Trusses and ceiling insulation and air infiltration elimination

Hello. We are building a new home at this time, and I am trying to maintain a Passive Haus standard. We are using ICF walls which will be easy to ensure an appropriate R-Value and infiltration value, but we are also using trusses. I would like to use cellulose totaling to about R-60 or more in the ceiling. I just am not sure of the best way to seal the truss overhang and ensure close to zero air infiltration in this situation. Please advise on good techniques on sealing the trusses.
thanks much.
GBA Detail Library
A collection of one thousand construction details organized by climate and house part
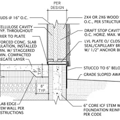
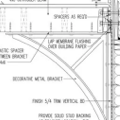
Replies
"We are using ICF walls which will be easy to ensure an appropriate R-Value..." It will? How are you going to accomplish that? I'm curious. On the R60 in the lid, are you sure that is sufficient for you PH goal?
The walls will have a total of 10 inches of EPS foam. 2 inner and 8 outer. This should put us in the vicinity of R40-45 wall R-value, then tne windows will be triple pane Serious windows, with U-values in the .24 range.
Raised Heel trusses with no overhang, sheathe, wrap & add overhang on after the fact (don't forget the attic ventilation - there are types you can cut into the roof sheathing to add)
Edit: Oops - slow typer... I also have to wonder how you are going to get the proper insulation levels for PH from an ICF - are they special ordered? Climate zone? Don't forget the insulation under the slab
Using at least 4 inches under slab. As for trusses will be working with truss engineer this week to design them.
Perhaps something similar to what Thorston did in the sunrise house? I'm picturing an airtight lid tied into the ICF system with trusses on top...
As Sean suggests, use raised heel trusses (20" to allow for vent baffles). Hang your ceiling drywall and seal over the top of your walls and drywall with an initial layer of spray foam. An inch or two of closed cell foam should do it. Then blow your cellulose.
Hi Mark,
If you really are targeting the 0.6ACH50 of the Passivhuas Standard and near the insulation values ( I can't tell without knowing your climate zone on the map at the top) , then the above answers regarding raised heel trusses and an airtight lid are proven methods to consider. The air-tight lid can be accomplished a few ways. The passivhaus projects that I've been involved with have used OSB panels on the bottom chord of the trusses taped at all joints and corners with SIGA Rissan 60 or equivalent. Another method would be an air and vapor control membrane like SIGA Majpell with battens and counter battens to hang the drywall below below.
At this point, you want to think about how your going to wire and light the area. If you're serious about the PH air-sealing requirement (or target in this case) then you might consider not depending on light cans in drywall as the air barrier. A service cavity is one of the most reliable and long term approaches. This means furring down from the OSB panels to run your electrical and mechanical services. Keeping the HRV ducting within the condition space can be done in this way.
If you want to take best advantage of your current design and get as close to the Passivhaus Standard as possible, think about discussing your project with a Certified Passive House Consultant. I'm sure one would be happy to consult on the energy side of the design without "derailing" your project.
Here is a national map of Certified PH Consultants: http://web.me.com/polytekton/CPHCstatesMap/CPHCstates.html
Good luck hitting your targets!
I am looking into suspended sheet rock for the lid, as done commercially. You then have as much space for lights, HRV, etc, as you opt to use.
Mark,
What stage of construction are you at? You wrote, "As for trusses, will be working with truss engineer this week to design them."
I really don't understand how you can be aiming for Passivhaus performance if these details weren't all worked out well in advance. You can't input numbers into the PHPP spreadsheet unless you know your thermal bridging numbers -- so how did you run the software if you are still working out the details of your house?
I am working with a truss engineer and another green building adviser. I am not using PHI consultants to help due to the costs (previously quoted after lectures). I am trying to maintain standards close as I can to PHI though via maintaining as many PHI techniques as possible. We are ready to dig a foundation as soon as a septic contractor is out of the way (on site). I did not use the PHI spreadsheet. I am simply trying to avoid thermal bridging and maintain the highest envelope R-values that I can afford.
The truss engineer will do anything I request from him so I can modify the truss design as needed. The other adviser is assisting in the physical construction, and compliance efforts (code, etc). I am trying to push the envelope to PHI standards - yes without hiring the PHI consulting company. I was quoted last year, a PHI design would cost 18,000$. So that would push the budget over the limit, and I am hoping/guessing about exactly how close we will get to PHI, but if I maintain construction standards that have been previously used is successful PHI homes, we should get pretty close.
$18,000 , my last project was an involved design, $9,500. Sounds like your quote may have included project oversight right to CO which mine did not. Still, I think you will do a good job your way. Use a blower door. Be wary of moisture issues with tight superinsulated homes.
Mark, there are some good suggestions above. Since you are using foam, go with spray foam on your ceiling drywall and use it also to seal up whatever you build for baffles at the exterior walls to truss area. Build in the baffles before sheathing trusses is how I would do it.
Just an update - I did mention that this was an ICF project. I originally designed it as a SIP constructed house using 12" EPS all around. But I was convinced that ICFs would do a better job sealing the walls with unbroken insulation through to the footing.
I had modeled the SIP ideas after another PH house I had viewed previously. Sorry at the moment I do not remember which one. Anyway, I just calculated the Square inch thermal pass throughs for both structures (SIP/ICF using overhanging trusses). The SIPs would have (in this home) about 7500 sq in. of thermal pass through (based on the sq inches of slab to SIP attachment 2X12s. Of course that could have been insulated with foam on the interior up the OSB wall prior to sheet rocking etc.. Comparing it to the ICF with overhanging trusses (for ease of construction), the total sq inches of wood passthrough (truss lower joist ends) based on a 2x6 truss bottom chord, would actually be less than the SIP connection to the slab. It amounted to about 5500 sq inches. The trusses would have 2 inches of eps inside under the truss, so the thermal barrier would be "pretty good" in my estimation. I have looked at truncating the trusses at the inside ICF concrete wall, then boxing, insulating, and then creating separate eaves to attach, but at the this time, the work effort seems like too much for a very small gain. I do understand that PHI would push for this, but the current plan calls for 16 inches outer to inner wall thickness, so the thermal pass through would occur over 16 inches of wood (truss lower chord). I do not truly know the R-value of 16 inches of southern pine, but without the inner truss foam sheathing, the square footage of this is approximately equivalent to 2 standard sized windows. Sure it is a fair amount, but add the foam, and consider the 16 inches of southern pine wood, then with standard wood insulation values (@1 / inch) then I get R16+R10 or so for the EPS liner, thus those sections would net about R26. Yes less than the whole wall, but for a small area, probably in my mind, acceptable. Thoughts?