to add or not to add, that is the question

I am finally getting around to making the attached garage of my house into a den. I knew it was 2×4 framing and assumed it was uninsulated. It had been my intention to remove the existing drywall and add 2″ rippers to the studs and fill it with R-19 batts (properly installed). Imagine my surprise to to find R-19 batts already in the 2×4 cavity and properly installed to boot! With the paper stapled to the face of the studs! The question is whether consensus would say it is most cost effective to leave it alone or whether I should stick to my original plan and firr out the studs. I’m afraid the 20 year old compressed R-19 will not “spring back” to fill up the newly deepened cavity. Would there be a problem adding the two inches and squishing in compressed unfaced R-11 on top of the paper-faced R-19?
GBA Detail Library
A collection of one thousand construction details organized by climate and house part
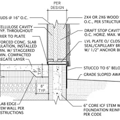
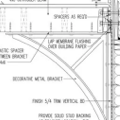
Replies
No problem, except it's more costly per R to compress fiberglass batts because you lose overall R-value.
The R-19 batts compressed into a 2x4 cavity (3½") provides R-13 and the additional R-11 batt compressed into a 2" space will provide R-7.5 for a total cavity insulation of R-18.5 or R-3.36 per inch.
You don't say where you are or what your climate zone is, but if you can afford to have someone blow dense-pack cellulose into the deepened cavities, you'll get R-3.8 per inch or R-20.9 cavity insulation and a much more airtight wall that won't attract insects and rodents, is far more fire-resistant and sound-proof, and mold-resistant as well (not to mention much friendlier to the environment).
Whoops. Math error. I must have hit the wrong buttons on my calculator!
The total compressed fiberglass R-value will be 20.5, about the same as the cellulose. So that would be a much less expensive option but without the many benefits of the cellulose.
Thanks Robert, about what I figured. I'm in Santa Fe -- 6000 HDD. I know about the cellulose but it seems a shame to rip out the perfecly good R-19 (albeit now R-13) and haul to the dump. What about having the Kraft paper now sandwiched between the fiberglass if I add unfaced R-11? By the way, I didn't know your advice was also for practical, non-life learning situations. Thanks again.
Kim,
As Robert pointed out, compressed insulation reduces the Rvalue by up to 45%. R18-20 in Santa Fe walls is kind of weak, specially assuming the house is 3-coat stucco and probably with a weak water management (as we did it for many years in NM); you really need to make sure the wall dries to the inside AND the outside as probably is already doing it. Cellulose is better Batt insulation for this application but higher $$$. I know you guys in SF are doing a lot of flash-n-batt (w/ open cell), and that could be a good application since it allows the wall to dry both sides but controls air infiltration.
Just to be sure there is no confusion: compessing a fiberglass batt reduces the R-value of the batt, but raises the R-value per inch.
Kim,
Most of my responses are technical in nature and based on 30 years of pioneering super-insulation and passive solar, healthy-home design, engineering and building as well as five years of teaching sustainable methods and materials.
I wouldn't assume that what you have are "perfectly good batts. Old fiberglass is generally riddled with mouse tunnels and various leavings or hiding mold from old leaks. You could be OK with the intermediate vapor retarder of the kraft paper, since it's approximately 1/3 way through the overall R-value of the wall assembly, but it would be worth checking out the status of the batts while you have the walls open.
At least here in New England, I've never opened up a fiberglass insulated wall and found the batts in good condition.