Typar vs Zip

I was thinking about using the Zip R system sheathing on my house – removing old clapboards, insulating the wall from the exterior and then installing the ZIP R. I just attended a seminar with a Typar house wrap rep who basically said Zip was no good – is not surfactant resistant and not much more that felt paper glued to OSB. But of course this is coming from the Typar rep. Any thoughts on the pros and cons of each?
GBA Detail Library
A collection of one thousand construction details organized by climate and house part
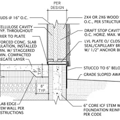
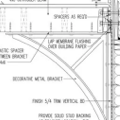
Replies
Michael,
For a full discussion of the pros and cons of a wide variety of water-resistive barriers (WRBs), including housewrap and Zip sheathing, see this article: All About Water-Resistive Barriers.
If you are worried that your WRB won't resist liquid water, the best improvement to your wall assembly is to include a rainscreen gap. The inclusion of the rainscreen gap is more important than the small differences in WRB performance between Typar and Zip.
For more information about rainscreen gaps, see All About Rainscreens.
Martin,
I was planning on using the Obdyke Slicker rainscreen, so it sounds like either product will work. Should I be worried about the surfactant claim by Typar or the fact that Zip is less vapor permeable? Or as I've read the permeability isn't all that important since whatever sheathing used in semi-permeable at best anyway?
IMO, both are good products, the Zip tape is awesome. I also believe that Zip R has the foam on the wrong side of the OSB, thus your awesome Zip tape better be installed perfectly. Unfortunately is usually installed with creases, bends, overlapped in the wrong direction, applied to dusty and/or dirty panels, etc., etc. As John said, it’s about a quality installation.
In our experience in the South and Southwest, I rather specify regular taped Plwd/OSB AND 1" taped rigid foam on the outside, for about the same price as the Zip R. If you tape the rigid foam with an approved taped, it becomes a WRB. Having said that, we install Tyvek for double WRB insurance. Nowadays, due to labor shortage, our builders may have to wait a long time to get masons or siders, so the Tyvek protects the foam.
The rainscreens we use are 1x4 for fiber cement siding, and Tyvek StuccoWrap and JumboTex60 for stucco and thin veneer cladding. Due to price, occasionally we use Slicker. Stone and brick get 1” air gap.
There are a plethora of YouTube videos conducted by Huber (ZIP) and DuPont (Tyvek) panning their competitors products. I know Tyvek isn't Typar but its a similar product. Here's my opinion based upon these videos.
A: Overdriven/improper fasteners with both products can cause bulk water to seep through the sheathing into the wall cavity.
B: Improperly applied tape with regards to both products can allow bulk water to get into the wall cavity.
C: Neither product is waterproof (in fairness I don't think either claims to be) so bulk water that is being applied constantly and never ending (an unlikely scenario imo) will soak through.
D Warranty. Huber offers a 30 yr warranty whereas DuPont offers a 7-10 yr warranty (I don't remember which) for their Tyvek product. What warranty does Typar offer?
My biggest takeaway from these videos is that paying attention to details and experience most regardless of which product is used.
My two cents.
Michael,
Q. "Should I be worried about the surfactant claim by Typar?"
A. In my opinion, no -- especially if your wall assembly includes a rainscreen gap.
Q. "Should I be worried about the fact that Zip is less vapor permeable?"
A. The permance of the sheathing sometimes matters -- especially if the sheathing isn't protected by a layer of continuous insulation on the exterior side of the sheathing. Sheathing permeance matters more when walls are very thick -- for example, in a double-stud wall -- than when a house has a conventional 2x4 or 2x6 wall. If you are worried about sheathing permeance, you could choose a sheathing material like fiberboard or gypsum sheathing. For more information, see these three articles:
Wall Sheathing Options
Monitoring Moisture Levels in Double-Stud Walls
How to Design a Wall
Q. "I've read that permeability isn't all that important since whatever sheathing used in semi-permeable at best anyway?"
A. Again, some types of sheathing (diagonal board sheathing, fiberboard, or gypsum sheathing) are much more permeable than OSB or plywood. That fact sometimes matters.
So with possible concerns about vapor permeability of the sheathing, inward solar drive, etc. - the house is in climate zone 4 - I'm planning to remove the old wood siding, spray foam the walls (full 4" studs) with Thermoseal 1200 open cell which will give me a cavity R value of 21.5 +/-, then Zip R 1" sheathing with an R value of 3.6, then the Obdyke slicker rain screen and either cedar or fiber cement siding. Any concerns with code compliance on r value, moisture in the walls, wet sheathing, etc.?
