Unvented cathedral ceiling — insulating from above

I am re-doing my family room roof, which is a cathedral ceiling.
Since the roof is being re-shingled, I thought it a good time to remove the sheathing and lay down some closed cell foam. I have some unopened from a previous project
Everything I’ve read about unvented Cathedral ceilings talk about them drying from the inside. Obviously this can’t happen if I’m spray in the closed cell foam onto the dry wall ceiling from above
The ceiling is 8″ from drywall to plywood
That is a lot to spray foam, and expensive. If all spray foam I assume it would then be completely air tight, but very expensive to spray that much foam
Is there an alternative to filling this completely with close cell foam? ..and still be unvented
I thought of using rigid foam on top of the sheathing, however I’m worried any air gap between the sprayed foam and sheathing might get moisture trapped
Is the best solution to vent, allowing some space above the close cell foam? Was hoping not to do this it would reduce the space available for insulation ( 8″ is not much to begin with ), and the top is on a head wall, not a ridge which makes venting more difficult
Any ideas would be very much appreciated
GBA Detail Library
A collection of one thousand construction details organized by climate and house part
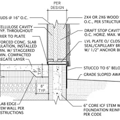
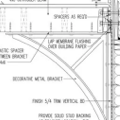
Replies
Paul,
There are two possible approaches.
One approach is the one you describe: remove the roof sheathing and install closed-cell spray foam from above. This approach works, and you don't have to worry about the one inch of air space between the top of the spray foam and the roof sheathing. From a moisture perspective, it will perform OK. (The only problem with this approach is that it doesn't address thermal bridging through your rafters.)
The second approach is to install rigid foam above the roof sheathing. If you are planning to install new roofing anyway, it's the perfect time to do the work. This approach addresses thermal bridging through the rafters, so it is the preferred approach. You can take the opportunity to fill your rafter bays with dense-packed cellulose insulation (working from above, by drilling holes in the roof sheathing) in conjunction with one or more layers of rigid foam above the roof sheathing.
For more information on the latter approach, see these three articles:
How to Install Rigid Foam On Top of Roof Sheathing
Combining Exterior Rigid Foam With Fluffy Insulation
How to Build an Insulated Cathedral Ceiling
Since i already had the close cell foam, about 1-2" across the space, I was first looking for a solution that would make use of it, without perhaps having to fill the entire cavity with close cell
Does rigid foam above the sheathing still work if close cell foam is below the sheathing, against the dry wall ceiling
Close cell against the drywall, air space, sheathing, then rigid foam?
Or.. same setup, with fiberglass batts/ cellulose between the close cell and sheathing
All rigid foam above sheathing procedures seem to imply drying from the inside. Does this prevent use of a closed cell and rigid foam combination
If you use the ccSPF kits you have, at the bottom of the cavity, against the drywall, and use fluffy insulation above it, you are right that you then need the top of the cavity vented. But then you won't have enough space to get the R-value very high, and probably won't meet code min insulation requirements (what's your climate zone?). You could then add rigid foam, eg polyiso, to the inside of the drywall and put new drywall on to cover it. But that's a lot of extra work ... Better to fill the cavity with cellulose, put foam boards on top of the decking, and use the spray foam somewhere where it solves a problem in a friend or family member's house.
Thank you for the responses
You have me convinced the preferred approach is likely to do away with the spary foam and do the rigid foam above deck, cellulose below deck approach
Part of the room however has a dropped ceiling, this dropped ceiling doesn't follow the roof line so ends up with a 3-4 ft attic space at one end ( compared to the 8" space between drywall and sheathing for all other rafters )
If I'm using cellulose, I'm worried about either leaving an air cavity above the cellulose in this dropped ceiling part, or having too much R value below the sheathing that the foam above will not be enough to keep the sheathing from condensing ( ratio of below to above )
Is there a best practice to follow here? Where I can keep the R value high enough but not have to worry about condensation
The ratio needed to keep the roof deck above the dew point of the interior air depends on your climate zone. It takes a heluva lot more in Fairbanks AK than Miami FL. The minimum exterior R values are called out by US climate zone in the IRC chapter 8 prescriptives, but they are based on the IRC chapter 11 minimum total R. If the total R is higher, the the exterior R needs to grow proportionally.
