Tiny house subfloor

Hey there! I’m building a 2×6 subfloor on my tiny house deck, there is metal flashing 3″ below my subfloor and I am wondering if it is safe to insulate this 3″ with cellulose in a Zone 6 climate? Would condensation in the winter occur and get into the cellulose?
GBA Detail Library
A collection of one thousand construction details organized by climate and house part
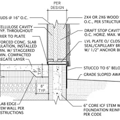
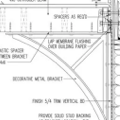
Replies
Michael, are you talking about a tiny house on wheels, and by "metal flashing" do you mean a continuous layer of sheet metal under the floor framing? If not, can you explain more or show an image of your proposed assembly?
Hey Michael, yes to both questions!
Michael, have you seen the other GBA questions on the topic? Every build is different but you will probably find an answer in one of these:
https://www.greenbuildingadvisor.com/question/tiny-house-subfloor-insulation-and-moisture-management
https://www.greenbuildingadvisor.com/question/floor-insulation-for-a-tiny-house-on-wheels
https://www.greenbuildingadvisor.com/question/tiny-home-subfloor-proper-layers-for-long-lasting-system
I've read them all but can't come to a consensus, can you give me your opinion? Should I leave an air gap of 3" or fill it with cellulose?
I have designed or consulted on a few tiny homes on wheels; so much depends on the project location, the installer's attention to detail and how much the home will be on the road that it's hard to give blanket advice. With that in mind, while I love cellulose insulation, I don't think this is a good location for it (potential settling, condensation, wetting from travel, etc.) I'd fill the cavities with mineral wool, and to limit thermal bridging which could lead to condensation, I'd consider adding 3/4" to 1" of rigid foam directly below your subfloor.
Okay, so 1" of rigid foam and 2" of mineral wool, but the problem is the mineral wool doesn't come in 2" thicknesses, only 3", would you do the full 3" in mineral wool or do it all in 3" foam?
The mineral wool between metal framing does almost next to nothing for the insulation. Depending on the gauge of the metal framing, you loose 50% to 60% of the R value from thermal bridging. The metal studs also become a condensing surface as they are cold and you might end up with mold under your cabinets.
So if you don't want cold, moldy floors, you need insulation above the metal. This does mean you loose a bit of ceiling height.
You can fill the floor with 3" mineral wool batts (safensound), install a layer of osb on the metal, rigid, another layer OSB on top as your final subfloor. There is no such thing as too much foam, if you are in colder climate about 3" is a good start. You can also do this by cross strapping + cut and cobble foam, but I think that is more work.
Thanks Akos. Your recommendation would be to put a layer of OSB/Plywood on top of the metal crossmembers, and then insulate on top? This would mean the 3" cavities would be filled with nothing correct? I am avoiding rigid foam due to vapour concerns and sticking to bio-insulation and/or rockwool. To clarify, I plan on building a wooden subfloor on top using 2x6 joists, this will on top of the cross members, using foam gaskets to prevent thermal bridging. I only recently thought about filling underneath with something for extra warmth
So:
3/4 subfloor plywood
2x6 joists
3/8 plywood
3" mineral wool
3/8 plywood
metal cross members
flashing
Is this correct?
I meant what Akos said--the foam goes above the metal framing, not between members. I'm pretty anti-foam but there are places it's warranted, such as this.
I just noticed that you're adding 2x6 members above the metal. That changes everything. The term, "subfloor" has a specific meaning in construction--it's a thin layer below the finished floor and over the framing. Your 2x6s are joists, not subfloor.
My suggestion was to fill the metal stud cavities, but it should not be your main insulation. You need real R value above the metal structure. If it is a lot more work, there is nothing wrong with leaving it empty.
If you have 2x6 joists, install 2x6 batts between those and call it a day. Insulating the floor pan does bump up your whole assembly R value by a bit, so it is worth it in cold climates.
If you have a metal floor pan, make sure you put in some drainage to allow for the inevitable water leak to find its way out.
I plan on flashing the bottom of my cross members with some galvanized flashing. I've just changed the design to have the cross members flush with the bottom, I will put foam on the members, a layer of 3/8" ply (or OSB if you recommend that) and fill that 2 1/2" cavity left with some mineral wool batts if possible, and then build the subfloor on top. If some water were to go to the bottom of the trailer at the moment, it would hit the metal flashing and have no way out due to the butyl tape sealing, should I raise up the OSB/ply from the metal members with a 1/2" furring strip to give some breathing space for the wood and the metal?
I sketch would work much better, not sure I follow your exact stackup.
Plywood has better moisture performance, so if you are going to move it on the road where it might get wet, go for plywood.
My drawing sucks, Does this make sense? Below the cross members there is the flashing, I forgot to draw it in
If you are not insulating between the cross members I wouldn't worry about floam blocks over it.
The layer of mineral wool does a good job of reducing the thermal briding of the 2x6 joists and does bump up the assembly R value quite a bit. Just make sure you get the rigid boards as regular batts are not stiff enough to support your floor assembly. You can also use rigid foam insulation if the rigid mineral wool gets expensive.
With this setup and the floor joist raised, the cellulose between the joists is fine.
I would also tape the first layer of 3/8 ply seams as well as the final subfloor. Air leaks through a floor reduce comfort much more than lack of insulation.
Hey Akos! Right! I plan on using a wooden runner down the cross members to provide support so the joists will only have to span about 5 feet (2x6). Mineral wool is about $150 more, but provides the fire protection versus foam which would melt, and I feel it's a better fit as I'm worried that a vapor barrier like rigid foam so close to the bottom could condense and cause moisture issues, what do you think? Yes! I plan on taping the seams using Tescon Vana :)
Did you do this yet? I'm planning a similar assembly. Did you end up using the furring strips to make space between the metal and the ply? If so, are you glad you did?
Also, I'm thinking about using a layer of housewrap between the ply and the metal frame, then some additional exterior insulation between the crossmembers of the trailer, and closing it up with horizontal metal flashing shingled with rainscreen at the seems to allow a bit of slope and an exit for any water that gets in there... any thoughts or recommendations? Could I use 2x4 to build up the floor to save the extra couple inches of headroom?