Vapor barrier behind brick chimney

I inherited a disaster of a home in Laguna Beach, CA, and am undertaking a complete rebuild of the house down to the studs. It is a 1944 beach cottage that is literally unsafe to inhabit currently. I have an architect drawing up the plans, but he seems unaware of the building science community, which is alarming since most of the conventionally built homes on the coast degrade rapidly from corrosion and moisture. I am trying to preempt this accelerated degradation by designing a weatherproof home, for example using 316 stainless steel fasteners on the exterior, etc.
I am theoretically Climate Zone 3, but we have a unique humid and foggy microclimate that is several degrees cooler than the rest of Southern CA, so I am designing for Marine Climate Zone 4 to be safe.
The main problem is that I have an old brick chimney, that I want to demolish, but my significant other is enamored with the idea of a fireplace and wants to keep it. I have read a lot about brick chimneys absorbing moisture, which then migrates into the wall and causes rot. I also know we can “get away with” a lot since it doesn’t rain that much, so I don’t want to overdesign the building, but the persistent humidity concerns me. That said, should I incorporate some kind of vapor barrier between the wall and chimney, or maybe just an air-gap for drying? Or should I just not risk it and demolish it all together.
GBA Detail Library
A collection of one thousand construction details organized by climate and house part
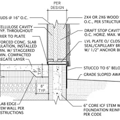
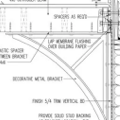
Replies
>"That said, should I incorporate some kind of vapor barrier between the wall and chimney, or maybe just an air-gap for drying? Or should I just not risk it and demolish it all together."
Current code requires an air gap between the masonry and combustibles, and an air gap is a pretty good capillary break.
The brick appears to be painted, which may or may not be a capillary break to limit the uptake of dew/rain. If the paint is stripped a silane/siloxane type masonry sealer applied to the bare brick and mortar chimney cap would be in order.
A stainless rain cap above the chimney top to keep direct rain penetration of the flue would also be a good measure.
A cricket and adequate flashing where the chimney meets the roofing is a necessary bulk water management feature, even in not-so-rainy SoCal.
Or you can just get rid of the thing and install a small wood stove with a glass viewing window door for ambience and taking the chill off. Open hearth fireplaces are an abomination with very heavy pollution levels and extremely poor fuel efficiency, and drives outdoor air infiltration 24/365. An EPA rated wood stove is a heating appliance with 4-5x the efficiency emitting only 2% - 5% of the pollution of fireplace. Even if you keep the chimney, an EPA rated air tight wood burning insert would fix most of those issues, though not quite as well as a free standing stove.
Thank you! Yes I will make sure the bulk water management is robust. That is the easy part. I did not even know EPA rated stoves existed. I will look into that.
Most new wood stoves sold in the US have a EPA rating of it's nominal efficiency and grams per hour of particulate emissions. Some of those aren't independently tested, and use some default numbers assigned that almost any newer stove of reasonable design would meet, others are tested and measured to the EPA's protocol.
Stoves with catalytic converters have the lowest emissions numbers by catalytic burning of the exhaust gases as the exit the stove. It has to hit a minimum temperature before that can work, but for hot fires (even small hot fires) it works really well. But low emissions on day 1 doesn't mean it'll meet those numbers on day 1000- the catalyst gets used up and needs replacement, and small smoky fires can clog them or burn them out early.
Most non-catalytic models use a secondary burner injecting heated combustion air (pre heated by the fire below) into the burning chamber near the top of the stove to light off any volatile gases before going up the stack achieve more complete combustion- those will still pretty much meet their day-1 performance as long as the air-injector secondary burners stay clean enough.
The short-story description from the EPA lives here.
https://www.epa.gov/burnwise/choosing-right-wood-burning-stove
In many locations it would be against local code to install a non-EPA rated wood burner due to local air pollution concerns. In other locations where wood burning appliances are ubiquitous, even EPA rate wood burning gets restricted on some days due to unfavorable wind/weather patterns. I suspect that neither would be an issue in Laguna Beach.
An EPA wood burning insert for a fireplace would be preferable to an open hearth fire, but with an exterior chimney the as-used efficiency will suffer relative to a free standing wood stove with the same efficiency numbers, since some of that heat is going directly outdoors, not into your house. (Unless you install insulation on the exterior of the chimney, which is another can of worms- it's easier and cheaper to just be rid of it and go with a small free-standing stove than it is to properly insulate an exterior masonry chimney.) It's still quite a bit more efficient than an open fireplace though. They come in a large range of sizes, and there will be one to fit almost any fireplace.