Update on 1930 house in Northern MA (fieldstone wall, insulating, heat pump water heater in basement)
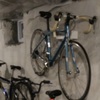
Thought people might be interested in the outcome of various renovations on the 1930 house we bought almost 10 years ago. I will post some photos.
As I explained in my original posts the basement was cold and damp with a fieldstone wall. Since the basement is not accessible from the house and we like to store items like lawn mowers and garden supplies there, we elected not to make it part of the conditioned space. We sealed it up well but did not insulate the two-foot-thick fieldstone walls.
Here is some good news: insulating the sill and the ceiling of the basement with 2″ of spray foam, then adding another full 3 1/2 inches of rock wool covered in fire resistant poly to our ceiling, we have finally warmed up the first floor of our house. No more cold floors, no more moist air coming up.
People here feared that the added basement insulation would make the basement cold, like below 32 degrees, having no heat source at all. So far it looks like temperatures will remain the same as they were before the recent insulation. If they stay above 45 degrees it is best because otherwise, we are forced to switch the heat pump water heater to electric resistance heating. That makes it less efficient in December through March. It would be nice to keep it in heat pump mode or hybrid mode all winter. Having a better sealed basement, we finally may be able to do that!
This strategy has had an impact on our use of natural gas. The gas bill for the 6 coldest months of the year (using normalized 2019 natural gas prices) has gone down:
2017 — $796.23
2018 — $676.65
2019 — $528.30 (Oct. 20-April 19)
2020 — $455.60 (October 20-April 19)
During that time we added a minisplit to the first floor as well as a remote thermostat. Right now it is not the primary source of heat but it does help us adjust the temperature when the house is uneven. During weekdays it is usually turned off.
We won’t be able to measure the full impact of these changes until March 2020. That will be a full year after the last insulation layer was put in.
*Still needing repair are the gaps in the first floor siding that let some cold air into the first floor walls and ceiling.
Here is my original post:
Basement insulation for a 1930 house retrofit (wall and slab)
a couple of photos from 2018:
(1) example of floor joists replaced and supported prior to the spray foaming of basement ceiling. About 10 joists were replaced or added.
(2) photo of replacement sill. Before jacks were removed, rocks were wedged under it and mortared in place by a stone mason to support the weight of the house. The sill was later covered with spray foam.
GBA Detail Library
A collection of one thousand construction details organized by climate and house part
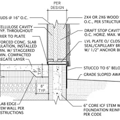
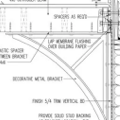
Replies
Those two foot thick field stone walls should have more than enough mass to hold and maintain any heat within the basement, even if you add a minimal amount of heat, just to keep it low moisture, the area should retain it.
>Those two foot thick field stone walls should have more than enough mass to hold and maintain any heat within the basement,
Finally, somebody else says this. On GBA, when I've brought up the idea of _not_ conditioning / finishing up our 2' thick field stone foundation walls, all the responses have been: cold basement. Have folks forgotten how much more mass there is?
> insulating the sill and the ceiling of the basement with 2″ of spray foam, then adding another full 3 1/2 inches of rock wool covered in fire resistant poly to our ceiling, we have finally warmed up the first floor of our house. No more cold floors, no more moist air coming up.
Great to hear. I'm still considering this option. To get at our cold floors, I'm finishing up standard GBA recommendations for all homes: basement window replacement (halfway done & on-hold till Spring thaw), rim joist seal & insulate, sub-pump for wet floor, etc.
Latest code allows another option to increase floor comfort besides complete fill: an air gap between basement ceiling insulation and 1st floor subfloor. I asked about that a few months ago and several smart / experienced folks chimed in: https://www.greenbuildingadvisor.com/question/new-code-option-for-cold-floors#comment-166404?utm_medium=email&utm_source=notification&utm_campaign=comment_notification&utm_content=view
I added a comment, reminding people that the location of the basement insulation may not make a huge difference as the sill (regardless of your method) will still be sitting on ~25 (F) degree foundation walls when temps get down near 0, in the winter. Even if the house is air sealed the temperature of the wall plate and studs can be much lower than the temperature of the air in an uninsulated basement.
To avoid cold floors it may be a good idea to insulate outside the sill, from ground level to a point above the level of the flooring that is cold.
vapor, thanks, unfortunately a lot of the posters here look towards new technology to solve their problems by using newer methods that are not time tested instead of investigating and understanding old technology which has proven itself over the centuries. If your field stone basement is usable space, I've seen ones that have been sand blasted, re-pointed and sprayed with a clear sealant to prevent moisture or the rocks from sweating. It really looks nice when finished.
