Uninsulated Floor deck over exposed earthen crawl space – Climate zone 5

I am planning to install a 6 mil polyethylene vapor barrier as depicted in the detail library of Green Building Advisor.
I also want to install rigid insulation to the underside of the floor joists.
Owens Corning professes to have eliminated hydrofluorocarbons and other toxic agents in a new formula blowing agent. The material is called NGS rigid insulation available in 1″, 2″ and 3″ thicknesses at -5 per inch.
Does anyone have experience with NGS?
Any recommendations to the details I describe?
Thank you in advance.
GBA Detail Library
A collection of one thousand construction details organized by climate and house part
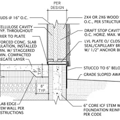
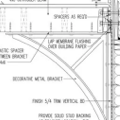
Replies
I think the smart move is to seal the exterior vent of the crawl space insulate the wall and cover the earth with a plastic and install enough HVAC vents so the crawlspace is more or less the same temp and humidity as the rest of your home. This would be a fully conditioned crawlspace.
Warning anything less than fully conditioned or total vented is risky in that things may get wet and stay wet long enough for mold and rot set going.
Walta
Agreed 100%.
I was trying to come up with a hybrid detail that would uncouple the floor joists and deck from the crawl space with less permeable insulation, taped and sealed at the perimeter, and control soil gas and moisture from the earthen crawl with polyethylene vapor barrier, I've been advised that 10 mil would be the correct thickness.
I will price out the details you recommend. Thank you so much.
+1 for sealing and insulating the entire crawlspace.
I would recommend that you go with at least a 10 mil thick crawlspace liner on the floor though. 6 mil poly sheet, while the minimum acceptable by code, is really too thin to hold up very well, in my opinion. 10 mil sheet is much stronger, is probably the standard for most of the pro crawlspace crews, isn't terribly more expensive, and will be less of an issue in the future if you have to go down there again to do any work. If you expect to be servicing things in the crawlspace more often, thicker than 10 mil may be a good idea. If you're going to be storing things down there, go for 20 mil.
Working in a crawlspace is not fun. Build things down there to last the first time so that you never have to do the work again.
Bill
MarcoD,
Sorry I don't have anything useful to add about NGS insulation.
While I generally agree with Walta and Bill about how to proceed, vented crawlspaces do perform quite well in parts of climate zone 5, so going that route isn't as fraught as it might be elsewhere.
If you do insulate the floor, it may affect the possibility of plumbing freezing in the crawlspace. Think through how you can protect those services as they move up into the conditioned spaces above.
Do you think I run a risky scenario by uncoupling the floor system with R-15 rigid insulation, all joints taped and perimeter sealed? Some think that detail would encourage moisture to form in the joists cavities and underside of subfloor.
MarcoD,
No, as I said in one of my other posts - it's very similar to how you would insulate the floor if the area underneath were completely open as it often is on houses built on piers.
Thank you so much for your reply. I'm a new member to this awesome site. I will investigate wats to protect the plumbing services moving up through the floor deck.
We've done a lot of crawl spaces like this.
If I were you I would block up all the vents put down a double layer of 6 mil poly vapor barrier & two inches of rigid foam insulation and pour a concrete slab over it, you can hire a pump to get the concrete in, you could run the hose in through an open crawl space vent before you finally close them up, if there are no open vents you could cut a hole through the rim joist or knock out a block to get the pump hose in.
I have been in many crawl spaces with poly only over the dirt floor and after time the poly gets brittle and cracks and stops doing its job.
If you’re not going to pour the slab at least get the string re-enforced poly, it will hold up much longer than the regular poly or vinyl pool liner.
We caulk or foam the plate or sill to the foundation and then only insulate the rim joist, we usually do a 2 inch layer of foam board and then a layer of Rockwool insulation over it but we've also done a double layer of R23 Rockwool, you can figure that out what will work best for you.
We have never insulated the walls of the crawl space but we do introduce conditioned air into them, if you think about it, heat rises and so if you put heat in there in the winter it's going to rise up to the underside of the wood floor and the insulated rim joist is going to hold it in where it is most needed, then the floor above will be warmer.
The biggest reason I see to insulated the walls is if the duct work is un-insulated, but the best solution to that is to insulated the duct work and of course there's no problem with insulating the walls but it's another step you might not need to take.
If you stay with a dirt floor and insulate the walls with rigid foam be careful you don’t create a path for termites to travel from the dirt floor, up behind the rigid foam and into the wood framing above. Keep the foam a few inches above the floor and a few inches below the sill plate.
If there is No duct work in the crawl and you do want some air movement in there you can set up a bath fan in an adjacent basement or a closet above and use it to blow air into the crawl using 3 or 4” bath fan duct work.
You can set up a thermostat in the crawl so the fan comes on when things get down to a certain temperature, you can also set it up with a humidistat if high humidity is the problem.
Whatever you do don’t insulate the underside of the floor with fiberglass or Rockwool, it will become a huge mouse hotel and toilet.
I would also not insulate the underside with rigid foam board as mentioned above that seems like a high-risk scenario for trapping moisture between the rigid foam and the sub-floor above and as the other person said likely rot.
