Cost-Effective High-Performance Building

I’m currently building a home in lower Zone 4 – just north of Chattanooga TN located on mostly north facing slopping lakefront lot. As I’m out in the county, no building inspections/codes other than electric and sewer. Two level, W/O, 2800 sqft. My goals, other than a -low maintenance required- place to live, are to build as close to a “pretty good house” as possible and stay within my budget. ($200 ft2 -site excluded) I am the builder – GC – and having experience in the building industry – a former working electrician (decades back), the process is well within my comfort level. I’m doing all but the framing, roof, basement walls – heavy stuff…. we start framing next week. What I’m finding – in this area- the green building concepts promoted on this site are somewhat a foreign language. “A house needs to breath” – I’ve heard a few times! As I navigate between the ideal and what makes sense for my climate and budget – my issue is the balance – face it- meeting green building goals – can be very expensive in comparison to the generally accepted residential standards of the area. Pay Back calculations can be depressing. What I’m doing: The basement walls – Superior Walls (waterproofed and insulated) – precast, and placed in 4 hours, on a 12″+ base of compacted gravel, uninsulated concrete flooring. 3/4 of the lower is below grade. Main will be 10′ – 2×6 walls, open cell foam, roof blown cellulose to R49. Airtightness is priority – but there are no testing means I can find – yet! I’m leaning towards Royal brand Haven BnB vinyl insulated siding around the main exterior, rock the exposed lower. Walls should approach R-19. Appropriate vapor and air barriers. Despite my preference for gas cooking, I’m going all electric, ERV ventilation, and mini split AC/Heat pump system. Solar is not a consideration given TVA culture. Window and large glass door assemblies are Jeld Wen Siteline’s U-26 SHGC – 20ish. Percentage wise $$$ of the budget. I believe my choices are leaning/keeping with “Green” building goals while keeping some sanity in the cost category. So – I am curious – how do the better minds among this site go about this balancing act – green building goals and the realities of building in the current environment within a conservative budget. Thanks for the time RB
EDIT – I’m really struggling with HW supply – the heat pump models seem really cool, but the added noise levels and my low electric rates leave me torn. When it comes time to actually make the purchase – we will see,
GBA Detail Library
A collection of one thousand construction details organized by climate and house part
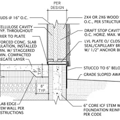
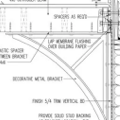
Replies
I think this kind of balancing act is exactly where the Pretty Good House idea comes from -- get most of the performance benefits for reasonable incremental cost. You can achieve quite a bit just by paying attention to details -- if you're going to be doing (or supervising) things like air sealing and insulation yourself, just getting those right is half the battle.
Thanks - and yes, air/moisture control is prime, insulation systems have kept me spinning the alternatives. Details, Details ... its all in the details, my largest priority/concerns are in this area -as were my window/door choices. With my views the plans include large viewing/entrance combo's so balancing cost and efficiency here was tough - cost lost out...
RB
I think you've come to the sobering conclusion that many of us know, whether we'll admit it or not. A lot of the materials are good, but heavily marketed and their cost can't be justified monetarily. For that matter, neither can most cars, trucks, clothes, phones, watches, or other consumer goods. It doesn't mean people shouldn't buy them, it's just that you wont save money by using them over something else.
The construction industry in the US is has been optimized (for good reason, we need houses people can afford to buy) to fit a certain style of building, from training the trades, right up to capping the last ridge shingle. That all fits together well to reduce costs, and make houses that are quite frankly good enough, though there's clearly a ton of room for improvement.
Once you break any part of that process, by doing things differently, or outside the norm, it starts a chain reaction of begging someone to try something new, ordering supplies from across the country because they're not stocked locally, and generally being dissatisfied with the end product, because of the difference of expectations between yourself, and those who are at least trying to accommodate by going outside of their comfort zone. That is unless you're working with a builder who has specialized in this type of thing, which is rare in this area. (I feel the TVA pain)
However, the outlook doesn't have to be grim, if you're comfortable managing the process, organizing all the material purchases and working with each sub, and doing much of the work yourself, it can be accomplished. $200 / ft^2 is a pretty good budget to work with. It sounds like you've given it a lot of thought so far, keep us updated on the process.
Kyle,
You summed it up nicely, better than I. I have come to manage my expectations - internally- trying to explain what I'm doing to other building trades folks has become exasperating - useless really - other than my framer - he gets it - as he is open to almost everything - my decision to go with 2x6 exterior on main was arrived at after discussing his process, and what I wanted to do with exterior foam board. More cost on the lumber side but offset by labor with the foam and other detailing. Plus, I can get 5.5 inches of foam on the inside, and some benefit with the insulated board batten vinyl. As for the sub's - he is a hardheaded old guy = wait that's me... After the framing and roof - it's all mine. I'll add the WWW is a great source of everything I may need to find or understand.
Edit- I spent way too much time with the person I initially hired to design/draw the prints - someone with lots of experience- I eventually just paid him for the useless work he did and drew up my own plans- changes were easy from then on....
Thanks for the feedback.
