Thick foam board exterior insulation attachment

I live at the intersection of climate zones 5A and 6A in New Hampshire. I would like to add 8″ of reclaimed XPS insulation to the outside of a 2×4 wall with 1/2″ CDX sheathing. I plan to air and vapor seal the sheathing with a self adhering vapor barrier before applying two layers of 4″ insulation, w/ staggered seams. I have three questions:
1) Which is more preferable: a vapor permeable self adhered house wrap (such as Henry VP100, or Delta Vent SA) or an impermeable rubberized asphalt membrane w/ self healing properties for screw penetrations (such as Grace Vycor or Henry Blueskin SA), underneath the insulation? I am hoping as well to use a fluid applied weather barrier for the window bucks, and the ones I’ve looked into seem to be permeable for the most part. Please note the answer to this question may also be impacted by my final question regarding permeability of the house wrap water control layer on the exterior of the insulation, under the siding.
2) I recently saw a video from a Youtube channel “Ecohome”. Here is a link to the video:
At the 7 minute mark the presenter details their strapping method, and I’m wondering if this approach is viable when using layers of XPS insulation, as opposed to rockwool. Their approach is to strap the 1st layer of insulation horizontally, securing the strapping with screws through the rockwool insulation to the structural framing of the wall. The 2nd layer of insulation is then applied and strapped, but in this case the strapping is secured with screws to the 1st layer of strapping and not to the structural wall framing. I should add that I will be using nominal 1″ white cedar ship lap siding. Also the walls are open on the inside, so I could add studs at 12″ on center if I wish (they are 24″ on center as built).
3) Once I’ve applied both layers of insulation I would like to add Tyvek house wrap or commercial wrap to the exterior as the water control layer/ drainage plane. I am contemplating using two layers, with the outside layer being a sacrificial layer for UV since I’ll be doing this work 100% on my own. I had planned to tape the outermost layer as well. I actually have two questions, one regarding placement of the house wrap in the sequence of layers and the second regarding permeability. I don’t know if it makes more sense to apply this layer behind the strapping the siding will attach to, or outside of it. It would certainly be easier to attach it on top of the strapping instead of under, but I know that defeats the rainscreen benefit I would get otherwise. Perhaps I could help that by using a drainage style stucco wrap? I am also unsure what level of permeability this water control layer should exhibit, and I realize if I double up the house wrap, I’ll decrease the permeability.
Thank you everyone for any help you can give me. This web site with it’s members and administrators has been invaluable to me in my self-education.
GBA Detail Library
A collection of one thousand construction details organized by climate and house part
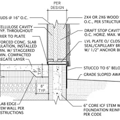
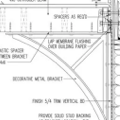
Replies
The vapor permeance of the WRB between the CDX & foam is irrelevant. At 8" anybody's XPS will be close to or even below the Class-I vapor retardency boundary. The assembly only dries to the interior.
Foam that thick can be awkward to deal with even on roofs, let alone walls. I can't recall seeing anybody's wall stackup that had more than 6" (which is awkward enough.)
The housewrap is easier to deal with and less likely to suffer damage if it's tight to the foam, under the furring.
If there are 1x girts holding the inner layer of foam to the studs, and vertical furring holding the second layer only to the inner girts there are several issues. The channel between the girts would be a thermal bypass channel of the exterior side foam (discussed at about 9:30 in the vidi) , and the structural capacity may be insufficient to handle the weight of stucco siding. You could fix the thermal bypass issue by ripping some 3/4" foam board to fit tightly between the girts or dado-cut the foam with 3/4" channels to accommodate the girts, but you'd still have to have an engineer spec the fasteners, furring & fastener spacing if piggy backing the exterior furring onto the girt furring rather than the structural studwall.
In your location with a well considered design you can probably hit PassiveHouse levels of energy use with a thinner wall than that.
Thanks, Dana, that makes sense.
Walter,
That seems like an awfully complicated, labor intensive, and risky wall assembly. Assuming that the reason for all of that foam outside of the house is because the walls are framed with 2x4s, would you consider furring them out on the inside with a strip of rigid foam and strapping, sometime called the Bonfig wall, named after the author of this FHB article: https://www.finehomebuilding.com/2014/11/26/breaking-the-thermal-bridge
With this approach you to get more cavity insulation and minimize thermal bridging. And you could go with less exterior foam and a more conventional installation, and I think less risk of the wall not performing as designed.
I expect that the thermal bridging caused by screws is far less than the video thinks it is and isn't worth addressing.
Yup- they need to show their math/modeling.
Assuming 8” long screws on 1 foot centers over a 4x8 foot section of wall (32 screws) and using 1/8” diameter steel screws, I show about 15.6 BTU/hr through the screws worst case (92 degrees F across the wall, which is about what he said is their worst case winter conditions with 70 degree indoor air temp). That’s a little shy of 0.5 BTU/hr/sqft.
The actual heat flow through the fasteners in the wall stackup they show will be something less than that since they have some kind of insulation inside the stud wall. My quicky “in the car at lunch between jobsites” calculation just assumes the fastener goes directly through from the hot side to the cold side of the wall, but in the actual wall there the fastener only goes from the cold side of the wall to the side of the insulated studwall that the exterior installation is attached to. That side of the studwall will be something less than the full indoor temperature of the house.
I was surprised at the energy transfer through the screws, but it’s still not very much in absolute terms.
Bill
> only goes from the cold side of the wall to the side of the insulated studwall
Insulating the end like this makes a huge difference when it comes to heat flow. This is not a case of a steel bolt through a steel SIP.
> will be something less than the full indoor temperature
Quite a bit less adjacent to the tip of the cold screw.
Attaching the siding and half the foam to the outside face of the first layer of foam makes me nervous. You have a lever arm attached to a lever arm.
Also 3/4" of bite is not enough for those structural screws. The wood may fail before the screw.
You might get away with a method like this when you're putting up pine or cedar clapboards because they weigh so little.
Fastenmaster publishes a manual on how to use their structural screws with foam insulation. I am pretty sure they have no prescriptive method for 8" thick foam.
As an aside, I have wondered how much stress the screws are under when you have 8-12" of foam on a steep pitch roof with a heavy snow load. It seems like there is a potential for an awful lot of load on those screws.
Note that the typical case for screws is that they don't see much shear force. The screws job is to press layers together and then friction between layers absorbs the shear force. Snow load adds to this friction.
On the other hand, foam (which suffers from creep) and rockwool (which can't take as much compression) might be exceptions. I expect that foam could be glued and once set, not need any fasteners.
I have, in the past, used metal tubes (cut sections of steel pipe) as sleeves around long bolts. I had to span through about a foot or so to put a structural mount for an antenna on the face of a false facade (some kind of stucco-like foam material with essentially no strength). The bolts clamp the mount against the wall and the pipes keep the bolts in tension so shear and creep issues are very much reduced. You need a strong bolt for this though since all the downward force is essentially converted to tension in the bolt. It works well and has held up for years. Something similar would probably work in the case of thick exterior foam.
Bill
Not 4” foam but this may give you some insight. Wish there was more detail on the foam fastening as layers went on.
https://buildingscience.com/documents/insights/bsi-056-leiningen-versus-the-ants-redux