Tiny house subfloor insulation and moisture management

First, I want to thank you for all of the fantastic information you’ve put out on this site! The forums alone have been incredibly helpful in planning my tiny house design.
I’m at the point of buying materials and building the subfloor and I’m running into a couple issues that I haven’t been able to find answers to here, or anywhere else online.
I have a 24′ trailer with steel joists flush with the top of the outer frame. They’re on 16″ center running the width of the trailer and there’s steel flashing underneath the trailer that will let moisture out, but can support insulation.
My initial plan was to insulate between these joists and then use sill seal on top of them and put the subfloor straight on top of that. After reading more about the thermal bridging that would occur from the steel flashing to the joists to the subfloor, I decided to create a site-build SIP on top of the steel joists as is suggested in a number of tiny house posts on this site. I plan on putting sill seal on the joists, a layer of plywood (not sure if I need pressure treated to deal with moisture), 2″ of rigid foam and then a 3/4″ osb subfloor. Only the bottom layer of plywood will go under the bottom plate for the walls, the sections of the SIP above that layer will come out to the inside of the bottom plate.
My questions are:
1. Would I benefit significantly from insulating the cavity between the steel joists under this SIP sandwich in addition, or would the thermal bridge negate the majority of the utility of any insulation surrounding the joists?
2. Should I use some sort of poly barrier under the SIP to prevent moisture accumulation from causing problems with the bottom layer of the SIP or will sill seal be enough? (and should I use pressure treated plywood as the bottom layer?). I noticed someone mentioned that idea in this thread:
3. Do I need to create 2″ wood supports between the layers of the SIP to prevent compression of the rigid foam insulation? The exterior walls won’t be built on top of the foam, but cabinetry and built-in furniture will be. Would construction adhesive be the best option to glue all the layers together?
Thanks so much for your help and for this website!
Eli H
GBA Detail Library
A collection of one thousand construction details organized by climate and house part
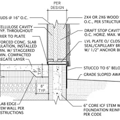
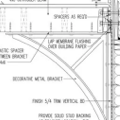
Replies
Eli,
You wrote, "There's steel flashing underneath the trailer that will let moisture out, but can support insulation." Can you be more specific? Is this sheet steel with perforations or holes to let out liquid water? Or something else?
If it is sheet steel with perforations or holes, what is the diameter of each hole, and how frequent are the holes?
Q. "Would I benefit significantly from insulating the cavity between the steel joists under this SIP sandwich in addition, or would the thermal bridge negate the majority of the utility of any insulation surrounding the joists?"
A. I would skip the insulation between the steel joists. It seems like it would just be an opportunity to house rodents.
Q. "Should I use some sort of polyethylene barrier under the SIP to prevent moisture accumulation from causing problems with the bottom layer of the SIP or will sill seal be enough?"
A. I vote for no polyethylene. (If liquid water ever trickled down to the bottom layer of your site-built SIP, the polyethylene would impeded outward drying.) Sill seal makes sense.
Q. "Should I use pressure treated plywood as the bottom layer?"
A. I don't think that pressure-treated plywood is necessary.
Q. "Do I need to create 2-inch wood supports between the layers of the SIP to prevent compression of the rigid foam insulation? The exterior walls won't be built on top of the foam, but cabinetry and built-in furniture will be."
A. No. Rigid foam can handle the compression.
Q. "Would construction adhesive be the best option to glue all the layers together?"
A. Choose a foam-compatible adhesive (in the form of tubes dispensed with a caulk gun). Read the label to make sure the adhesive is compatible with rigid foam.
Thanks for your response!
The steel flashing is made up of solid, 4' panels installed flush against the underside of the joists running the width of the trailer. They are welded for 2 inches every 8 inches all the way around, so moisture and rain while building can escape. Rodents wouldn't be able to access the interior of these cavities, but insects/ants probably will. It's tempting to caulk up the seams after getting the structure dried in, but that seems like it would create rust problems in the long run from moisture remaining in the cavity and not being able to escape.
Another reason I'm considering the pressure treated lower layer of plywood is because about 3 inches of the underside of the lower layer of the SIP will be exposed running the length of the trailer (aside from where the wheel wells are). This is because the main frame of the trailer is between the wheel wells and to extend the trailer beyond that, there are supports and angle iron at the trailer maximum width of 8'. The flashing underneath only extends to the main frame. My thoughts were that I could cover this gap with metal flashing on top and then sill seal and then put the SIP on top. I could also just cover it with a wide layer of sill seal or just leave it exposed and potentially later paint the underside with waterproofing paint once the structure is dried in. Which of these options do you think would be the best?
I'm leaning towards pressure treated 3/8" plywood, both for moisture and insect resistance in the the exposed sections as well as above the cavities between the floor joists. I am concerned about negative chemical interactions between the plywood and the connectors as well as the trailer itself. I was planning on using 4" long screws through the entire SIP into the trailer and then threaded rod through the bottom plate of the walls, the bottom layer of the SIP and the trailer. Is it worth it based on these considerations to go with pressure treated?
Also, would you recommend buying a large sheet of plastic or a large tarp to cover the whole subfloor until it's dried in? I noticed that Michaela had issues with trapping moisture in her subfloor in this post:
https://www.greenbuildingadvisor.com/community/forum/general-questions/41526/moisture-management-tiny-house-subfloor
I won't have the same assembly that she did, but I'm concerned about the bottom plate all the way around with sill sealer under it trapping water on the lowest layer of the SIP.
Thanks so much!
Eli H
Eli,
The underside of your floor won't get wet, except when your trailer is going down the highway on a rainy day. Do you expect to drive your tiny house a lot? Or just park it in one spot?
Unless this is intended as a travel trailer, I don't think you need pressure-treated plywood. It's true that pressure-treated lumber can be corrosive to fasteners, so that's a drawback to using pressure-treated plywood.
If you can't build your tiny house in a garage (under a roof), you should certainly invest in a tarp to keep everything as dry as possible as you build your house.
I won't be moving it much, so I'll go with the normal plywood and invest in a nice tarp. Thanks for all your help!