To foam or not to foam? — Basement insulation help desperately needed

I have been actively researching this topic for quite some time, and I feel that every time I finally determine the “proper” way to do it, another piece of contradictory information pops up. I am trying to determine correct method to insulate my basement walls. My home was built in 2007, and there is currently 2″ of XPS surround exterior of basement. All of basement walls are below grade. Going to be framing with 2×4 studs. I believe that I should be aiming for R20 total? Is that right? 15/19? Anyways, with the exterior presumable giving R10, would it be advisable to put xps against walls on interior, frame against rigid foam, and fill cavity with FG? Can I simply frame 1/2″ away from wall and put kraft faced fg? No moisture problems. Air temp in first floor is 69 degrees F, and in basement, it is 65.7.
Sorry to be all over the place, I am so confused. Some say vapor barrier, some say the exterior xps is the vapor barrier. I figured you folks are the experts, and I’d love to put this issue to rest and get going on finishing my basement!
Thank you in advance.
GBA Detail Library
A collection of one thousand construction details organized by climate and house part
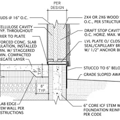
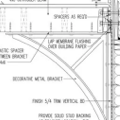
Replies
I apologize for not including in original post, but I am located in southern Wisconsin. That's probably important information!
In southern WI you're in US zone 6. IRC code min is R15 continuous insulation. Discount the XPS to R9 for a 50 year lifecycle average, even though it's labeled R is R10.
If you installed 2x4 studwall tight to the foundation and installed kraft faced R11 batts you'd beat code min. If R13 you'd be at about over R20 whole-wall.
If there isn't a capillary break between the footing and foundation and between the top of the foundation and foundation sill you could potentially have groundwater moisture seeping up the concrete sufficient to create a moisture problem for the studs, but if you put up a poly vapor barrier that could potentially push the moisture higher and compromise the foundation sill. If you're not sure, a layer of perforated1/4" fan-fold XPS over the entire foundation would still allow the concrete to dry enough to protect the foundation sill, but provide enough of a capillary break against the studs that they'll stay dry.
If the slab is not insulated, put an inch of EPS under the bottom plate of the studs, which is sufficient R to keep the summertime temperature of the bottom plate above the summertime dew point temperatures, keeping it dry enough to avoid mold.
Kraft facers are fine, but NOT foil facers or poly vapor barriers, which would trap ground moisture inside the studwall. No foil or vinyl wallpaper finishes, only standard latex paints. In a zone 6 climate, R9-R10 foam on the exterior provides more than sufficient exterior R for wintertime dew point control at the exterior side of R11-R15 batts, even if the first condensing surface were wood instead of concrete (or fan-fold XPS.) See:
http://publicecodes.cyberregs.com/icod/irc/2012/icod_irc_2012_7_sec002_par025.htm
Trace,
You are located in Climate Zone 6. According to the 2012 IRC, you need R-15 insulation of rigid foam for these walls, or R-19 if the insulation is installed in stud bays.
You already have R-10 insulation, so you either need to install R-5 rigid foam on the interior of your wall, or install a stud wall and fill the stud bays with fiberglass or mineral wool insulation.
I think that it makes more sense to install a continuous layer of R-5 (or more) rigid insulation on the interior of your wall, and to leave the stud bays empty, because I don't like to see fibrous insulation in a basement. (Basements can flood, and you don't want to have fibrous insulation if you have flooding.)
If taking a foam-only approach, unless you really need the studs for routing wiring, 1.5" of unfaced EPS strapped to the wall with 1x4 furring through-screwed to the foundation with 3" TapCons gets you there, and only eats up half the floor space.
Unfaced EPS would be preferable to XPS or foil-faced EPS/polyiso if the capillary breaks at the footing and foundation sill are unknowns. Putting more vapor-tight foam than that on the interior would be fine if there is at least 15" of above-grade exterior exposed concrete, decent roof overhangs, and good surface water management with the proper grading, drains, and backfill. This has been described as "All of basement walls are below grade." It's not clear how much of the foundation is above grade, or whether the above grade portion is also covered with 2" XPS. The 2" XPS is about 0.5-0.7 perms which is pretty vapor tight. At 1.5" unfaced EPS will be 2-3 perms depending on density. At R5 most XPS is in the 1-1.3-perm range, tight enough that the moisture content of the concrete near the foundation sill would be measurably higher. And in 50 years 1" XPS would perform at about R4.2-R4.5, whereas 1.5" EPS would run R6-6.3 pretty much forever.
