Two layers of insulation or one?

We are installing 2″ of Hi-load XPS rigid foam insulation under a heated slab in zone 4a and we have the option of doing 1 layer of 2″ insulation or 2 layers of 1″ insulation. I’m wondering if there is an advantage to overlapping the seams or if it’s inconsequential at the end of the day. We will be taping the seams.
thanks,
bigern
GBA Detail Library
A collection of one thousand construction details organized by climate and house part
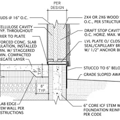
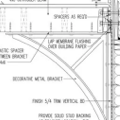
Replies
First, it doesn't have to be high load foam under slabs- even 15psi foam is more than sufficient, even if you're parking a Caterpillar D10 on that slab. You don't need anything like 2lbs or 2.5lbs density goods, 1.5lbs is enough. (Under a foundation wall footing it would usually need a high load foam, but you would have to engineer both the footing and the foam to make that work.)
Then, XPS will drop in performance to that of EPS of similar density well within the lifecycle of a residential slab. So for the longer term even 2lb XPS is only going to deliver about R8.4, not R10 or whatever. And even R10 is on the skimpy side if you're using the slab as the space heating radiator.
Worse still, the reason for the performance loss over time is that it is losing it's HFC blowing agents, which are powerful greenhouse gases ( more than 1000x CO2 @ 100 years.)
EPS is blown with pentane (7x CO2), most of which escapes from the foam at the factory, often recovered and burned for process heat, converting it to water and CO2. It's performance is not affected by the blowing agent and is stable over time. It's the same polymer as XPS, just processed differently. At 1.5lbs density (recommended) or 2lbs density (sometimes preferred by radiant heating pros due to better staple retention), it's performance runs about R4.2/inch forever.
Since it's simpler to manufacture, EPS is cheaper per R than XPS. Even 3" (R12.6) is usually comparable to or cheaper than 2" of XPS (R10), and that would be the LEAST amount of foam to use in a radiant slab in zone 4A, unless you're betting that energy prices in the future will be substantially cheaper than they are today. Taking it to 4" as a potential energy price inflation hedge isn't necessarily insane under a heated slab, but if there is a payoff for that last inch it's pretty long at current energy pricing & equipment efficiency.
Finally (to answer the question you actually asked), two layers with seams over lapped and taped are better than one, since polystyrene foam insulation (all types) sometimes has long term shrinkage issues, and even a 1" seam opening up would have minimal performance issue if it's only half the R at that seam.
Big Ern,
As Dana explained, two layers of foam with staggered seams is better than one. If the cost is close, I would go with two layers.
If two layers of rigid foam is significantly more expensive than one layer, you may choose to go with one layer. It won't be a major problem if you do -- you'll get most of the benefit from the foam, even if it shrinks a little. In this application, air leakage at the seams of the foam is not an issue. So don't worry too much, no matter what you choose to do.
hi martin and dana,
dana, i really appreciate the in depth description but it has left me more confused than i started! I thought i was abiding by best practices using 2" under the slab but now cant get the idea out of my head that we should be using 3"! Or even 4"! The hiload was reccommended from the structural engineer when he heard we might be taking cars (or forks (rarely)) over the slab. Of course i would rather not spend the extra money if not necessary but i have had trouble figuring out what will work best for our application, ask 10 people get 10 opinions, right?
Big Ern,
When it comes to compressive strength, it sounds like your engineer is being extremely conservative. Type IX EPS and common XPS products like Dow Styrofoam or Owens Corning Foamular have a compressive strength of 25 psi. That’s more than many soils that are routinely used to support a footing and a house.
Here are links to two articles with more information on this issue:
Choosing Rigid Foam
Foam Under Footings
If your slab will have embedded PEX tubing for hydronic heat, it's going to be warmer than the average slab. That fact will increase the rate of heat loss to the soil below. For that reason, it's usually important to specify thicker insulation under a heated slab than a slab without hydronic tubing. I agree with Dana that you should install 3 or 4 inches of rigid foam -- eventually your energy savings will add up to the point where the energy savings pay for the cost of the thicker foam.
You can literally drive a large steel tracked bulldozer over a 4" slab with 15psi foam under it without cracking the slab. The concern about driving a car or a forklift over it is unwarranted. If your engineer doesn't agree (it's arithmetic not rocket science, but OK) Type-9 EPS (2lbs per cubic foot nominal density) is good for 25psi, any vendor, and still cheaper than 1.5lb XPS.
http://www.buildwithplymouth.com/eps_properties_spec_sheet.pdf
http://www.northwestfoam.com/fact-specs.htm
Type-2 is really good enough, and typically costs about 10 cents per R per square foot, installed. So for 3"/ R12.6 budget ~$1.25 per square foot, for 4"/R16.8 figure $1.65 /foot.
At 1.5lbs density Type-II XPS is more like 12-13 cents per labeled R per square foot, so for 2"/R10 figure ~$1.25/foot, but know that before 50 years is up it won't be doing better than R8.5-ish, whereas 3" of Type-II EPS runs roughly the same money, and would still be performing at R12.6.
Only if the house has SUCH a low heat load that the slab is barely running above room temp even on design day would 2" be enough.
If you have already run the preliminary heat load numbers for the radiant heat design, how many BTU/hour per square foot does the slab need to deliver?