Update to 1910 Duplex in 4a mixed climate attic insulation search

The search continues for a company that will do best practices for insulating my attic! It is a walkup attic (with stairs) with zero insulation, unvented, with two small windows in dormers. Balloon frame, stucco duplex.
To recap, I had one company that started out recommending 5 inches open cell foam against roof decking, told me to do my own air sealing with can foam ahead of time (despite fact that there is a big hole at soffit, like bigger than my fist, and my arms aren’t long enough to reach there). They also recommended closed cell foam at party wall in attic. Even though I use my attic for storage, they said they wouldn’t need to do intumescent paint unless I’m trying to sell soon (i.e. I wouldn’t get caught for violating building code).
Next company wanted cellulose in the 9″ gap between floorboards and plaster ceiling, but said they had no plan for the stairwell in attic that would be affordable.
Asked first company to bid on 2 inches of closed cell foam against roof decking (planning for flash and batt as Dana recommended).
Another company bid on 2 inches of closed cell foam.
The company that came today does do air sealing (hurrah) and did a blower door test. At negative 50, my numbers hovered around 5200… this is about 1300 sq feet, not counting attic and basement.
They also recommended open cell foam at roof decking, but recommended baffles above. Claimed 5 inches of open cell foam was ‘effective R38’. I said that’s not possible because of the R-value per inch of open cell foam. Estimator also claimed no one does closed cell foam in attic, only in basement and crawlspaces because of its water blocking properties. He googled his company’s comparison of kinds of insulation and it showed open cell foam is 3.7/inch. Oops. Then he was trying to say ‘it depends on the pressure of how you blow it in’… I’m like yeah, that’s the difference between open cell and closed cell.
This has been quite a journey!
I don’t know yet what this company is going to charge for air sealing attic walls/soffit/around chimney (They already charged $150 for blower test) but I think I’m going to have to go with them for air sealing, then another company for closed cell foam then install the batts ourselves. (Found out the other side of the duplex has fiberglass batts at their roof decking, so it seems like I can get away with not dealing with party wall)
I’m curious how bad the 5200 number is… any perspective there?
GBA Detail Library
A collection of one thousand construction details organized by climate and house part
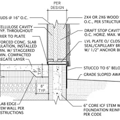
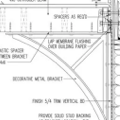
Replies
>"They also recommended open cell foam at roof decking, but recommended baffles above."
Open cell foam under a vent gap is very safe- that part works.
>"Claimed 5 inches of open cell foam was ‘effective R38’."
Utter BS, of course.
The real reason is that for many o.c. foam products 5-6" is the maximum amount that can be installed in a single pass, with a cooling/curing period required between passes to keep the fire hazard during curing low, and the quality of the installation high.
>"I’m curious how bad the 5200 number is… any perspective there?"
5200 cfm/50 in a 1300' space with 10 foot ceilings is 240 air exchanges per hour. Current IRC code max is 3 air exchanges per hour at 50 pascals. So yeah, pretty bad- your goal is to knock it back two full orders of magnitude to 2.4 ACH/50.
The good news is there has to be some pretty big easy to find & fix holes. The crude rule of thumb is 10 cfm per square inch of hole, so at 5200 cfm it's about 520 square inches, or 3.6 square feet of leak area. If that can be reduced to 0.25 square feet (36 square inches) by fixing the big holes the rest are going to be easier to find.
Is the square footage based on just the first and second floor, or should it include the basement and attic? If so, the square footage is quite a bit larger.
Interesting about the 3.6 sq. ft. I can only see one big hole in the attic, but of course, as I said in the first post, there's no insulation in the walls or attic.
I sort of wondered about where he chose to measure the building envelope, as there are three enclosed porches that are not heated; he included two of them. (That adds 12 by 5 for the upstairs porch and 16 by 9 for front porch; basement is 39 by almost 17, fwiw). When I questioned him, he said it didn't matter, as long as they do the same thing post-sealing.
Not that it changes the calculations much, I'd think, but our ceilings are 9 feet.
He looked around the second floor with an infrared camera -- you can see the lathe inside the plaster with that! The one upstairs window that is waiting for its storm window to be installed was a major cold spot, also.
He said our very old boiler (pre-1992) is operating at 78% efficiency. I am surprised it would be that good.