Michael,
No particular concerns with your plans.
If you're re-applying clapboards, why do you think you need the new layer of sheathing that comes with the Zip? You could just insulate and then screw vertical strapping through the insulation into the studs for clapboard nailing. Thus getting rid of the time and expense of both the Zip and the Obdyke, and ending up with a more robust rain screen with easier nailing (Obdyke and clapboards can be a pain in terms of consistent nail drive depth).
Oops - just read your last post. Didn't see you were removing sheathing. In that case, the Zip-R makes more sense.
I would, though, recommend playing with some Obdyke before committing to a whole house of it. We typically only use it for shingles - with clapboards we find it easier to set vertical strapping. Could be either 1x3 spruce strapping or just strips of 3/8 or 1/2" ply if you want a thinner rain screen.
The house actually doesn't have sheathing now, clapboards are nailed directly to studs. I'm taking it back to the studs to re-insulate from the exterior, then adding the Zip-R. Thanks for the insight on Obdyke - I had thought about vertical strapping but with the 1" sheathing I'm aready thickening the walls so I was mainly using the Obdyke to keep the rain screen thinner. I believe it's 1/4". But maybe ripping some 3/8" plywood would work. Any concerns on the plywood, would you think it needs to be more of a marine grade?
"But maybe ripping some 3/8" plywood would work. Any concerns on the plywood, would you think it needs to be more of a marine grade?"
- No need for marine grade because the strapping will easily dry whenever it gets wet.
No, if don't reasonably well it should stay dry. And of course the whole point of the rain screen is to let things dry out. including the rain screen itself.
Any advantage to using a product like the Cor-A-Vent SV-3 strips instead of wood? More expensive I'm sure but appears to offer some advantages with air flow through it in both directions, integral bug screening. etc.
I haven't used it. I'm sure there are, but whether it's worth the added expense and labor I can't say. It's easy to get too obsessive but its function is pretty simple.
Following up on an old post since I've done some additional research with a couple more questions. The house has original plaster walls on the interior with plaster lathes and I would spraying against with the open cell spray foam (from the exterior). I'm not sure how vapor permeable plaster is but will adding ZipR over open cell spray foam result in a double vapor barrier issue? Would close cell be better?
And a separate question - with the Zip-R at 3/.6R is 4" of spray foam overkill or would dense packed cellulose be just and good and less expensive?
Thanks again for all the comments - just trying to get this right the first time.
Michael,
If you are installing ZIp-R sheathing, you can install either open-cell spray foam or closed-cell spray foam between the studs. Neither option is better from a moisture perspective (although closed-cell spray foam obviously has a greater R-value per inch).
I'm not sure what you mean by "Zip-R at 3/.6R." There may be a typo in that phrase.
If you are trying to decide between closed-cell spray foam and cellulose, you may want to read this article: Installing Closed-Cell Spray Foam Between Studs is a Waste.
Still researching this re-side/re-insulation project, hoping to complete the work in summer 2019. One more question regarding the entire system. I've decided on removing the vinyl and wood clapboards, installing medium density open cell spray foam (Thermoseal 1200), 1" ZipR, 6mm Obyke Slicker Max rain screen (Slicker Max to reduce compression) - then a siding material. Still trying to decide on the material. I had settling on Boral TruExterior but they stopped making the bevel siding.
1920, 1 1/2 story house in climate zone 4 with an unvented attic (spray foam under the deck).
My question is - with an unvented attic and spray foam in the walls, will the house be too tight and will we need an air exchanger added? We will be keeping the original 1920 double hung windows with exterior storms but we're in the process of making those a little more air tight as well. Although I think they'll still be a little leaky when we're finished. And we'll still have the window weight pockets basically un-insulated (except for some thin rigid on the exterior) although I hope to make then air sealed from the exterior.
Will our house be too tight in the end? We don't want to do something we regret later. Thanks
Tighter is always better. Regarding ventilation, it's far better to measure (with a blower door) than guess.
I agree with Jon. Why not test? And with all of the air sealing you are doing, why not plan on bringing in some fresh air in a controlled and efficient way instead of planning to rely on leaks. There's plenty on the site to read about this topic. Start with these:
https://www.greenbuildingadvisor.com/article/do-all-houses-need-mechanical-ventilation
https://www.greenbuildingadvisor.com/article/five-ways-to-do-balanced-ventilation
https://www.greenbuildingadvisor.com/article/spray-foam-insulated-homes-need-ventilation