Sealing a Vented Attic

Feel like this question must have been answered somewhere, but am at a loss. Hoping to go from a vented attic to unvented since air handler and ductwork is in the attic.
1. In Paso Robles, CA where summer time temps reach 110+ F and winter reaches ~40F.
2. The attic has just two gable vents. It has no eave vents or ridge vent. Hence we have to do something, seems like heading in a unvented direction is better given the HVAC.
4. The roof covers the house, breezeway, and garage, so would be cost prohibitive ($20k) to spray foam. Dimensions are 74’x30′.
3. Currently there is sparse batts and cellulose on the floor.
4. We need to do a re-roof in the next year.
Would love advise on best path forward… do we just install eave vents and add blown in over the living area of the house (34’x30′) or is there something that can affordably be done to move the HVAC into a conditioned space without risking damaging the roof?
Options I’ve considered:
A. Vented with radiant barrier under roof deck and R38 blown in.
B. Vented with R13 under roof deck (possibly polyiso), radiant barrier, and R30 blown in.
C. Unvented… ?
GBA Detail Library
A collection of one thousand construction details organized by climate and house part
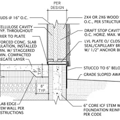
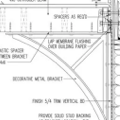
Replies
Hi jcraffi
Just to clarify, do you have trussed, constructed of 2x4's, or legitimate rafters, made from 2x4's? For the span you must have either site built trusses, purlins, or something up there supporting the roof over that span.
The cheapest option is a vented attic (soffit and ridge) with blown in insulation on the attic floor, and it does a very good job at insulating. What it doesn't do well is keeping the air handler and duct work inside the conditioned space. You can bury the duct work in the insulation, which helps, but I view that as something of a band-aid, and I'd have to offered about half a million to work on it later.
The next least expensive option is multiple times more expensive, regardless of what that is. Insulating between rafters can work well if they're true rafters, and somewhat deep. You'd need at least 2x10's to get in the R30's with a ventilation channel in the bays. You can't do un-vented with fibrous / air permeable insulation. It's prone to moisture damage. There's a solution called a 'vapor diffusion port' that is supposed to mitigate that, but it also requires you to already have those rafters in place.
The next solution (more expensive) can work un-vented, which is exterior insulation on the roof decking, if it is in good shape, and if the roof can support the additional (albeit small) load. Using a combination of polyiso above the deck, and open cell spray foam below the deck can work, but it requires a good air barrier on the roof deck, and is much more labor intensive than any of the other options listed here. It also requires some imaginative thought as a retrofit, with modifications to the fascia. It solves all of the problems, but is probable more expensive than closed cell spray foam under the deck.
Just throwing those out there for thought.
Hi Kyle,
Thank you for your reply!
Blown In: Agreed, cheapest option is a band-aid. Seems to be the default option, but really trying to avoid it.
Insulation between Rafters: You're correct that we have trussed constructed of 2x4's. Relatively shallow slope with 6' height at the center. Hence my thought of R13-19 (possibly polyiso), radiant barrier, and R30 blown in on the floor. Pros/cons of this hybrid setup? (Option B has a vented version of this: https://rbhinsulation.com/wp-content/uploads/2017/10/JM-CA-Title-24-2016-Attics-and-Walls.pdf)
Polyiso above the deck also solves another problem I didn't mention, which is that the living room is vaulted (no attic) and has no insulation on the ceiling. So that would kill two birds with one stone.
There has been some discussion of that hybrid assembly on this site before. At its heart, I feel there's a dichotomy of bringing the energy codes up to maximum efficacy, and minimizing costs, and title 24 is the best compromise a group could find. It somewhat brings the attic into a (more) conditioned space, thereby reducing the insulation required on the attic floor.
I appreciate the attempt being made, but it's not a solution that I would implement for myself. Any amount of blown in insulation essentially voids any interactive use of the attic. To me it doesn't matter if there's 16 inches, or 4 inches. The results are the same - it's going to be messy to work in and I know I wont make trips up there for storage, three's just no place for it.
There's a lot to digest and weigh here -
(1) There's a section of roof that is uninsulated, and certainly the largest 'energy hole' in the structure.