Thank you all. In answer to a few questions, there is very little of foundation above grade, about height of the small window, maybe 2 feet, and yes, there is 2" of XPS there as well, protected with vinyl casing I believe. I did decide to follow Martin's suggestion of using R5,and will be putting up 1" XPS, and then studded with 2x4's. I chose that over the EPS, simply because I really need all the square feet as possible, and omitting framing not possible, as i need to run a lot of wiring. My wife and I both work from home, and will be utilizing as office space. So thank you so much for suggestions...but now I must ask. According to my interpretation (probably wrong) it looks like our code still requires a vapor retarder, regardless of XPS. Does that sound right?
According to Wisconsin State Code....
SPS 322.38 Vapor retarders.
(1) General.
(a) Definition. Under this section, a vapor retarder is a material with no intrinsic thermal or structural properties that has a rating of 1.0 perm or less when tested in accordance with ASTM standard E 96, Procedure A.
(b) Continuity.
1. The vapor retarder shall be continuous. All joints in a vapor retarder consisting of sheet material shall be overlapped 6 inches and taped or sealed, except as provided in subd. 2. Rips, punctures, and voids in the vapor retarder shall be patched with vapor retarder materials and taped or sealed. Seams that are not over a framing member shall be taped or sealed.
2. Taping or sealing a vapor retarder is not required around doors and windows, behind bathtub enclosures, and at top and bottom wall plates, if the retarder is held to those materials in an airtight manner by other building components, such as gypsum wallboard.
(2) Frame assemblies.
(a) General. Except as provided under par. (c), all frame walls, frame floors and frame ceilings that comprise the thermal envelope, shall have a vapor retarder installed on the warm-in-winter side of the thermal insulation.
(b) Coverage. The vapor retarder shall cover the exposed insulation and the interior face of the framing.
(c) Exceptions.
1. Where the vapor retarder is omitted, as allowed under subds. 2. to 4., all sources of air leakage, such as between double top or bottom plates or between double studs, shall be caulked or sealed.
2. No vapor retarder is required in the box sill.
3. No vapor retarder is required where batt insulation is provided with foil or kraft paper backing on the warm-in-winter side and the nailing tabs are tightly fastened to the warm-in-winter face of the framing members.
4. No vapor retarder is required over cavities that have at least 50% of the required R-value provided by spray-applied foam having a perm rating of 1.0 or less, unless required by the foam manufacturer.
5. A vapor retarder for a floor over an open, unheated area may consist of 5/8-inch tongue-and-groove oriented-strand board, or 3/4-inch tongue-and-groove CDX plywood, which is exposure-rated plywood.
(3) Concrete floors.
(a) Except as allowed under par. (d), a vapor retarder shall be installed directly under the concrete floor slab or under the base course of concrete floor slabs.
(b) Vapor retarder material shall be at least 6 mils in thickness or shall be a reinforced material.
(c) Joints in the vapor retarder shall be overlapped at least 6 inches and taped or sealed.
(d) A vapor retarder is not required under the slab of an unconditioned attached garage.
(4) Concrete or masonry basement walls. A non-rigid sheet vapor retarder with a perm rating of 0.1 or less is prohibited in all of the following locations:
(a) On a concrete or masonry wall which is below grade to any extent.
(b) On an insulated frame wall constructed in front of a concrete or masonry wall which is below grade to any extent.
History: CR 08-043: cr. Register March 2009 No. 639, eff. 4-1-09; CR 09-104: r. (3) (d), renum. (3) (e) to be (3) (d) Register December 2010 No. 660, eff. 1-1-11; correction in (3) (a) made under s. 13.92 (4) (b) 7. Register December 2010 No. 660; CR 15-041: renum. (1) (b) to (1) (b) 1. and am., cr. (1) (b) 2., am. (2) (c) 4., cr. (2) (c) 5. Register December 2015 No. 720, eff. 1-1-16.
Trace,
The code you quote reads, "A non-rigid sheet vapor retarder with a perm rating of 0.1 or less is prohibited in all of the following locations: (a) On a concrete or masonry wall which is below grade to any extent. ..."
With vinyl clad XPS on the above grade section you DON'T want to use XPS on the interior, or any foam with foil facers, since the conrete has ZERO capacity to dry toward the exterior. The concrete can withstand being saturated with water, but if there's any question about the vapor permeability of the sill gaskets the concrete should be allowed to dry toward the interior to protect the foundation sills.
1.5" EPS and 2x3 studs is a half inch thinner than 1" foam + 2x4 studs, has 2x the drying capacity, and won't lose performance over time. Using 1x furring would use only half the floor area of 1" XPS + 2x4 studs, 2x furring would still be reasonably easy for running the wiring and still an inch thinner than a 2x3 stud approach.
If studwall, don't forget to put some foam under the bottom plates, even if you don't insulate the studs.
What'd you end up doing? I'm in a similar predicament (also souther WI), except that I've already glued up and framed in front of the XPS and now the inspector is advising me it's a "vapor barrier" that needs to get torn out before I can proceed. I'm not one to go down without swinging, so I'm trying to build a case that the foam can and should stay.