Ah, re-pointing is something that's come up but the 1st time sand blasting and clear sealant has. Good to consider ... growing list of things for me to consider.
One thing that probably gets overlooked is making assumptions. Most old home basements (that I've seen) are thick field stone and below frost. Most new home basements (again, that I"ve seen) are thin cement block and walk-out. But not all homes; folks here have probably seen so many variants. Perhaps part of the 'old v new' disagreement here is not having enough time to consider all variables, with the "new" camp wanting to move faster and faster, so generalizations are made from assumptions before stuff really has time to set up after baking, so to say. So the assumption is that newer technology is based on newer (better) information and so must be best.
As a technologist (software), not a builder, I'm not convinced that "new technology" comes from more informed progression based on lessons learned from the ignorant folks in our past. Technologists (in my industry) have an amazing tendency towards amnesia when making broad claims about their new widget. Sometimes the new thing is just a new crap shot. Othertimes, it's that we really didn't capture what actually failed. Even Dr Joe comments, every once and awhile, about how long stone buildings last. They stand the test of time. The older I get, the more I like things that last.
I noticed Dana commented below about cavemen. Well touche. Bank robbers of the 1800's now just hack into online banking accounts -- like just happened to my brother-in-law. "Secure" online banking, two-factor authentication, thumbprint readers using smartphone banking apps, etc. "new technology" didn't stop people like my brother-in-low from being robbed. My point is newer != better, and there may be a good-enough alternative.
I have a house in RI built on a circa 1850 fieldstone foundation. The basement is part of the building envelope and mostly used as finished space, about a quarter is walled off for utilities. I sandblasted the walls and repointed them but didn't seal them, they look great, I'm very pleased. It's just the stone walls, a vinyl plank floor and a drywall ceiling, plus a drywall partition to the utility area.
It's not well-insulated -- dirt and stone -- but I feel I did a good job sealing it. In addition to pointing I insulated all of the rim joists with polyiso and spray foam. On the stone wall in the utility room I did closed-cell spray foam. I also installed a ducted dehumidifier. In the winter it's chilly -- it mostly gets heat from the boiler, it has a zone but I leave it off most of the time because I'm a frugal yankee -- but in the summer it's the most pleasant room in the house.
It's trimmed with cherry from a tree that fell on my property which fell in a storm and I milled into lumber.
First, congratulations on getting it right. It's a simple concept that a lot of people have trouble with, which is that you have to draw a bright line between the conditioned part of the house and the unconditioned part of the house, and then sealing and insulating between them. A lot of older houses were built with attics and cellars that are "kinda, sorta" part of the conditioned part of the house so this separation can be tricky.
I would disagree that thermal mass is what's keeping your cellar warm, it's because it's dug below the frost line. I have an unheated barn with stone walls, it gets plenty cold during the winter inside.
I think what the commenter meant to say about thermal mass is that the walls (plus of course the ground around them) can maintain a stable basement temperature above 45 degrees even when my heat pump is causing the basement air to get colder.
Also, if my basement were below the frost line it would be even warmer. Not all of it is unfortunately. If I can raise the grade around the exposed portion of the foundation we could benefit from the ground temperature even more!
DC, well how well is you barn basement sealed? In some cases if there is no air flow, or if cold outside air can penetrate into the space and has no way out, the cold will settle down into such a basement and stay there and it just keeps getting colder and colder whereby the mass retains the cold just as it can retain the heat.
No basement in that barn, just a dirt floor and stone walls.
>"I would disagree that thermal mass is what's keeping your cellar warm, it's because it's dug below the frost line."
No kidding!
Unless you consider the typical ~50-52F subsoil temperatures in northern Massachusetts "warm" that thermal mass isn't doing much for you. There are reasons why the locals who greeted the pilgrims back in the day lived in huts with thick bark cladding heated with fire rather than living in caves, dug out cliff dwellings, or high mass adobe type structures.
The most the thermal mass of a fat fieldstone or rubble wall will do for you in winter is to average out the daily swings in heat load on the above-grade portion of the wall. Most fieldstone in MA is granite. At the same thickness granite fieldstone is about 40% more thermally conductive as concrete. The R-value of THICK fieldstone walls can be twice as high as an 8" poured concrete wall, but not much more than that. It might even hit a hair north or R3 maybe even getting on to R4 for a REALLY fat wall, but that's well below the current IRC code minimum R15. Fieldstone walls usually leak more air than poured concrete too.