(2) The attic isn't really that useful for storage
(3) air sealing to make the attic unvented is actually really hard, especially when trying to work in the small angle sections of the roof
(4) A new roof is imminent
(5) continuous insulation R value is not derated by a framing factor
Digesting all of that -
You need to insulate that section of roof that is uninsulated. Otherwise adding more insulation to other sections of the roof will not really save you any money on utilities, and that's what we're trying to do after all. Combine that with the fact that you'll be working on the roof anyways means you have a one in 30 year chance to make any sort of structural change without incurring the cost of a early shingle / tile / metal roof alteration. An air barrier of any kind smashed under Four inches of polyiso on the roof deck would provide you something around R28, all things considered. While that doesn't sound like a lot, it is equivalent to ~ R32, if cavity insulation were used with 24" OC truss spacing. That's huge, and going from R32 to R40's doesn't save anywhere near that much energy. It's kind of like our mpg fuel economy measure - going from 18 to 24 mpg saves much much more than going from 24 to 30 mpg.
If I were doing this my self, I'd propose this kind of assembly from outside to inside. (assuming shingles, I'd modify it for tile)
shingles -> #15 felt -> OSB -> 2 x 2" layers of polyiso -> tyvek or similar WRB* -> original decking, assuming it was in good shape. Vacuum all the other insulation out, and just have a nice empty clean attic.
*Tyvek isn't typically used on a roof. But this isn't a roof, it's a wall laid on its side. Many other self-adhered products exist, but they're overly expensive for the use case here.
The layout above has these advantages
(1) Achieves insulation on the uninsulated roof section. There's no other way without disrupting aesthetics
(2) preserves roof elevations
(3) maximizes r value / cost
(4) provides an effective air barrier
(5) conditions the space for duct work and air handler, possibly storage in some areas
(6) practically guarantees water damage will never happen, not that it's a problem for you.
It has these drawbacks
(1) It costs much more than other insulation types, you have to buy natures gold (wood) at the moment, long screws cost a lot, and because of the distance between the outer layer of OSB and rafters, it's slow to install. That is to say - the material cost is more, the labor cost is more, and the project time is longer.
(2) It requires you to air seal the attic well. Cover up the gable vents and calling it good just wont do here
(3) Nobody within 200 miles of you, with exception of maybe a handful of over achievers has done a roof like this. Title 24 is still new, and most of the houses built don't, or haven't had continuous insulation on the roof. You'll get odd looks, stares, and questions from everyone you ask about it. They won't know how to quote it, and many will probably ignore your inquiries. The lumber yard will think you're crazy, your dog will think your neighbor is his best friend, and your spouse will start to burn every dish that's cooked. Such is life when you're going against the norm.
(4) Current roof penetrations will have to be moved upwards to the new deck. Vents may have to be extended, etc.
(5) elevated humidity could be a concern if the house were a new build and already very tight. I don't think this is your case, and it's probably not a concern to worry about.
I hope that provides a few things to think about!
Incredibly helpful! Once in a 30 year opportunity and fixing the giant hole in the thermal envelope really resonate. Interesting to get your take on title 24. Hadn't heard it stated that way, but makes total sense now that you said it. Compromise solution. Likely will do the new roof install early next spring (slow season in Paso Robles), so will give me enough time to plan ahead. Will post update with how things go.
Many thanks again! Your thoughtful response for a stranger speaks volumes.
You're welcome. I'd urge you to keep seeking out opinions, mine's only worth the paper it's written on! If/when you start, be sure to post back. Surely you'll have lessons learned that you can share with all of us.
An added bonus is that the price can be reduced further by using reclaimed rigid foam.
Let’s talk about the elephant in your attic.
Consider locating the HVAC equipment and ductwork in the attic, is was and forever will be a poor choice someone made long ago. If you are motivated to spend money on this problem (I am not sure it is a good choice) the smart move maybe to undo the poor choice and move the HVAC equipment inside the conditioned space.
My wild guess at the operating cost of your options.
Leaky HVAC in vented attic=3x the electric bill.
HVAC in vented attic=1.5x the electric bill.
Conditioned attic = 1.2x the electric bill.
HVAC below ceiling=1x the electric bill. (Mini split heads in room)
Given that most people will move in less than 7 years except for patching up the leakiest of ducts you are unlikely to recover the cost of the improvements you are considering unless you are sure to stay much longer than average.
Walta