Unvented airtight flat steel roof without spray foam?

I am in the hot-dry climate of Phoenix, AZ. I have a barn constructed of a skeletal steel frame filled in with plywood walls and topped with a corrugated steel flat roof. It is essentially outside-space with the complete lack of insulation and anything resembling air sealing. There are four enclosed stalls and I shall be converting one of those into a band practice room. This entails creating a heavily sound-attenuated room-inside-a-room. Airtight; mass with drywall; absorption with fiberglass; that type of thing.
The outer shell (plywood walls; steel roof) are considered the outer “leaf” of the soundproofing shell and so shall be made airtight prior to building the interior room.
I am concerned about the ceiling / roof in this new setup. It’ll have a drywall ceiling suspended by joists and holding up as much fiberglass as space allows below the corrugated steel roof. That roof gets blazing hot more than it ever gets cold but it likely can lose a lot of heat at night to night-sky radiation and if the conditions are just-so, could even dip below the dew point. This feels like a solid scenario for condensation on the underside of the roof.
This cannot be a vented assembly. The canonical way to handle it would be to spray foamĀ the underside of the steel and I could even get a froth-pak that would do that. But I’d very much rather not do that!
I would be confident that I could accomplish the same thing more easily if I had a smooth flat roof (plywood or OSB) by just attaching rigid foam sheets, sealed around any edges. But I’m concerned that this wouldn’t work in my case since the roof sheathing is corrugated and so the foam will only be physically touching a very small percentage of the roof.
I’ve seen references to maybe using dense packed cellulose to completely fill in the space. That would maybe modulate the roof temperature like foam and keep air from notably moving in the cavity. That’s not talked about a lot, though, so I’m unclear if that could work in my situation?
I even wonder if not doing anything special could work since the entire shell will be airtight and so I’m not sure where the humid air that could condense would even come from?
What are y’all thoughts on this?
GBA Detail Library
A collection of one thousand construction details organized by climate and house part
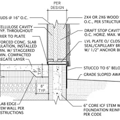
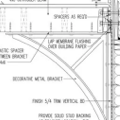
Replies
Is the shell currently airtight?
I think you'll save yourself a lot of trouble by not using the existing shell as the outer layer of the soundproofing and conditioned space. Build a building-within-a-building, and have a layer of unconditioned air on all sides of the conditioned space. Make the inner building air-tight, let the outer building be vented. Along the walls the gap only needs to be an inch or so.
The shell is currently far from airtight -- think "holes big enough to see through" levels of air infiltration.
I agree that doing the minimum to the shell is the most guaranteed and easiest method. My concern is that it wouldn't be good enough doing its job at noise abatement. The bands that practice in this space feature heavily distorted grungy guitars, screaming and growling vocalists, and drums beat so hard that the sticks last no more than a week. The end result is multiple visits by the local police and even more complaints by the neighbors.
Just having a sealed inner shell will go a long way towards toning down the cacophony... but this type of noise is particular hard to truly tame and so having an extra leaf to work with could go a long way. And since convective air is one of the best sources of flanking noise, doing everything I can to stop that is going to be a top priority.
I may still go the "vented" route, but wanted to explore possibilities of what it would take to not.
Second what DC said, building within the building.
You still need to seal the outside, but not the outside of the existing shell. Air seal of the exterior of the new structure. Much easier when it is all part of the plan.
If it is concrete slab it can carry bass. There are ways to deal with that as well.
I'm not actually concerned about the concrete slab. Bass does travel extremely well over concrete, as I've seen first hand with my own home theater, but it doesn't typically end up being the part that reproduces the noise -- it's the part that's carrying the noise waves to some remote wall or similar that will vibrate enough to create the noise. And since the barn's concrete slab is surrounded by earth a good 50 ft (at least) from the nearest neighbor, the bass doesn't end up being a big component of the noise.
I only know a little bit about soundproofing, but my understanding is that you want walls that are heavy and stiff. Something that when you knock on doesn't make much noise. The way a wall transmits sound is the air in a sound wave on one side of the wall pushes on it and makes it vibrate. This causes the other side of the wall to pass the vibration onto the air, creating a sound wave. Metal siding is rather lightweight and stiff and I think would be an excellent conductor of sound (or a poor damper, depending on your viewpoint.) Think of what metal siding sounds like when you tap on it.