"There are reasons why the locals who greeted the pilgrims back in the day lived in huts with thick bark cladding heated with fire rather than living in caves, dug out cliff dwellings, or high mass adobe type structures."
Maybe because they used what was available to them in their environment, just like the other examples you gave.
>"Maybe because they used what was available to them in their environment, just like the other examples you gave."
There is plenty of stone in Plymouth MA (not just the one famous Plymouth Rock landing zone :-) ) and cliffy areas of easy-digging hard clays w/ sand layers, lots of available sand & clay and swamp-grasses that work easily for wattle daub or cob type high mass walls, lots of glacial moraine type rounded fieldstone too, but those methods were not used in that area. There are many abandoned granite quarries in that part of MA too. There is/was no dearth of available options.
The European settlers in Plymouth made use of a fair amount wattle & daub walls their timber framed clapboarded thatch roofed houses, but not high mass versions thereof.
Well those pilgrims weren't to bright. And I don't think they brought their quarrying tools with them. They wouldn't have made it through their first winter if it weren't for the local natives. After that they spent too much time doing witch hunts.
> After that they spent too much time doing witch hunts.
lol!
I have 2' deep granite block foundation walls. Could it be hitting R3/4 as well?
The R-value of typical New England granite is about R0.05 per inch, so at 24" it's about R1.2.
Add another ~R1 for interior + exterior air films on the above grade section and it's a bit more than R2.
I've seen antique houses in Maine with quarried granite foundations about 3' thick, which would come in about R3 after air films.
Below grade it gets more complicated. Dirt has some insulating capacity and the center of the earth is a giant heat source, the deeper you go the warmer the ambient temperature. It's hard to predict heat flow because the simple model used above ground doesn't apply.
Of course it's more complicated below grade- dirt has both R-value and thermal mass. But it doesn't mean that with a mean in locations January temp in the low to mid 20sF and a 100 year frost depth north of 50" and deep subsoil temps in the low 50s F that it's reasonable to expect this statement to be anywhere near factual:
"Those two foot thick field stone walls should have more than enough mass to hold and maintain any heat within the basement, even if you add a minimal amount of heat, just to keep it low moisture, the area should retain it."
It suppose it may depend on what order of magnitude one considers "...minimal amount of heat...", but I would expect in an otherwise reasonalbly insulated reasonbly tight house an uinsulated 2' thick fieldstone foundation is still well into double digits as a percenatage of the total heating fuel use, even if it's in the 40s & 50s F in the basement in January. The description "...the basement was cold and damp..." The thermal mass of the walls is buying nothing- it's still a net outward heat flow every day of the year in northern MA, pulling heat from the house through the floor above, but not much now that there is insulation between the basement and first floor.
There is no point to actively heating that space, but air sealing and insulating the walls will make it warmer year-round, parasitically heated by the the floor above, and the heat of the subsoil below, probably enough to be able to support a heat pump water. Without insulating the walls (or heating the space somehow) the mid-winter temps in the basement may fall too low for a heat pump water heater. While the heat pump water heater would be a great way to control summertime humidity, don't expect it to stay above 45F in winter on the heat coming up through the basement floor, or down through the now insulated first floor unless the foundation walls are insulated.
"The thermal mass of the walls is buying nothing".......really? Question for you....What is it that you heat up anytime you heat "something"?
OK, let's calculate the thermal mass in those walls. I'll use my house because I know the dimensions. The basement is 35' x 25' and averages about 6' deep and the walls are 2' thick. So there are 120 linear feet of walls, 720 square feet, 1440 cubic feet. Let's assume stone is 100 lbs per cubic feet to keep the math easy, so those walls have 144,000 lbs of stone. I pity the poor guys who stacked it all by hand.
Let's assume those walls get as warm as 65F in the summer time and down to 20F in the winter, so a swing of 45F. Stone has about one quarter the specific heat of water, and it takes on BTU to raise the temperature of one pound of water on degree F. So raising the temperature of 144,000 lbs of stone by 45F takes 144,000*45*0.25= 1,620,000 BTU.