http://publicecodes.cyberregs.com/icod/irc/2012/icod_irc_2012_8_sec006.htm
http://publicecodes.cyberregs.com/icod/irc/2012/icod_irc_2012_11_sec002.htm
It basically breaks down as
Zones 1-3 it's 13% of the total R above the roof deck
Zone 4C-marine it's 20%, the rest of zone 4, 30%
Zone 5, 40%
Zone 6, 50%
Zone 7, 60%
Zone 8, 70%
To meet code the fiber insulation has to be in contact with the underside of the roof deck. So, for the areas with 3-4 feet of attic space you can either vent the space to the outdoors, and put the code min amount of insulation on the attic floor, or continue on up the rafters with cellulose blown in mesh or something.
Where are you located?
A very timely question for me. We just bought a gutted carriage house in Maine and our renovation plan calls for an open loft apartment upstairs. It's a hip roof with 8" rafters and double skylights at the center "peak". We had hoped to insulate entirely from the outside, but the roof is in okay shape. We're open to any approach including reroofing that keeps the ceiling open and makes economic sense. I've managed projects like this before, but not for a decade and in Florida not Maine. I've read the articles and others cited in Martin's response anticipating the conflicting views of insulation contractors, but I still wasn't prepared. The most often recommended insulation contractor told me he wouldn't touch the job if I wanted blown-in cellulose no matter how much rigid foam was used above the sheathing and another recommended using open cell foam rather than closed. There are always rabid opinions about insulation and I'm never sure if it's just that or someone trying to sell me something. I don't have a lot of options here for getting the job done so what's the best evidence I can point to to sway their opinions?
Thanks.
Kim,
You're right that insulation contractors often provide conflicting advice, and that some insulation contractors haven't kept up-to-date with the latest building science research.
When it comes to preferences for open-cell over closed-cell spray foam, or vice versa, the reasons for these preferences often have to do with economics or familiarity rather than building science.
I can assure you that a roof assembly with an adequate layer of rigid foam above the roof sheathing, and cellulose between the rafters, will work well. Any insulation contractor who disagrees is ignorant.
Good luck with your project.
Ha! Martin, you don't mince words. Thanks for that definitive answer.
Kim,
Of course, the definition of "an adequate thickness of rigid foam" is strict.
Details are provided in the three articles that were mentioned (with links) in my first answer to this thread.
Martin,
Yes, I've managed to get the figures 36% and 51% of the overall R value to stick in my head.
Martin,
The more I consider this the less enamored I am with the idea of foam. Would the use of Roxul's Comfortboard in place of exterior rigid foam change the calculation of exterior R value as a percentage of the overall value?
Thanks.
Kim,
If you are designing a roof that can't dry to the exterior (for example, one with asphalt shingles, most types of metal roofing, or EPDM roofing), then you certainly would need to use the same R-value guidelines for mineral wool as are provided for rigid foam.
If you are choosing a vapor-permeable roofing material like slate, concrete tiles, or cedar shingles, the R-value rules wouldn't apply.
All of that said, installing mineral wool insulation on the exterior side of roof sheathing on a sloped roof assembly is rarely done, so you would be pushing the envelope if you went that direction. Only a few people have experimented with mineral wool in that location. Mineral wool is a little squishy, and how you handle its squishiness would take a little thought and planning.
Sorry, Martin, my reading and thinking had shifted to the walls and I'd forgotten the original question here was regarding the roof. But good to know.
Kim,
If you are thinking about walls, your question was answered in my article, How to Design a Wall.
In that article, I wrote:
Mineral wool insulation can be substituted for rigid foam insulation on the exterior side of wall sheathing. One advantage of mineral wool over rigid foam: because mineral wool is vapor-permeable, it doesn’t inhibit wall sheathing from drying to the exterior. That means that builders can install mineral wool of any thickness on the exterior side of their walls. You don’t have to worry whether exterior mineral wool meets any minimum R-value requirement. (Of course, thicker insulation always does a better job of resisting heat flow than thinner insulation.)
For more information on the installation of mineral wool insulation on the exterior side of your wall sheathing, see these articles:
Installing Mineral Wool Insulation Over Exterior Wall Sheathing
Installing Roxul Mineral Wool on Exterior Walls
Wrapping an Older House with Rock Wool Insulation