A ducted or ductless minisplit system? If ductless, how many indoor units?
Paul,
I am still developing this aspect of the build. As the lower level will not be completed until much later, and I will have the benefits of open ceilings/walls - making this choice later is cost neutral. I will probably use one of the Panasonic ERV's and one ducted mini split - need to feed the main living/kitchen area and the master bed / bath area. It is a very open design, large covered screened porch on main, porch below - we live outside a lot. I have toyed with two non-ducted mini splits......one for main open areas, and one for master living area. In any case - no more than two units in, and out. I didn't mention - I will also be installing my time-tested Woodstock wood stove on the opposite wall of the Kitchen/great room. I'm planning on its own fresh air feed - with damper control of flow. (I have an endless supply of wood fuel for this - and I should get green credits for sawmilling the trees I took off the lot.... I will use the Oak, Poplar and Walnut for outdoor projects) And yes, I have heard the admonitions to have this all figured out before starting - I just don't see the need in my case.
Thanks for the question.
Awesome, you’re on the right path there!
Hi Russell,
I think you will appreciate how Randy Williams—a builder and energy rater in Grand Rapids, Minnesota—handled exactly what you are asking about: A Code-Minimum Case Study. It supports just what Jonny_H said: "You can achieve quite a bit just by paying attention to details."
Yes - thanks I had read that article/post some time back - a reread is in order.
RB
The two most important tools I found were a calculator and spreadsheets. Doing cost comparisons on assemblies and maximizing how much work you do yourself will save you money. Shopping materials is required nowadays with material fluctuating so much. If you can buy material during the winter while costs are down do so. Pay attention to yearly increases on materials, which usually happen in the January through April range. We kept our Custom Timber Frame Pretty Good House, 3200 sf, basement walk out included at $150 a sf in Zone 5 with a lot more insulation.
I keep a spreadsheet on the cost/expense side - but trying to shop prices is beyond me now - I am building - now - and material availability is key - at any price some things are unattainable. You can get Pex A tubing - but try finding the expansion fittings. So, I'm staying with B and compression. I am dreading my start of the electrical material process. Given the new code - the cost of this system is double what it once was. Hope I can find the panels I want. We're framing next week - weather dependent - and TJI's suddenly became scarce - get them while you can, and as most everything has gone up substantially - I increased my target from $150 to $200. I fully expect to come nearer the $150, but hey- it's a brave new world.
Thanks for the input.
RB
You can use Pex A with crimp fittings, I'm not sure why people think iit is only for expansion connections.
@russell1313, I would LOVE to talk to you. I'm building close by in North Alabama and you're a few (ok, a lot) steps ahead of me.
Are you sure the pre cast foundation is worth what I assume is a higher cost? But it seems that ship sailed if you are framing next week.
I personally do not see spray foam as a good thing. I see it as a red flag for something in the plan that needs work. I fail to see what open sell spray foam does so well that it cost so much more damp sprayed cellulose with the same 3.5 Rs per inch. I never read a post about cellulose that failed to cure properly whit a stink that drove people from their homes. We do see that post about spray foam and I don’t see any reward given the risk.
I bought the “insulated vinyl siding” but not for its R value but because the vinyl was thicker and the foam made the siding rigid. When I look at most vinyl siding insulations, I see wavy panel and droopiness that I don’t see in mine.
Be sure to get an induction range you will not be disappointed.
I found building a BEopt model helpful when making economic choices.
https://www.nrel.gov/buildings/beopt.html
Walta
Walta,
There was not a poured wall contractor that would come to the area, too much business close to home with prices to match - block is almost as expensive, random quality, but still need waterproofing and insulation. Around here, the precast is now in the ballpark, and in the end, superior. If I can find a local damp spray cellulose contractor I will compare - I have a very good and reasonable foam guy - and I believe the air sealing is superior, and I want to seal all the rim boards and spaces, junctions, etc.
Induction - yea I've looked at a few - still like the flame though..... ahh progress.
Thanks for the input.
RB
+1 on the BeOpt model.
I haven't worked with damp spray cellulose. Is it vapor tight? I find spray foam has a place in assemblies that need to be vapor tight to be safe from condensation, particularly ones that are irregular and need a very good seal.
It's my experience that using Protecto Warp's Triple Guard is by far the best sealer. If you use regular sill sealer, I would make sure to apply two beads of polyurethane sealant, one on top of the sill sealer and one on the bottom, and finish off with liquid applied flashing at the bottom, after installing the sheathing.
On the openings, I recommend liquid applied flashing or a good stretchy tape, and also a good tape to flash the windows. The window sill frames need to have 1/4" slope.
We also use dense-packed cellulose on the walls and ocSPF on the rim joists on all jobs, and we've gotten around 1ACH50 on every job in the last 20 + years. If you follow good detailing, good sealing installation guides and YouTube videos (like Matt Risinger's), I'll guarantee you wouldn't need to use ocSPF on your wall assembly, unless it's what's available to you.
See: https://www.greenbuildingadvisor.com/article/product-review-worlds-best-sill-seal
Thanks Armondo - I was just looking for good sill and window sealers - very timely.
RB
Deleted