A gallon of fuel oil produces 140,000 gross BTU., but with an 80% efficient boiler the net BTU is 112,000. So all of the thermal mass in that wall provides heat equal to 14.5 gallons of fuel oil -- assuming that 100% of it is captured toward warming the house -- per year. The last time I filled my tank I paid $2.44 per gallon, so all that thermal mass is worth, at most, $35 per year.
If we're going down this path, then similar maths can be used for other popular "green" products and techniques.
Take windows, like these so-called "best" imported Europen, triple glazed, low-e coated, Argon filled windows.
Martin wrote a fine, critical article on this a few years back that I was happy to read: https://www.greenbuildingadvisor.com/article/study-shows-that-expensive-windows-yield-meager-energy-returns. I was happy to read this because so many people, even on GBA, were pushing these windows pretty hard just a few years ago. To me the push felt like: if I didn't import these windows, then one might as well give up having an efficient home.
Basically all that extra expense to get as close to .1 U-value as possible via upgraded windows would, in one study that Martin cited, save the homeowner a whopping 8kwh per year. Which should be obvious! .3 U-value double pane to .1 triple-pane is moving from R-3 to R-10. Big deal!! Less than a buck a year in savings after spending tens of thousands on the "best" windows.
So if we're saying a couple R value improvements in thermal mass aren't worth it, then other popular "green" products, like Europen imported windows, are definently NOT worth it.
Give me thermal mass anyday.
>"So if we're saying a couple R value improvements in thermal mass aren't worth it, then other popular "green" products, like Europen imported windows, are definently NOT worth it."
That's quite a straw man you're building there! :-)
Nobody is saying that you should install better than code windows when the R-values or U-factors of the foundation walls aren't even close to code minimum.
What I AM saying is that thermal mass in a wall assembly (above or below grade) without R-value has no real benefit to a basement in northern Massachusetts.
I would also suggest that those U0.1 Euro windows aren't really very popular at all, even on better than code construction. U0.25 windows are just fine for most better than code homes in the northeast, and even upgrading to U0.25 windows from code min is more of a comfort issue for rooms with a substantial window/floor ratio, not about energy use.
>"Give me thermal mass anyday."
Go ahead, knock yourself out. Every uninsulated mass wall homes in the northeast (and there are many) are miserable in winter without pouring in huge amounts of heat- even those with 18" thick masonry walls, and have heating energy use numbers 3-4x that of much lower mass IRC 2018 code minimum framed construction. With a big enough boiler you can heat most anything to a comfortable level, if you don't mind excessive fuel use.
Vapor, LOL, yeah, I think it would be wiser to take all those tens of thousands of dollars doing upgrades to save yourself 10 bucks over the next ten years and go to someplace warm for the winter instead and enjoy life a little. Your house doesn't give a shit and never says thank you.
Thermal mass was the hot buzzword in the 1990's and the science behind it was always shaky. Unless it is integrated into the HVAC controls of the house it makes the house less comfortable because it is prone to overshooting.
The buzzword was used a lot of different ways, but let me give a couple of examples. I remember when radiant floor heat first got hot about 25 years ago it was popular to put piping in a concrete slab. "You need lots of thermal mass for it to work" was the mantra. Complete nonsense. Let's say you live in a place where it might be 50F during the day and 30F at night -- which is a lot of the US at some time in the year. If your indoor temperature is 70F, with the simple linear heat-loss model typically used your heating load is double at night what it was a few hours earlier. The model for heat produced by a radiator is also a simple linear formula based on temperature differential, so to double the heat output you have to double the surface temperature. So the temperature of that slab has to double in a few hours. The more surface mass it has, the longer that takes, and the less responsive the system. The following morning when the sun comes out the temperature of that slab has to drop by half or the house overheats. Unless you have a control system that is monitoring the outdoor temperature, indoor temperature and slab temperature you're not going to be comfortable.
(The fundamental mistake people were making was confusing the thermal mass of the concrete with its high heat conductivity. A radiant floor needs high conductivity to avoid hot and cold spots.)
Another application that has fallen out of favor is using thermal mass with passive solar. Again, the problem is lack of control and overshooting. If you have a totally passive house then sure, having more mass is better than not. But if you also have conventional controls that thermal mass makes the whole house less responsive, more prone to overshooting, and less comfortable.
And remember, comfort is the reason we heat and cool houses.
You're mixing apples and oranges. "So all of the thermal mass in that wall provides heat equal to 14.5 gallons of fuel oil".....The mass doesn't provide the heat......it stores it.