Jud_Aley,
If using rigid foam on the underside of the floor on a building supported by piers is part of the preferred method of insulating, what causes the worry about doing the same over a vented, unconditioned crawlspace?
I'm also not sure that possible water intrusion from the outside is a suitable reason to use a vapour-open insulation on rim-joists when we know it causes problems. The place to address bulk-water issues is on the exterior, not try and compensate for a failed wall assembly by giving it the ability to dry to the inside.
I'm curious why you prefer a double layer of 6 mil over a single layer using thicker material like 10-12 mil. Have you seen some advantage with the two layers, such as allowing for some slip or something like that?
Two comments in regards to your insulating practices though:
1- You should make sure you have a layer of air impermeable insulation against the rim joist, not just a "double layer" of rockwool. Using air permeable insulation against the rim joist allows for moisture to condense out on the cold intererior side of the rim joist which can cause problems. Putting rigid foam and some rockwool over that is fine though, and I've done that myself. I find I like the "safe'n'Sound" version of mineral wool for this, since it tends to be a little bit thinner and just seems like a good fit here.
2- You should really consider insulating the crawlspace walls. There is a good amount of energy savings to be gained by insulating at least down to the frost line. The idea is to at least insulate the coldest section of the wall here, and crawlspaces tend to have ONLY walls in that colder area near the surface of the exterior ground.
Bill
Bill-
I mentioned a double layer of 6 mil poly only because 6 mil is what is typically available at the Big Box or lumber yard. 10 mil will of course be better, but I have never seen it on the shelf at HD.
And as I said, a concrete floor is best, but a big cost not everyone wants to pay, but it is set it and forget, plastic needs to be checked every few years for cracking or rodent damage.
I know the argument for rigid foam again the rim joist, but I think one can also argue for a vapor open approach because the concern is not just moisture from from the inside but also from the outside, an over flowing gutter or a landscape contractor that piles mulch up against the sill and siding or an irrigation contractor that is clueless about the damage their sprinklers do every night spraying water on the house. If you have rigid foam up against the rim joist its going to trap all the exterior moisture and rot the sill/rim faster than condensation on the inside, so for these reasons I like vapor open assemblies at the rim unless the sill is a good 18" above grade and the house has 2 foot overhangs.
Agree with you on insulating the walls of the crawl, but most my clients want to spend as little as possible on insulation and when push comes to shove it makes more sense to put more insulation in other places in the house first, the attic, the walls of the house, the rim joist, an insulated door at the bottom of the bulkhead stairs to the basement, if after all that there are funds left over by all means insulate the crawl walls, but I think it gives you the least bang for your bulk as far as insulation goes.
Malcolm-
I guess if you have a vented unconditioned crawl space then you have to insulate the under side of the floor, but every crawl I have been in with an insulated ceiling has been full of mice and mouse poop so we have always brought the crawl inside the envelope and removed the ceiling insulation & insulated the rim only, the clients often notice the difference within days as far as comfort and smell.
As far as vapor open insulated sills, I'm basing it on my real world experiencing and have not yet seen a problem with vapor open sill insulation.
At one property we help take care of I have battled the irrigation sub for years over his sprinkler heads spraying on the house, the decks, wood steps, masonry patios, I have even gone so far as to duct tape the sprinkler heads shut, he takes the tape off, I put it back, he takes it off.
We were on a multi year job and I had many interactions with the landscape sub over the course of two years, I told him repeatably "dont pile the mulch up to my new siding, dont let your sprinkler heads spray on the house", told the homeowner all this and asked them to look out for it. A few months after we completed our work i went back to the job and what did I see? Mulch up against the house and sprinklers soaking the new siding.
What about a2x6 exterior wall with dense pack cellulose and no exterior insulation, just plywood and house wrap, Sheetrock on the other side, that assembly drys two ways, vapor open, its worked in my own house so far and was bone dry after 2 years when we opened up the north wall to add an addition. How would that be different that the rim joist?
Jud_Aley,
I hear you about insulating floors. Not my preferred method either. I've just been giving advice based on the assumption that MarcoD wants to proceed that way.
The significant difference between using permeable insulation on rim-joists and walls is that the walls have an interior air-barrier and vapor-retarder to stop the moisture getting at the cold wood or sheathing. Before the practice of using foam came along we used to use batt insulation, but sealed it behind squares of poly to slow the moisture getting at that first condensing surface.
I quite understand why you do what you do in the circumstances you encounter. I'm just not sure that strategy has much wider application.
Seems to me Marco is looking for anyone to tell him his plan is the bests option and is going ignore the fact almost every post disagrees and move forward regardless.
Insulating applied to the floor is only useful if you have a way to install an air barrier to keep the air from blowing around the insulation. Given the number of pipes, wires, ducts and supporting posts an affective air barrier seems nearly impossible. If somehow Marco does install an affective air barrier and insulation and leave the vents open his pipes are likely to freeze when it get cold.
Walta
Hi Walta,
I'm new to Green advisory. I don't like your opening sentence about my query. I'm trying to learn something. There are usually a number of ways to solve a problem and I am carefully reading all of them to educate myself. Thanks.
MarcoD,
Don't take it personally, that's just Walta.