Use of rigid insulation on interior?

I am working on a 1970’s home renovation. There is no insulation in the walls or ceiling. The home is in Washington state, IRC climate zone 4 Marine. I could use feedback on the wall and roof system, specifically the air and vapor barrier and insulation design. My understanding is that the IRC and WSEC code requirement is to infill all existing walls and ceilings that are opened during construction with insulation but we wanted to add more than that. Existing overhang details preclude us from using rigid insulation on the exterior. There is also a new roofing on the structure, so we do not want to mess with that. This is the system that we are looking at using.
Walls
metal or wood siding (new)
building wrap as a moisture and air barrier (3 or 7mm VaproMat rain screen over weather resistant building membrane vapor rainsheild or equivalent) (new)
Ply sheathing (existing)
2×4 stud wall with infill unfaced rigid insulation or batt in joist bay (stud wall existing, insulation new)
R-5 unfaced rigid insulation continuous on interior (XPS or polyiso), tape all seams (new) vapor retarder
1/2” sheetrock w/PVA primer and latex paint
Roof
Standing seam metal (existing)
metal underlayment (existing)
1 1/2” T+G decking (existing)
4×6 rafters (existing)
1 1/2” airspace created by site built ventilation channels (new)
Infill rigid insulation or batts in joist bay (joists existing, new insulation)
R-5 unfaced rigid insulation continuous on interior (XPS or polyiso), tape all seams (new) vapor retarder
1/2” sheetrock w/PVA primer and latex paint
Questions?
I’d appreciate feedback on the effectivness of these systems.
I am concerned about condensation buildup in the walls and not being able to escape, I do want it to breath.
Should I be using faced or unfaced rigid insulation?
Is it wise to use rigid inside?
GBA Detail Library
A collection of one thousand construction details organized by climate and house part
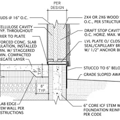
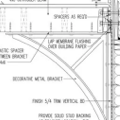
Replies
Use fully adhered building wrap for an air barrier and a better water barrier.
Consider strips of nailbase along the stud edges (although this won't provide an interior side air barrier).
Drying is beneficial - best if you can avoid < .1 perm vapor barriers (on either side).
For the roof, make sure that perms into the vent are much higher than interior side perms.
In colder climate, there is nothing wrong with interior rigid provided that there is drying capacity to the exterior. This is the case for both your roof and walls, so the interior rigid should work great. Your roof vent channels should be built with permeable material (thin plywood, fiberboard, housewrap or unfaced EPS).
If you are doing new siding, the wall air barrier should be taped sheathing. This is quick and simple to do and it is much easier to detail properly than foam since there is no device boxes or floor joists poking through it. It doesn't hurt to tape the foam as belt+suspenders approach, but you want to get your sheathing air barrier right.
Make sure you deal with the two main weak points at the foundation connection and at the roof. Peel and stick rated for concrete adhesion is best at the foundation. At the roof you want to have the sheathing air barrier tie back in to the ceiling air barrier. This is usually easiest with a bit of spray foam, one of the smaller 2 part kits works great for this.
You'll find foil faced polyiso the easiest of the rigid foams to tape. This is what I'd use in the walls and ceilings for the assembly you describe.
For vent baffles, 1/8" or 1/4" hardboard (a special kind of particle board) is probably your best bet. This is a cheap material, even with today's crazy materials prices (I just bought some PVC conduit today for a project, even that has gone crazy), and it's stiff and vapor open. Another possible option is kraft or fiberglass faced 1/2" polyiso, which is also vapor permeable.
XPS is the least green of the three common rigid foams, and it's also the one that tape least likes to stick to. I'd stay away from XPS in these assemblies.
Bill