>"Is the square footage based on just the first and second floor, or should it include the basement and attic? If so, the square footage is quite a bit larger."
Normally the air exchanges per hour are calculated on the overall enclosed VOLUME (no square footage), and not just the fully finished fully conditioned space. It doesn't include vented attics or vented crawlspaces, which are outside the intended pressure boundary of the house.
So if the basement and top floor are roughly the same volume as the 1300' space you're talking "only" 80 ACH, which is still pretty breezy. There may be major air leaks from basement to attic from balloon framing, which should go down substantially if you air seal and insulate at the roof deck and insulate the walls.
When adding in the joist depths a 9 foot ceiling is still basically a 10 foot height from a total enclosed volume point of view, which is why I ballparked it there.
I learn so much from you! Basement roughly the same volume, but not sure how one would measure the unvented attic, since the ceiling in some places is much lower, but in some spots is much higher than 10 feet. At any rate, we knew it was leaky from the start, so 70 or 80 ACH is not a surprise. That's why I didn't want to bother with paying for an air blower test, but I couldn't find a company that did air sealing without charging for one.
We are not going to insulate the walls (and not sure if we ever will, given the stucco and plaster construction in living space and moisture issues along basement walls)... but hopefully this many thousands of dollars in the attic will make a big difference in comfort and natural gas use. Have a great weekend!!
Why closed cell in an attic? Open cell at 5" is an air barrier in itself and probably cheaper than paying someone to come out and spray 2" and then buying batts to put over it, say nothing of the hassle of installing them yourself. If you insulate joists instead you should be able to find someone to build an insulated hatch. I built one for fold up stairs out of 2x lumber with a pulley system to raise once, took maybe a day. Also built one over a spiral staircase with railing coming through floor, much more involved. Forget costs at this point but basic one would likely only have been a few hundred, spiral a good bit more. Huge improvements in the blower test from both though.
>"Why closed cell in an attic? Open cell at 5" is an air barrier in itself and probably cheaper than paying someone to come out and spray 2" and then buying batts to put over it, say nothing of the hassle of installing them yourself"
At only 5" open cell foam has a very high vapor permeance (well north of 10 perms), which is enough to excessively load up the roof deck with moisture over the winter to rot-risk levels, particularly on north facing pitches.
See the "Full-depth ocSPF" column in Table 3 in this document:
https://www.buildingscience.com/sites/default/files/migrate/pdf/BA-1001_Moisture_Safe_Unvented_Roofs.pdf
Even in locations as warm as Atlanta there is still some risk with an all open cell solution, even with 8.5-9" (R30-ish) open cell foam, which is more vapor retardent than a mere 5".
Then take a peek at the " 2" ccSPF + spray fiberglass column". Even at R49 total in locations as cold as Minneapolis 2" of closed cell is enough to be protective of the roof deck as long as the roofing material is dark shingles rather than "cool roof" type shingles or light colored metal roofing.
True I suppose, but nothing a layer of 6 mil poly couldn't fix if it was a concern. Probably better than foam really, considering it covers rafters as well and prevents wicking there. I recall that her house also has plywood rather than OSB which is significantly more rot resistant.
On a personal note, I work mostly commercial construction now but used to do residential, and have never seen rot caused by anything other than a direct leak, on a number of old new England houses with all types of insulation. My own mid 60s house had two bathroom vents going directly into the unvented attic until I bought it recently, with sagging, ripped fiberglass batts, and though there was a little mold around the outlets before reducting them outside, the rafters and plywood deck are very solid. Which isn't to say rot doesn't occur from condensation given the right circumstances, just that it isn't something I'd make a primary concern unless I lived in Seattle or the like. (I have spent a summer in DC and know it gets humid though).
Didn't see mention of Rock wool before, that stuff is really itchy. Not a fan.
>"True I suppose, but nothing a layer of 6 mil poly couldn't fix if it was a concern."
A 6 mil layer of polyethylene would create a moisture trap, and eventually doom some section the roof deck- maybe some rafters too. You may be able to get away with air-tight Intello Plus on the interior for the long haul, but not cheap sheet polyethylene.
>"On a personal note, I work mostly commercial construction now but used to do residential..."
Wintertime interior moisture drives are usually MUCH higher in residential buildings than commercial.
