To spray, or not to spray (Zone 3a SE, 140+yr. Historic 3 wythe)

Long time listener, first time caller here. Love the community and appreciate all of the contributions and support.
We have a renovation project underway in a ~140 year old 3 wythe MMU two story historic building located in South GA. It is a mixed use space, with the first floor commercial and second floor residential, and approximately 1800 sq.ft. per floor.
We are evaluating insulation options for 2 of the exterior walls on the second level and are restricted to interior only solutions. The plan so far is to frame a 2″x4″ wall 1 1/2″ away from the brick/plaster, insulate and cover with a smart vapor retarder, and then install perpendicular strapping to allow for electrical and drywall installation.
At this stage, the recommendations for insulation are all over the place, primary with foam type and where (sills/ceiling vs full wall cavity, etc.) and we’re struggling a bit, even with researching here, on how best to move forward with it. I’ve used mineral wool in other projects and areas of this building, love it, and plan to use it here as well. It’s just coming down to that same old question of open or closed cell, and where. I’d like to just use it to control air infiltration, but then it’s back and forth on water/vapor considerations. Were hoping the community can share some wisdom and offer some sound guidance and recommendations.
Some additional information on the building –
The first level walls will remain either exposed brick and original plaster, and the attic space is well vented and will remain so. Both levels will be conditioned with modern HVAC and the ceiling/floor separating the levels will be insulated with mineral wool and a smart vapor retarder along with new substrate and finished floor.
We will be applying siloxane to the exposed exterior walls to help with reducing water driving inward, as well as dealing with any tuck/point needs.
We realize humidity is a huge factor in our zone, and freeze/thaw cycles not so much. Air infiltration is another major factor to contend with, along with the variables of mixed use and overall age of the building.
I’m sure I left out a pile of other helpful details and will do my best to answer any questions. I really appreciate any feedback y’all have and look forward to hearing your thoughts.
Edit: corrected zone information.
GBA Detail Library
A collection of one thousand construction details organized by climate and house part
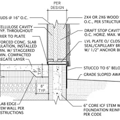
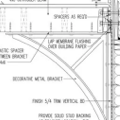
Replies
I don't have experience in your climate zone but I can say that Siloxane will help, but not stop vapor drive, and I would not want a very low-perm vapor retarder on the interior because it will keep the bricks damp. Concrete doesn't mind being wet. A building that age will likely have lime mortar, or it should, because the bricks are relatively soft, and lime mortar doesn't like being wet for extended periods. So I would allow some drying to the interior.
A variable permeance membrane (they are quite dumb, so I don't call them smart) between the brick and stud wall would be a good idea, with nothing stopping vapor drive on the interior side.
I would not recommend closed-cell foam. Open-cell would probably be ok, but it has no advantages over mineral wool. If you want to be "greener," wood fiber batts or sheep's wool batts would also work well.
Hopefully someone with more direct experience will weigh in.
Thank you, Michael, I really appreciate the feedback.
Understood on the Siloxane, the goal is to minimize, but to also allow for the vapor transition. For the retarder, MemBrain was recommended because it had a higher perm rating for our seasonal humidity needs. Because we're using a horizontal strapping and mineral wool bats, we weren't as concerned about it not being as strong as some of the other solutions.
A question for clarity regarding the wall assembly if I may. Our current design is: Exterior | Siloxane -> 3 wythe Brick -> lime plaster / sparge -> 1.5" gap (air-sealed top/bottom plates) -> 2x4-16" stud wall with mineral wool -> MemBrain -> Gypsum Board | Interior. Your comment is suggesting that introducing the MemBrain between the plaster and 2x4 wall would be viable. If that is the case, I'm guessing it would be best to not have the 1.5" gap and just fill that entire space with the rockwool?
We've just started reviewing another recent architectural design guide for MMUs and it recommends not having the air gap at all, and changing up the interior detail by introducing a fluid capillary break (~10 perms) on the plaster/parge, rigid mineral wool, 2x4 framing with mineral wool, MemBrain, and then the gypsum board.
Also, I appreciate the comment about not using closed-cell. I was fairly adamant about that with our GC but a few of the proposals had it as part of the assembly so we started second guessing our design. Our thought was to use the open cell foam for closing in the ceiling and floor in the 1.5" space to minimize air infiltration from the lower level and attic. That said, the air gap might not be viable at all.
It's been a lot to take in and a bit of a struggle to lock in a detail when the risk of a significant issue is high if we get it wrong. Again, thank you for the comments and we really appreciate the feedback.
I belive the guide is based on information from here:
https://buildingscience.com/documents/building-science-insights-newsletters/bsi-105-avoiding-mass-failures
You definitely don't want any vapor retarder outside the brick. There are lot of older buildings that got painted with oil and the results are not pretty.
Also watch how much insulation you add, colder brick can spall, less of an issue in warmer climate though.
I would go for wall one or six.
Thank you Akos, and really appreciate that link!
100% agreed on exterior. We will only be using the Siloxane outside, and focusing our effort on the interior.
I think you're right. The guide I was referencing appears to be recommending wall 7. I like the idea of the gap between the wood and masonry, was just concerned about the possibility of too much air infiltration from where the floors and ceilings meet the wall (they do not make contact), but maybe with the wall cavity and joist/rafter cavities being full of mineral wool it will be minimized enough. I want the assembly to be able to breath and just want to help control the amount of free (humid) air that is able to enter the space.
Again, I really appreciate the link, it's very informative and helping us better assess our options.