I wrote a detailed post, with numbers and calculations. Your response can be summarized as, "it doesn't work that way." OK, how does it work?
Well what is comfortable to you may not be comfortable to someone else. Going by a single standard doesn't work for everybody, unless you're in the gov. Perhaps you can calculate the heat process of a cast iron steam radiator instead. Temperature input can't be doubled on these, but yet they store and radiate heat and have worked in the past and still work today. A hot water tank heats up a volume and mass of water, that water retains the heat and slowly loses it over time to it's surroundings and can stay warm for days depending upon the temperature difference. The radiator and water are not the source of the heat, something has to heat them. If the mass is colder than the incoming heat, it will absorb it, once the source goes colder than the mass, the mass releases its heat until they come into equilibrium which is where you want to be.
In your example, you want to heat up the entire volume of the foundation rather than let it absorb what it can as long as it can. The outside portion of the foundation is already in equilibrium with its surroundings, the ground, so heat transfer will have a boundary. It is up to this boundary that the wall will absorb and store heat, no different than your well insulated above ground walls. But these walls have very low mass on the outside to hold and retain the heat that creates a barrier to reduce heat flow.. Think of the outside atmosphere as a low mass insulation. Remember T and P are directly related and work in the same way and everything acts like a fluid. Understanding the basic principles first doesn't rely on numbers. A slightly higher indoor pressure in the summer prevents infiltration better than any insulation. A colder indoor temp in summer has a lower pressure and invites infiltration. A higher temperature and pressure indoors in winter creates a higher heat loss. Working with these principles and figuring out simple ways to make it happen can save you a lot more than installing fancy, mechanical or expensive material items.
Remember, the energy co.'s need you to use their product, and if they can sell you the latest and greatest thing that breaks down in three years, doesn't work as advertised and cost you an arm and a leg to purchase and install, all in the name of saving you money, you've gotta wonder.
>What is it that you heat up anytime you heat "something"?
Thermal mass, of course. But unless there is something else in the assembly designed to retain heat heat going into the foundation's thermal mass is passed through to the outdoors or the soil. Thermal mass is buying you nothing in terms of net heat retention in the basement or the house- it just inserts a time delay in how fast the heat loss rate CHANGES as the outdoor temp rises and falls. The heat going into the thermal mass is always being lost to the outdoors (or soil), it doesn't "...hold and maintain any heat...", it's always just passing through, even if the rate at which it's passing through doesn't change instantly with a change in indoor to outdoor temperature difference.
To hold and maintain heat in the thermal mass there needs to be a substantially less thermally conductive layer (aka "insulation") on the exterior side of the thermal mass, or the thermal mass itself has to have low thermal conductivity. Most stone is way too thermally conductive for a 2 foot thick foundation to "...hold and maintain..." heat long enough to matter when the heat flow is always in one direction. It can only be beneficial if the temperature difference from interior to outdoors CHANGES direction on a time scale of mere HOURS (not days, weeks, months).
In a northern MA location the below-grade heat flow through the foundation is always outward (unless the basement leaks so much air it drops below the subsoil temp), varying only seasonally, and the delay inserted of thermal mass of the wall isn't long enough to measure such a slow changing heat flow. Above grade the thermal mass can lower the PEAK heat loss rate from diurnal outdoor temperature changes, but not the average, since it's always colder outdoors than in the basement in winter. During the shoulder seasons it can have a very modest heating energy use benefit if the basement is being actively heated, but it's barely measurable in an unheated basement that's only getting it's heat from the standby & distribution losses of the heating system.
So you are implying that something that has R-value is massless? Better re-read your physics book, then pick yourself up a book on thermodynamics and the fundamentals of mass and heat transfer. I guess we should rethink how we furnish our homes, build fire places, boilers, walls, water tanks and the atmosphere, not to mention the earth itself and figure out how to make them all massless.
'In a northern MA location the below-grade heat flow through the foundation is always outward".... again, really? This is a contradiction to your own statement of conduction.
UPDATE and Good News: I updated the dollar figures in my post. Over 3 years (2017-20), we reduced the use of natural gas by 43%. The main change is the insulation of the sill and the basement ceiling. The electric usage went slightly down during this period which means the additional power we are using in the house from our new (2018) first floor air source heat pump is completely offset by improved performance of the basement Geospring heat pump that heats our water.
Part of the goal was to warm the space where the Geospring heatpump resides without stealing any air from the conditioned space.