>"Which isn't to say rot doesn't occur from condensation given the right circumstances, just that it isn't something I'd make a primary concern unless I lived in Seattle or the like. (I have spent a summer in DC and know it gets humid though)."
Another common misconception.
Condensation and rot from interior moisture drives are pretty rare in Seattle, which has very very temperate roof deck & wall sheathing temperatures in winter, and low (sub 50F) average outdoor dew points in summer. The mean outdoor temperature in January is north of +40F- it has to be CRAZY humid indoors for condensation from interior moisture to become a problem. See:
https://weatherspark.com/m/913/12/Average-Weather-in-December-in-Seattle-Washington-United-States#Sections-Temperature
https://weatherspark.com/m/913/8/Average-Weather-in-August-in-Seattle-Washington-United-States#Sections-Humidity
Exterior moisture drives are the far more common causes roofs to sheathing and roof rot in western WA climates, sometimes with moss and mushrooms sprouting from shaded roofing, and bright green algae on the siding. (I spent the better part of 2 decades living in the Puget Sound region.) Adding 6 mil poly to the underside of an open cell insulated unvented roof in that climate would be courting disaster.
1910 Duplex will you please tell us your name?
Part of a proper blower door test is calculating the volume of the house and the ACH50 number and was likely done, most people would not know what it meant and they don’t want to spend time explaining it. You may want to ask and by asking you are putting them on notice you are not the average customer and you know more and care more about this work.
Will you have a second blower door test after the air sealing is completed?
Air sealing is hard nasty work but it is worth the effort. The only real way to find the leaks is to have a blower or a fan running. I do not see how paid workers can stay motivated working on someone else’s house so getting it done right may fall to you.
Being a duplex a lot of the leaks may be coming from the other unit. These leaks will not affect energy usage but are still worth hunting and blocking, because if air can get thru so will sound, smells and smoke.
Do you have a goal in terms of X number of ACH50 tightness? My thoughts are for an old building short of a total gut rehab 2ACH would be exceptional, 5 may be an OK place to stop after days of hard work, anything over 10 needs more work.
Like everyone else you want to get the insulation installed but it is important to get the air sealing right first because once the insulations is in it is now in your way making later air sealing more difficult and the insulation can’t do its job with air blowing thru it.
Walta
Walter,
my name is Mara (rhymes with Sarah).
I don't particularly have a goal, but hearing 10 is useful. I don't think he did a volume calculation, but it's possible he did while he was in the attic, since he had a laser tape measure and therefore could have calculated that volume. (The basement volume is pretty much the same as first and second floors). I will ask him when he gives me the pitch for the scope of work.
They will do another blower test after they do air sealing.
They already know I'm more clued in than the average customer because I argued when he told me that 5 inches of open cell foam is 'effective' R-38, since I told him that the per-inch value is 3.7 for open cell foam, so that is not possible.
In the case of my attic, fancy smoke wands are probably overkill? (if you search on my user name you can see pictures of my attic). There are a number of places where you can see the sky through little cracks in wood siding, or around the window frames. There is a maybe 9-inch by six inch hole at the soffit (this is a guestimate, as I cannot reach it from inside, but it was big enough for a bird to make a nest in)
I don't know if they'll be able to get to 10 by only air sealing the attic, since I have no insulation in the walls, and they'll only be tackling the attic, not the whole building.
Happily, there is virtually no sound transfer between the two sides -- only in the post-original-building enclosures (former sleeping porch upstairs and the enclosed front porch). My better half sometimes hears something in the bathroom, but I have not. I've never smelled anything from their side, though they smelled the polyurethane after our wood floors were refinished, and so I'll be warning them when we get the foam done so they can exit for the worst smelly day of that.
Totally agree air sealing must come first -- that's why I didn't hire the first company, because they were not interested in taking on air sealing in the attic before installing foam.
answer to JBVT -- yes, I looked into insulating at the joists, since there is 9 inches of space there, a little more than I have at roofline even at the deepest rafters. And the company that wanted to take that approach also estimated it would take a day to build a pulley trap door. But since was going to charge $2,500 for just the cellulose, it seemed like getting the hatch would be at least another $2,000... he didn't even bother to take a stab at bidding it. Installing the rockwool ourselves will be a drag, I agree, but it's hard to justify paying $3500 for it, which is the only bid I've gotten so far for someone else doing it... as it is, the payback for the insulation will probably be quite lengthy (though I think the comfort should be dramatically improved, and that's worth something, too).
