at the inside surface of the polyiso ( the condensing surface) possibly below the dew point. These calculations can get a little involved - hope this doesn't put you off.
Forrest provides an outstanding wall design. Very high effective R value and durable. Both your wall and his require building it as-you-go. Outside wall first with its insulation, then the mid-wall insulation, then the interior wall and its insulation. Fully interior perpendicular walls would come last, though they could be done before the insulation in the inner stud wall. That would make inspection a little bit easier, but any of these walls will require close contact and communication with your building inspectors. In our area, all (ALL) of the framing must be done and utilities roughed in before they will allow you to put any insulation in the walls. That makes any of these sorts of approaches impossible without local approval in advance.
Thanks Peter. Coordinating the build sequence with the inspectors ahead of time is not something I had considered.