I think your best bet is going to be a box with double walls that aren't linked to each other, with a double layer of 5/8" drywall on each of the walls. It's not hard to detail the drywall so it's airtight.
This airtight room is going to need ventilation. I'm thinking a long piece of flexible insulated duct -- like 50' -- on the intake and exhaust would give enough sound deadening, maybe not. I'd put a heat exchanger on it, and put the HVAC outside of the performance space so the noise of the HVAC doesn't bleed in.
I do actually know enough about the soundproofing aspect of it to be mildly dangerous but yeah, you are correct that the metal roof (and plywood exterior walls) have very little mass and so will only go so far in attenuating the sound. It's not nothing, though.
Okay, the idea of a building-in-building model is attractive on the surface but has two fundamental problems in practice. The first is that I'm not sure how I could practically attach and/or seal the "exterior" sheathing and roof INSIDE of an existing shell, since I will have zero access from "outside". I would essentially have to rip up the existing metal roof to have access to the inner roof and, honestly, if I'm doing that, I might as well be tearing up everything -- which I would love to do -- but there's no time or budget for that!
And even if I figured out how to do that, it would likely have worse performance than the alternative. The problem is that the inner walls and roof combined with the still existing outside shell would create a "triple leaf" design. Triple leaf designs will nearly always underperform any similar design that just has two leafs, since that third leaf is essentially creating a smaller "spring".
Okay, so one of the best tools for sound attenuation is to use mass in a mass-spring relationship. The "spring" will be something like trapped air or (even better) an absorption material like fiberglass which traps even more air and makes an even bigger conceptual spring. Increasing an assembly's performance typically means either increasing the mass or widening the spring. In the case of a triple leaf construction, you'd have mass-spring-mass-spring-mass, where the springs are relatively tiny due to the mass in between them. If you remove that middle mass, though, then you have mass-spriiiiing-mass with a MUCH bigger area to work with. This will dramatically lower the resonance point, which is great since most of our sound/noise is in the higher frequencies and so that's one less way for the assembly to fail.
You are right that this will need ventilation. There are proven designs for ventilation in studios and theaters so I'm not concerned there. You are spot on with the way you are thinking about it in the sense of no straight lines and move as much of the equipment as possible outside of the space.
The first is that I'm not sure how I could practically attach and/or seal the "exterior" sheathing and roof INSIDE of an existing shell, since I will have zero access from "outside".
To be clear, what I'm proposing is that the outer sheathing of the inner building be a double layer of 5/8" drywall. I would build the walls on the floor and stand them up, that's how framed buildings are built all the time. I'd do the inner and outer walls separately, I'd build the outer walls first, put the drywall on before standing them up and seal them and do blower-directed sealing (IE pressurize the space with a fan and use smoke to find any small leaks) all before building the inner walls. The outside corners of the outer walls won't be accessible to seal so I'd seal the inner corners with spray foam. The inner walls and ceiling could be drywalled after being stood up and sealing them will be easy because the entire face is visible. I'd glue and screw throughout. I'd fill the space between the two walls and ceilings with dense pack cellulose.
If you don't have enough headroom to drop the ceiling and get in between the roof and the ceiling to drywall from above it's going to be a little tricky. What I would do is run ceiling joists on the top of the outer walls and hang a double layer of drywall from below. Tape the seams and spray foam the corners where it meets the walls. The inner ceiling has to be a few inches lower, which means the inner walls are shorter.
In Phoenix I'd imagine that occupant activity is going to be the main source of humidity. While this entire assembly is breathable there's not going to be much vapor drive to the exterior, you're going to have to rely on your HVAC to remove humidity.
You can also build the outside wall and celling first, offset this from the existing structure. Cover with house wrap on the outside to deal with condensation dripping from the metal panels.
Now install denseglass/CDX/OSB over the INSIDE of this wall. Since this is all inside it is easy to detail. Air seal all seams. Install the 2nd layer of drywall over this layer. Tack 3" batts to the wall with long cap nails.
Build inside structure offset from the batts by about an 1" or so. From there it is standard build.
The existing building shell elements are outside this double wall structure so it doesn't create any triple leaf effects. If anything, the extra air gap increases the overall STC of the assembly.
Important part here is you don't want any part of the new structure touching the existing building shell.