Hi Mara
Maybe it me but if I do not set a goal things get done but not always done well or decide that’s good enough after so much time and stop and call it good enough sometimes it is and sometimes it is not, so I find goals helpful.
A window fan and a few incense sticks will find a lot of leaks.
I have to ask is there any old knob and tube wiring still in use in your home? If so please be sure no insulation comes in contact with the wiring and now before you are seal may be a good time to get it brought up to today’s code.
Walt
Walt,
we did have an electrician do a heavy up to our home, with special attention in our attic, where a previous electrician had not pulled a permit and had done lots of extension cord funny business. So no knob and tube there, and I think none active anywhere, though can't be sure of that.
Totally understand on the goal.
The aggravation continues. This company refused to bid just for the air sealing, and also refused to bid for closed cell foam. Instead they continued to suggest five inches of open cell *(though there is nearly eight inches of space in most rafters) with baffles and tumescent paint....
and wanted $13,000!!!!
Do you know how long it would take me to get payback on $13,000? I mean, my worst heating bills are no more than $300, and we don't have any cooling bills... going from R-2 to R-20 in the attic is what, maybe going to save 10-15 percent on heating bills??
to JBVT, they were going to install baffles to deal with the moisture issue, but the bigger problem for me is that R-20 (five inches of open cell+plywood/shingles) is not as good as R-30 (two inches of closed cell foam plus compressed R-23 batts).
I know it's going to be annoying to install the rock wool and probably itchy, but to save thousands....
>"Do you know how long it would take me to get payback on $13,000? "
No, I don't. But that's not what it's about.
Insulating and air sealing a roof deck about far more than mere energy savings "payback". It's about moisture management and comfort. You can discount the comfort as much as you want, but if you do it right it makes the place more moisture resilient, saving on potential future major repairs. If you do it wrong it makes it LESS moisture resilient, saving nothing. But 13 grand implies either a pretty big job, or for some reason they don't want to do the job.
For the record, how many square feet of 5" open cell foam are we talking?
If unvented, in my area $13,000 would buy something like 8000 square feet of 5" thick (40,000 board-feet total) half pound open cell foam in competitive bidding in my area. If installing the roof vent chutes were included there's more labor involved, which would have to add something (but still... ). If the attic floor is 1300 square feet you're probably looking at less than 2000 square feet of total roof area to be insulated which would run $3000-3500 for just the open cell foam part. There just can't be 9-10 grand of work installing the chutes. Even if foam costs 2x in your region compared to mine it seems too high.
oh, and this is from the "report" they gave me on why they're recommending 5.5 inches of open cell against roof (after adding baffles) and between three and five inches in gable end walls:
Gaps present along tops of interior and
exterior walls as well as around plumbing,
electrical, and other penetrations. These are
allowing hot/cold air migration to and from
the home through the wall cavities. The
existing insulation is not adequate. Area
contained some combination of flooring,
recessed lighting, storage and HVAC
ductwork.
Er, there is no recessed lighting on the second floor or in the attic. There is no HVAC ductwork in the attic. (or anywhere in the house, it's radiator heat)
I'll say the existing insulation is inadequate -- there is NO insulation.
Seriously, this is what you charged me $150 for? 'A blower test where you didn't give me the ACH number, no pictures from the fancy infrared camera, and a cut and paste job??
oh, and yet another update -- company that has the most reasonable bid for closed-cell foam reiterates that they don't do airsealing, though they have a page on airsealing at their website!
https://www.cameronhomeinsulation.com/air-sealing/
When I asked for a recommendation of who would, they had nothing.
I am losing my mind. I have been trying to hire someone since October!
Dana,
the attic floor is about 575 sq ft! I haven't measured all the roof decking, but another company was going to charge $2,730 for 6 inches of open cell foam in the same space. They weren't going to do intumescent paint or baffling, so that's a corner-cutting approach, and they weren't going to do any air sealing,,,, but yeah, the difference is extreme.
I think they're just counting on customers not shopping around since the $150 is a sunk cost?
I am still trying to find someone willing to do the air sealing, but if I can't, I may have to buy an extension ladder that can reach the third floor and try to figure it out myself!