Unvented Low Slope Monopitch Roof Assembly

We’re building a custom home in SE Wisconsin and I’m looking for advice on the roof assembly. It’s a 1:12 monopitch roof so I’m guessing it’s better to go unvented. I’m attaching my idea for the assembly – 8″ of Rockwool or EPS on the exterior and slightly less Rockwool on the interior to give the safe ratio to keep the sheathing warm (51% exterior in climate zone 6). We’re also planning on a smart vapor retarder like Siga Majrex on the interior to also be detailed as an air barrier to prevent air from taking moisture to the sheathing. My question is what happens in the space between the interior air barrier and the bottom of the interior Rockwool insulation since the roof truss will be much more than 8″ (more like 28″)? Is that a problem? I don’t know how we could put the air barrier directly on the underside of the insulation with the complexity of trusses. I also would like to avoid spray foam for a few reasons so I’m hoping for a solution without that. Am I thinking about this correctly? Thanks for your help!
GBA Detail Library
A collection of one thousand construction details organized by climate and house part
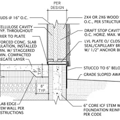
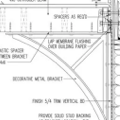
Replies
nmullenonline,
The air-space isn't a problem. You do want to make sure the rockwool stays in contact with the underside of the sheathing though.
Thanks Malcolm, that's good to hear. And the reason to keep the Rockwool in contact with the sheathing is to prevent any vapor from air that was trapped in the space from condensing on the sheathing? Or is it something else?
nmullenonline,
It's a code requirement. To be honest I'm not sure what the reasoning behind it is.
It is to prevent convective loops.
If you have an air gap, convective loops would continually move interior air into the gap between the rigid and fluffy which can create moisture issues.
Thanks Akos.
One more thing you can consider.
When you have continuous insulation, you can also comply based on the U factor of the assembly. I would check what your local code, it could be as low as an U.026 (R38) assembly. When you are building with expensive materials there is no ROI, either in energy savings or carbon footprint, for going above code min.
Thanks Akos, I'm not sure what you mean by 'when you are building with expensive materials' - do you mean because continuous insulation is more expensive than interior insulation? And wouldn't it depend on the energy model regardless of the code? I guess I'm not sure what you're recommending.
Exterior rigid is expensive in terms of material cost and labor. A couple of inches is simple to install but when you get up to 8" even the cost of fasteners can add up.
Of course when it comes to energy use, it is always best to model it. In my climate (north edge of zone 5), the energy use difference between an R38 roof and R49 is in the neighborhood of $10-$20/year.
My recommendation is to find out what your code U factor compliance value is and size your insulation from there. For example an U.026 assembly would be R24 batts plus 3" of exterior polyiso. Lot easier to install than 8" of rigid.
This is a good calculator for figuring out your options:
https://www.ekotrope.com/r-value-calculator
EDIT. that is for zone 5, in zone 6 you need a bit less fluffy or more exterior rigid.
I see, ok thanks Akos. Technically we're in Zone 5 now but only since they changed the zone maps recently so I'm still thinking it makes sense to build closer to a zone 6 detail.