Thoughts on the Bensonwood OBPlusWall?

I’ve been a big fan of Bensonwood’s ideas and innovations for some time. They recently announced their new wall system, dubbed OBPlusWall. I’d love to hear some of the GBA community’s thoughts on this wall system, with the following considerations:
-Not sure exactly where the air barrier is… the Huber ZIP sheathing? Any knowledge or experience how Huber ZIP performs as an air barrier?
-If ZIP is the air barrier, and all insulation is inside the wall, does this pose a potential danger for condensation during the heating season? I suppose that if the air barrier is tight enough then it shouldn’t be a problem.
-Any idea how significant thermal bridging is with I-stud wall construction?
-Could a Passivhaus be built with these walls?
Thanks,
Ben Wilson
Columbus, Ohio
GBA Detail Library
A collection of one thousand construction details organized by climate and house part
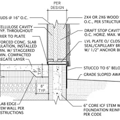
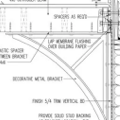
Replies
1) The inside sheathing over the I-stud is usually the air barrier for this type of wall system, though the ZIP sheathing/tape should also work well as an air barrier.
2) Repetitive thermal bridging through I-studs is roughly half that of conventional stud framing. It's still significant, and should be accounted for, but it's better than standard framing (from a thermal bridging point of view).
3) Passive Houses have been built with these types of wall systems in Europe and in the U.S., though you'd be hard-pressed to meet the Passive House heating standard in Columbus, OH with the R-values mentioned on the Bensonwood site (R-35 walls / R-38 roof). Check out the http://www.e-colab.org (the non-profit affordable housing
Any reasonable wall assembly with insulation is a candidate for a potential Passivhaus design.
The are several variables that must integrate into a complete thermal envelope, with appropriate mechanical support included, to achieve Passivhaus standards. The Passivhaus approach requires a designer(s) to design and model the thermal envelope and mechanical systems in there entirety. There are site specific circumstances the must be factored into the model. Whether a design meets PassivHaus is dependent on building orientation and any shading elements near the building.
R-35 can be sufficient R-value in milder climates. This wall system has the potential for the interior sheathing and exterior sheathing to act as effective air barriers. The air barrier within the field of the wall assembly is the easiest detail. Details that must be scrutinized for air tightness (and thermal bridging) include the wall to floor detail and the wall to roof detail. Passivhaus standards require the built assembly to demonstrate a .6 ACH.
The fact that the windows are installed in the factory will likely mean the overall design would not meet Passivhaus standards. Windows and doors have to be selected carefully and their installation into the wall assembly are critical details especially in colder climates.
I wonder if anyone can comment from field experience on how well examples of pre-fab walls and modular construction have performed for blower door tests. On average do they seem to complicate achieving air-tightness or make it easier?
One thing I have been thinking everytime Passive House is discussed; That a home that even comes close to PH standards is one heck of a improvement over standard construction.
And a Net plus home is even better than Passive House. And a house not built is even better still.
And stretching the topic just a touch; when will the world catch up to the smarts of China and implement public policy to reduce population? I would think mandatory reduction in births is desired verses World War lll or world resource collapse.
Go Passive House and any other way we can stay sustainable as a world community.
The Bensonwood OB plus wall has been developed to provide the next level of building systems in regards to thermal performance, combined with the effort to produce these building components off site. Our (Bensonwoods’)main goals are optimized structure, improved insulation, airtight enclosure and highest quality levels with tight tolerances.
In regards to the question for airtightness, we have seen that tight tolerances combined with the Huber ZIP systems and a European gasket system are an effective way to produce large sections of building enclosure (walls AND roofs) and assemble them fast. From the early days’ of using SIPs to now we have seen constantly improving Blowerdoor values. Recent tests on our projects show ACH50 ratings below 1. The Huber ZIP system can be used as reliable airbarrier, if applied correctly and with good care. Our air tightness ratings took a jump for the better when we started using ZIP about 3 years ago.
While I agree that detailing a Passivehouse challenging I feel very confident that using this wall system or a version thereof (depending on the location of the home, some aspects of the wall may vary) can achieve that standard. In fact we are building a house with that standard in VT this summer.
ACH50 below 0.6 is mandatory and will have to be achieved, in order to get the certification.
Installation and detailing of windows for a Passivehouse is a matter of how it is done, but not where it is done. Our experience is, that putting windows into the walls in the shop has many advantages and outweighs the concerns someone could come up with. It is a safe way to install and seal the window unit accurately and put it into place with the wall eliminating any challenges of handling these usually very heavy units (triple glazed with some times bulky euro frames) on a job site on pump jacks or aerial lifts.
There is no difference in the final performance of a shop installed window compared with a site installed unit.
I used to work in the German home manufacturing industry. Many certified Passivehouses are produced off-site in Europe every day. Bensonwood and I are confident that we can achieve the same.
Thanks for the response, Hans.
I am very inspired by what Bensonwood is doing. Your movement towards increased use of technology and modern manufacturing methods could lead the industry towards a goal of affordable, high-quality housing for the masses.
I would like to learn more about the gaskets used to seal wall sections. Could you provide a link to a manufacturer or white paper describing their installation/use?
I have seen more information come out about Bensonwood and I am taking notice. My first uncritical impression when I looked at their website was here is another production builder that may be overstating the quality of their product. I've been impressed by the additional information about their operations that have come out recently on this website.
In my prior post in this thread when I noted a concern with windows installed in the factory I meant that I was assuming that Bensonwood, a production builder, would likely be using a "production" grade window (i.e. a cheaper window to keep costs down) and not a quality window unit that is essential to meet PassivHaus standards. I didn't mean that installing the window at the factory couldn't be executed well (I can see how my earlier post communicated this incorrectly).
When I worked as a framing carpenter I saw many poor examples of prefab wall erections so I tend to be skeptical (and nostalgic of field framing), but it sounds like Bensonwood is legitimate and I hope to hear more about their field results in the future on this website.
Bensonwood (Ted Benson's operation in NH) has been producing high-quality timber frames for a long time, and they were one of the pioneers in foam panel enclosures. I lived for a while in Walpole NH and it seemed that every carpenter there at one time worked for Benson.
But they produce very high-end homes and their long-time focus has been on quality, not affordability. One of their frames costs more than a complete superinsulated home I built some years ago. Timber framing generically is expensive and often resource inefficient, since it typically requires either additional framing or the use of high-footprint foam panels to create a separate thermal envelope (though it could be wrapped or infilled with straw bales).
There are much better techniques for building efficient AND affordable homes, and they tend to involve less, not more, technology.
Ben,
Trelleborg is major Swedish manufacturer of EPDM building gaskets: http://www.trelleborg.com/upload/SealingProfiles/Catalogues/Standard%20products_EN_web.pdf
Their Sill Seal and ST Strip are commonly used. Conservation Technologies sells the Sill Seal: http://conservationtechnology.com/building_gaskets.html
Robert, (#7)
We are not perfect, but we are also not stuck in our past. Your memories of our company might be relatively accurate because we have built many high end homes. That clients want us to work at that level is a tribute to our quality standards and our very talented team. However, we are not wholly defined by those "patron" types of projects. We also build many homes without timberframes and affordability is indeed a major company objective. We've recently completed an 1100 s.f. home for $150K, turnkey; and another at about 2200 s.f. for around $250K. There weren't a lot of timbers in those projects, but our quality standards weren't compromised.
I would argue that the best quality standards come from knowing where to apply more technology and where less is better.