The fieldstone walls don't really store store heat, except in late fall when seasonally they are warmer than the ourside air. We use the fieldstone walls as a place to dump the cold air generated by the Geospring -- so that cold air doesn't affect the conditioned space above.
The air output from the Geospring can make the basement colder but it is only 1 or 2 degrees overall. The problem is that cold air would pool near the water heater. To fix this I ducted the output of the Geospring to the other side of a freshly built basement partition. The Geospring is now only 7" from that wall but it is finally able to run in heat pump mode all winter long.
I didn't mention in the original post that we also worked on the fieldstone walls before insulating. Many walls need old mortar chipped out and replaced especially if there is efflorescence, like we had on one wall. If we spray foamed those walls how would the next owner of the house chip out the bad mortar and replace it? I had a mason repoint the outside of the walls when we first moved in, getting rid of some of the voids. Inside, I filled up a lot of gaps with rocks over the years and mortared them in to prevent air from flowing through the walls. Finally I worked with the masons to coat the walls with a masonry product (cheap at the time) BASF Masterseal, which makes them clean white and attractive and prevents most of the water seepage in the spring.
One final upgrade is that the spray foam contractor was able to spray about 35 feet of exposed metal ductwork in the basement, which further prevented heat loss to the unconditioned basement space and warmed up what was coming out of 3 heating registers.
Now that the house is more efficient we may be able to eliminate the gas furnace entirely.
"The fieldstone walls don't really store store heat, except in late fall when seasonally they are warmer than the ourside air. We use the fieldstone walls as a place to dump the cold air generated by the Geospring -- so that cold air doesn't affect the conditioned space above."
So the stones are doing what they are supposed to do, they are absorbing excess heat when it is available and/or absorbing the excess cold keeping it from migrating elsewhere. Storage.
Good idea to monitor how cold it gets and open doors or windows in the colder months to introduce and circulate outside air when it is warmer.
What good is thermal storage that lasts a few hours at most? That's all you'll get out of a foot or two of stone. Enough to even out diurnal temperature swings but that's about it.
Circulating outdoor air into basements when it's warm outside is a good way to introduce a lot of moisture that raises the humidity into the range where mold and other microbes are happy. Unless you're in a very dry climate or the rare day in a humid climate where the it's reasonably warm outside and the outdoor dewpoint is lower than the indoor dewpoint, that is.
there is a distinction between the ground storing energy built up after 4 warm summer months or 4 cold early spring months.... and (as a few commenters suggested) the homeowner dumping energy into the walls to be reclaimed later. Yes we do the former with those walls but there is no way we are doing the latter. We are not sending enough heat or cold into the walls to make much of a difference.
I guess that IF you designed your fieldstone walls with a nice layer of insulation going all the way down to the base of your foundation, and even under the foundation, then you could go above ground temperature and actually store heat in the walls. Different from what I am doing.
Rich, exactly--you can look up "PAHS"--Passive Annual Heat Storage systems, sometimes called Umbrella Homes, which use the earth around the house to even out annual temperatures. Coupled with passive solar design, after a few years of acclimating, these homes need little to no supplementary heat. They do have their downsides, but at a certain scale and with insulation outside the building envelope, thermal mass can work in cold climates. But those conditions are not present in an uninsulated stone wall.
See my comment #21 about the amount of energy a stone wall is capable of storing, even after 4 warm summer months.
Here's my update.
It's pretty clear that the main heat loss in the house was through the first floor walls, it wasn't from the basement (due to the insulation under the first floor). The first floor walls, constructed in 1930, had board sheathing covered in multiple layers of clapboard and carboard and vinyl. There was cellulose in the stud bays, but any time there was a wind storm air easily penetrated under the siding and flowed through the interior wall. You could feel cold spots all around the perimeter, below our first floor flooring and above the first floor ceiling.
The only way to fix that was to strip off the five layers of external siding and replace it with continuous insulation, exterior insulation that is air sealed at all joints. And also locate the stud bays that were missing insulation, as it turned out there were a half dozen of those.
This really was necessary to make the house comfortable when heated with a heat pump. The noisy gas furnace is now gone and the house is all Mitsubishi. The second floor is not changed at all, but it was built to the 2004 building code so it's fine.
Here is a link to the new post:
https://www.greenbuildingadvisor.com/question/update-2-on-1930-house-in-northern-ma-adding-many-kinds-of-exterior-insulation-all-at-the-same-time